SEA Electric and MEVCO sign MoU to electrify 8,500 Toyota models
SEA Electric and Mevco have signed a memorandum of understanding for the joint manufacture of 8,500 electrified Toyota Hilux and Landcruiser models for global mining operations.
A Toyota Hilux pickup, electrified by SEA Electric. Image: SEA Electric
SEA Electric has signed a Memorandum of Understanding with MEVCO, a leading systems integrator providing end-to-end service including electric light commercial vehicles and associated infrastructure within the mining industry.
8,500 electrified Toyota Hilux and Landcrusier models will be manufactured for the mining industry, with MEVCO committing to a five year deal with SEA Electric, in a deal worth close to AU$1 billion.
Mining companies have long seen the benefits of battery electric vehicles; predominantly in the form of vastly lower operating costs and increased reliability. Many new mines are also adding renewable energy, like this 34MW solar farm designed to reduce Rio Tinto’s costs - and in a small part - its emissions.
The deal is based around SEA’s medium-voltage SEA-Drive power system, which is light, cost-effective and simple, thanks to its lack of a requirement for an active thermal management system.
Available in various mining-specific designs for 4×4 and 4×2 configurations, the vehicles can be specified with two SEA-Drive options - an 88kWh battery with a quoted 380km (236mi) of range, or a 60kWh battery delivering up to 260km (160mi) of range. The system offers fast DC charging, topping up the battery from 10-80% in less an 60 minutes.
SEA Electric’s Toyota Hilux specifications. Screenshot - mevco.com
According to MEVCO CEO Matt Cahir, “This is a pivotal partnership for the mining industry…It enables the world’s leading EV technology for heavy and light commercial trucks to be commercialized on a scale that makes sense for the bespoke needs of the mining sector. SEA Electric’s unique architecture is perfectly suited for the task, with the system’s high-torque characteristics ideally fit for purpose.”
This announcement represents a big step forward for SEA’s expansion into the commercial vehicle segment, and it will hopefully demonstrate the company has the ability to be a world leader in electrified vehicle platforms.
There’s a certain irony that a company like Toyota - well known for being a BEV laggard - is being dragged into zero-emissions vehicles by a third party manufacturer, but it speaks to the ruggedness and suitability of its vehicles for industrial applications; if only it and other Japanese manufacturers would take full-fleet electrification seriously.
Renault-Nissan plan new electrified line up, US manufacturing operations as combustion engine investment dries up
With plans for 15 all-electric global models, and 23 electric-powertrain models total by 2030, Nissan has a lot of work to do this decade. Plans for EV plants in Sunderland, UK and Mississippi USA will see a massive investment in electric vehicle jobs and manufacturing.
The fully electric Nissan Leaf, Ariya and Townstar.
Nissan’s Ambition 2030 Plan has already called for 15 all-electric global models, and 23 electric-powertrain models total by 2030, and now the automaker has announced that it will not introduce any new pure internal combustion engine-powered passenger cars in Europe from 2023.
Nissan’s new electrified line-up promises “no compromise on excitement and driving pleasure” according to the company, and Nissan expects 75% of its sales mix in the European region to be electrified by FY2026, with the ambition to reach 100% by the end of the decade. It is targeting a mix of 40% electric vehicles in the United States for the same period.
Fully electric models include the Nissan Leaf, just-released Ariya, and Nissan Townstar, a fully electric compact light commercial vehicle.
Nissan hopes its Ariya Crossover will be a global sales success.
Hybrid models planned include the JUKE Hybrid, Qashqai e-POWER and X-Trail e-POWER. Nissan is also working on a comprehensive EV Energy Ecosystem, which explores initiatives to optimise and expand battery energy management capabilities. Nissan's flagship EV manufacturing hub, EV36Zero, based in Sunderland, UK – brings together vehicle and battery production, powered by renewables to set the blueprint for e-mobility manufacturing.
Nissan’s range of battery electric and plug in hybrid electric vehicles. Images: Nissan
Nissan to build two all-electric models in Mississippi
Nissan will also invest US$500 million to transform its Canton, MS assembly into a facility capable of building next-generation Nissan and Infiniti EV models starting in 2025. The partnership with local, county and state governments will preserve and upskill nearly 2,000 jobs according to the automaker.
Nissan has also set the goal to achieve carbon neutrality across the company’s global operations and the life cycle of its products by 2050 by pursuing further innovations in electrification and manufacturing technology.
The 2021 Nissan Chillout hints at the design of a possible Leaf replacement.
“For nearly two decades, Mississippians have kept our state at the forefront of the world’s automotive industry,” said Governor Tate Reeves. “The announcement that Nissan Canton is shifting some production to EVs further positions Mississippi as a leader in this crucial economic sector. We are a top state for automotive leaders, and this significant investment by Nissan in the Canton facility lets the world know that we are open for business and our workforce is ready to take on these in-demand jobs of the future.”
While South Carolina is the number one US state for auto and auto parts exports, Mississippi also generates a considerable amount of revenue and employs thousands within its auto industry. Companies such as Toyota, BorgWarner, Yokohama, Continental and Tiffin Motorhomes are based there, and Nissan has had a presence in Canton since 2003.
The highly-anticipated Nissan Ariya crossover is expected to launch in Europe during summer 2022, and Fall in the United States. Australian customers will have to wait until 2023 for a taste of car.
Polestar 5 electric sports sedan set to use revolutionary bonded aluminium platform
Polestar is working on an entirely new, faster manufacturing process that develops both body and platform in unison.
The Polestar 5 will closely resemble the Precept concept car.
The Polestar 5 — based on the Precept concept — is shaping up to be a technological tour-de-force, with the announcement from the automaker that the upcoming model will feature a revolutionary bespoke bonded aluminium platform.
Auto manufacturing is a constant juggling exercise, finding the fulcrum between low weight for efficiency and performance, and strength for safety. Aluminium is a lightweight material, but traditional welding techniques require additional metal for strength, somewhat negating the intended weight advantage. Bonded aluminium is light-weight and rigid, offering exceptional performance and “green” advantages, according to Polestar. We understand the process involves special adhesives and screws, rather than traditional welding.
According to Polestar, while this technology has previously proven labour-intensive and difficult to use in mass production vehicles without sacrificing quality, the company’s 280-strong team of former Formula 1, low volume and bespoke sports cars engineers in the UK have resolved the challenges associated with bonding technology by developing an entirely new, faster manufacturing process that develops both body and platform in unison.
Polestar 5 manufacturing process gallery
As a result of the new materials and techniques involved, the body-in-white (completed platform and body) is expected to weigh less than that of cars in smaller segments, contributing to improved vehicle efficiency, real-world EV range and dynamic responsiveness, all while delivering leading safety levels. The new bonded aluminium platform will also help drive faster product introduction, high quality and platform rigidity.
“Our UK R&D team is one of Polestar’s greatest assets,” says Thomas Ingenlath, Polestar CEO. “Their mix of engineering and technological expertise enables us to develop advanced, light-weight sports car technology with a creative mindset and a spirit that embraces innovative engineering. This will set Polestar apart in the years to come.”
By further developing this technology for Polestar’s first in-house platform, the 4-door Polestar 5 is being designed with torsional rigidity superior to that of a traditional two-seat sports- or supercar. The decision to develop a bespoke platform has also enabled the brand to deliver a production model that remains true to the Precept concept car that inspired it.
“We knew we wanted this car to be light-weight, we knew we wanted high quality and we knew we wanted it quickly,” says Pete Allen, Head of Polestar UK R&D. “This architecture delivers outstanding dynamic and safety attributes, with low investment technology applicable to high production volumes.”
Although without any distinguishing features in the above images, the Polestar 5 appears to retain the design character of the Polestar Precept concept, visible in the long hood, raked rear design and cut-off rear decklid. It also appears to be quite a large vehicle, when seen alongside a Polestar employee.
We expect the production Polestar 5 to be unveiled late 2022 - early 2023, ahead of a global market introduction in 2024.
Tritium Rings Nasdaq Closing Bell in Honor of Listing
Australian EV charging startup Tritium DCFC Limited began trading on Nasdaq on January 14, 2022, and it is expected the company will announce plans for a US manufacturing facility in the coming weeks.
Australian EV charging startup Tritium DCFC Limited began trading on Nasdaq on January 14, 2022, following the close of its business combination with Decarbonization Plus Acquisition Corporation II. On the afternoon of January 27, Company management rang the Closing Bell at Nasdaq MarketSite in New York’s Times Square in honour of its listing on the exchange.
“We are pleased to celebrate this important milestone for Tritium here at Nasdaq,” said Jane Hunter, Tritium’s Chief Executive Officer. “The transport industry is being electrified, which means it is more important than ever for EV owners to have access to rapid, reliable charging infrastructure. We are proud to provide this networked infrastructure to our customers. As a public company, we expect to continue to expand our product suite and global footprint, which has already enabled more than 3.6 million high-power charging sessions across 41 countries—delivering over 55 GWh of energy. I want to thank the Tritium team and Board of Directors, our investors, our partners at DCRN and our transaction advisors for their support and dedication through this process.”
Tritium embodies the Australian technology success story, and emphasises why investment in similar startups is critical. Founded in 2001 by e-mobility pioneers Dr. David Finn, James Kennedy, and Dr. Paul Sernia, the company draws on two decades of power electronics experience in the renewable energy field, and has well and truly established itself as a global leader in the DC fast charging space for EVs.
Tritium will look to have its US manufacturing plant up and running before the end of September, as it seeks to rapidly expand following the on Nasdaq. The company has been affected by global pandemic-related supply issues, and a stateside factory will go a long way to calming investors’ nerves around the continuing global transport delays and semiconductor shortages. Tritium had $US2 million (AUD$2.7 million) sitting in ships off the Port of Long Beach in December, en route from Australia, unable to dock.
German auto giants Mercedes-Benz and Volkswagen accelerate battery production plans
Daimler secures 33 percent stake in Automotive Cells Company alongside Stellantis and TotalEnergies, and JAC Volkswagen announces construction of additional battery factory in Hefei, China.
Following news this week that Ford has partnered with Redwood Materials to secure future battery component supply chains, we have an announcement from Daimler that Mercedes-Benz has secured a 33 percent stake in Automotive Cells Company (ACC), a battery cell manufacturer with a presence in France. The stake is estimated to be worth around $1.2 billion USD ($1.65 billion AUD).
Stellantis and French petroleum company TotalEnergies own 33 percent each. Automotive News Europe reports Mercedes-Benz CEO Ola Kaellenius has said “the purpose of the partnership is to develop cells and battery modules and “help ensure that Europe remains at the heart of the auto industry — even in an electric era.”
Mercedes-Benz will provide technology and production expertise to the ACC partnership, and aims to manufacture at least 120 Gigawatt hours of cell capacity by the end of the decade with its partners. The company is moving towards a modular, standardised battery “kit” that allows battery cells and modules from different manufacturers to easily fit with its range of components and interfaces.
High energy density, performance and charging power are key benchmarks for the project according to Daimler. ACC will primarily use renewable energy for its production facilities, and the batteries themselves will be over 95 percent recyclable.
ACC’s first new factory will be located in Northern France, and plans to be operational by 2023.
A rendering of JAC Volkswagen’s Hefei battery production facility. Image: Volkswagen
Volkswagen powers ahead in China
Meanwhile, Chinese joint venture Jianghuai Automobile Group/Volkswagen (JAC Volkswagen) will also have a new battery factory operational by 2023, located in Hefei city. Automotive News Europe states that the factory's initial capacity will be 150,000 to 180,000 battery systems a year.
This is the fourth battery factory in the works for the Wolfsburg automaker, with plants in Brunswick and Salzgitter Germany coming online in the next couple of years. A battery factory in Chattanooga, TN and at Volkswagen technology partner Northvolt’s Skellefteå plant should also be operational by 2023. Volkswagen plans to produce unified, modular cells like Mercedes-Benz for its scalable MEB platform architecture, and has flagged an annual capacity of up to 180,000 battery systems from its Hefei plant.
“With a significant increase of battery-electric vehicles in the future, we need to focus on keeping key components like battery systems in our own value chain, allowing us to leverage Group-wide synergies and innovations” says Stephan Wöllenstein, CEO of Volkswagen Group China. He goes on to say that “Volkswagen Anhui and VW Anhui Components Company, alongside our two strong Joint Ventures, are crucial to our electrification strategy and to achieving our goal of the Volkswagen Group China fleet reaching over 40% NEVs by 2030”.
Sources: Daimler, Automotive News Europe
Ford partners with Redwood Materials to recycle EVs, and provide battery materials
The deal will see the automaker work with battery recycling firm Redwood to create an end of life solution for electric vehicles, reducing environmental footprint and future cost of manufacturing, while ensuring Ford has adequate supply to meet projected battery demand.
Ford’s EV architecture will soon use recycled battery components in a deal with Redwood materials. Image: Ford
Ford is partnering up with Redwood Materials with a plan to create a closed loop supply chain system for its future range of electric vehicles. Redwood Materials is the brainchild of former Tesla CTO JB Straubel, and the company wants to address the problems of growing e-waste by developing an end-of-life supply chain to provide materials to battery manufacturers and automakers.
According to a Redwood Materials media statement, “we [Redwood Materials] need to start planning now for the end-of-life of batteries as we ramp up to build millions of EVs that can’t be disposed of safely without a robust recycling solution. The exciting side of this problem is that the critical materials inside of a battery are essentially infinitely recyclable. Unlike gasoline, the materials are not consumed or lost in their lifetime of usage in the vehicle.”
Ford has already seen success with its Mustang Mach-E, and as the electrified F-150 Lightning enters pre-production, the automaker is sure to see battery cell and component demand soar over the short-to-medium term.
Battery modules used in Ford’s Mustang Mach-E, manufactured by SK Innovation. Image: SK Innovation
Redwood Materials currently partners with battery manufacturers such as Panasonic/Tesla in Nevada, and Envision in Tennessee. The company received a healthy $700 million capital injection in late July, through a successful fundraising round from the likes of Baillie Gifford, Goldman Sachs Asset Management, Amazon and more.
Redwood plans to soon supply anode and cathode materials back to the American supply chain, and the company states that the deal with ford will span a vehicle battery’s entire lifecycle. To further advance these business opportunities between the companies, Ford has invested $50 million in Redwood to help them expand their manufacturing footprint.
It’s positive to see Ford thinking ahead like this; while many automakers like Volkswagen and Stellantis are simply scrambling to build up battery capacity to meet growing demand, Ford’s long-term strategic partnership should provide the company with an opportunity to not only secure enough materials to meet production demand, but reduce costs of production, and the associated environmental footprint.
Polestar highlights climate impact of the Polestar 2 EV, aims for environmental transparency
Polestar publishes the carbon footprint details of its Polestar 2 model range, aiming to lead the industry in transparency and sustainability through Life Cycle Assessments.
The Polestar 2. Images: Polestar
Polestar has just published full details of the carbon footprint of its latest models, in a move to improve transparency around the auto manufacturing process, and drive an industry-wide shift to sustainable mobility.
Tesla leads the automotive world with its Impact Report, published annually to highlight the company’s own sustainable mobility and energy push, and provide data from all aspects of the business including commodities sourcing, materials recycling, greenhouse gas emissions, and company workforce diversity.
Polestar’s Life Cycle Assessments (LCA) consider a range of factors in a car’s life cycle, from supply to manufacture to recycling, and summarise this climate impact in a single number.
Thomas Ingenlath, Polestar CEO, says: “Carmakers need to take full responsibility. Every week, we see a new announcement that an automaker is changing direction towards electrification. But going electric alone is not enough. Making cars electric is not the end game, it is a starting point. We need to be honest and transparent.”
Polestar wants to go further, and urges the industry to adopt greater transparency to rebuild consumer trust. Events like Volkswagen Group’s “Dieselgate” destroyed consumer trust in the group’s brands, and according to Polestar, recent research proves that only one in four consumers trust car manufacturers to be transparent and to operate in the best interests of society, and that over half of consumers demand more transparency and the ability to compare CO2 footprints between cars. Polestar says the adoption of an industry-wide standard could be the key.
The new LCA has found that the new Polestar 2 variants – Long range Single motor and Standard range Single motor – leave the factory with carbon footprints ranging between 24 and 25 tonnes of CO2e, a number that remains flat during the use phase if the car is charged with green energy. The existing Long range Dual motor’s footprint was previously declared to be 26,2 tonnes of CO2e in 2020.
“We are working towards net-zero production emissions, but our LCA shows that Polestar 2 is already a climate solution. EV technology provides a car with less than half the carbon impact of an equivalent petrol car if charged with green energy,” says Fredrika Klarén, Head of Sustainability at Polestar.
While the manufacturing of electric vehicles can result in emissions as high or even higher than internal combustion vehicles, we know that the life cycle emissions of EVs are a small fraction of internal combustion equivalents. The below graph from Polestar, showing the differences in the LCA score from renewable vs. non-renewable energy sources, demonstrate that the clean energy can effectively halve the score of each model.
View the LCA graphs supplied by Polestar below, and view the automaker’s sustainability goals and 2020 review here.
The LCA figures for the Polestar 2 range, with different energy sources.
A LCA comparison of the Polestar 2 Long Range Dual Motor.
A LCA comparison of the Polestar 2 Standard Range Single Motor.
A LCA comparison of the Polestar 2 Long Range Single Motor.
New South Wales government to add 35 electric buses to its North Shore fleet
The New South Wales Government has appointed Busways North West as the operator of bus services in Sydney’s North West and select areas of the Lower North Shore, and the company has committed to introducing 35 electric buses to replace diesel buses that have reached the end of their life.
A BYD-Gemilang-Nexport electric bus, currently servicing the Inner West of Sydney.
The New South Wales Government has appointed Busways North West as the operator of bus services in Sydney’s North West and select areas of the Lower North Shore, and the company has committed to introducing 35 electric buses to replace diesel buses that have reached the end of their life.
“Busways is an Australian-owned family company which currently runs bus routes, with integrated On Demand services, in Sydney’s West and the Hills District, and will now operate in the North West and Lower North Shore,” Mr Constance said.
“Busways will introduce 35 electric buses to replace diesel buses that need to be retired, meaning cleaner, quieter and smoother rides for customers. Charging infrastructure will be installed at the Willoughby depot to support the new fleet.”
Nexport is likely a contender to receive the purchase order. As a growing Australian business, with the company recently announcing a $110 million funding injection from Hong Kong-based financier Tor Investment Management, Nexport plans to partner with Australian technology giant Tritium —which is soon set to list on the NASDAQ exchange— to build EVs in Brisbane and the Australian Capital Territory. Nexport is already building buses using BYD drivetrains and Gemlang/Volgren bodies in New South Wales and Victoria.
We’ve reached out to Transport for New South Wales to get more information on the buses.
A concept of BYD-Nexport’s next electric bus. Image: Nexport
Mercedes-Benz announces electrification plan, EV and battery rollout, end of internal combustion vehicles
Mercedes-Benz has announced an end to its internal combustion-engined product offerings, moving towards a range of electric-only vehicles by 2030. Mercedes-Benz will cease the development and release of internal combustion vehicle architectures from 2025, launching three electric-only platforms in the same year.
Mercedes-Benz has announced an end to its internal combustion-engined product offerings, moving towards a range of electric-only vehicles by 2030. The caveat provided by the company is that zero-emissions vehicles will prevail “where market conditions allow”, presumably giving the automaker a guilt-free emissions pass in markets where charging infrastructure and EV uptake is yet to develop.
Mercedes-Benz will cease the development and release of internal combustion vehicle architectures from 2025, and will launch three electric-only platforms in the same year. According to the company, customers will be able to choose an all-electric alternative for every model in the Mercedes-Benz range, and that “Mercedes-Benz intends to manage this accelerated transformation while sticking to its profitability targets.”
Ola Källenius, CEO of Daimler AG and Mercedes-Benz AG said in a media statement that "The EV shift is picking up speed - especially in the luxury segment, where Mercedes-Benz belongs. The tipping point is getting closer and we will be ready as markets switch to electric-only by the end of this decade," "This step marks a profound reallocation of capital. By managing this faster transformation while safeguarding our profitability targets, we will ensure the enduring success of Mercedes-Benz. Thanks to our highly qualified and motivated workforce, I am convinced that we will be successful in this exciting new era."
Ola Källenius, CEO of Daimler AG and Mercedes-Benz AG with the Mercedes-Benz EQ range.
Mercedes-Benz’s Future Product Line-Up
Let’s look at the above image and get a sense of where the brand is heading this decade. We’re already familiar with the upcoming EQS luxo-barge next to Ola Källenius, and pictured to its right is the soon-to-be-revealed EQE sedan. Both vehicles are based on Mercedes-Benz’s Electric Vehicle Architecture (EVA) modular platform. Behind them, from left to right, we have the GLB crossover, and the currently on sale EQC and EQA crossovers. In the third row, a mysterious crossover —likely the EQS SUV— sits just ahead of the EQV.
Mercedes-Benz revealed its subbrands including AMG, Maybach and G-Class —made infamous in the 2010s as a symbol of gas-guzzling excess— will go electric. The EQS SUV will be the first vehicle in the lineup to receive the Maybach work-over, as teased in this image below.
The Mercedes-Benz EQS SUV Maybach. Image: Mercedes-Benz
All subbrands to go electric. Images: Mercedes-Benz.
Brand new electric platforms from 2025
Three electric-only architectures will be launched in 2025:
MB.EA will cover all medium to large size passenger cars, establishing a scalable modular system as the electric backbone for the future EV portfolio.
AMG.EA will be a dedicated performance electric vehicle platform addressing technology and performance oriented Mercedes-AMG customers.
VAN.EA ushers in a new era for purpose made electric vans and Light Commercial Vehicles, which will contribute to emission free transportation and cities in the future.
Manufacturing and battery cell demands
The upcoming mercedes-Benz EQB.
Mercedes-Benz plans to install battery cell capacity of more than 200 Gigawatt hours with partners, and sets its sights on eight Gigafactories to support this product rollout. The company will develop new partnerships for R&D and production of battery cells in Europe.
Following Tesla’s lead and in an attempt to reduce the bureaucracy and cost of development for legacy automakers, Mercedes-Benz is reorganizing its powertrain activities to put planning, development, purchasing and production under one roof. The company claims this will deepen the level of vertical integration in manufacturing and development and electric drive technology.
Mercedes-Benz’s next-generation batteries will debut in 2025 and will be highly standardized, and suitable for use across more than 90 percent of all Mercedes-Benz cars and vans according to the automaker. The company intends to focus battery cell and module manufacturing in Europe, keeping the supply chain close to home. It will work with technology partners across Europe such as SilaNano to further increase energy density in batteries through silicon- carbon composite anodes.
Mercedes-Benz is also developing solid-state technology, with an aim to create batteries with even higher energy density and safety. The company is already trialling Citaro buses with solid-state batteries.
EV Brief’s Take
This is all great news in our view. After a general reluctance to commit to electrification from Germany’s big automakers, Mercedes-Benz is officially going “all in”. Massive investment in capital works, battery gigafactories, and cell R&D, as well as ensuring reduced emissions and CO2 neutrality from the production process will allow the brand to get ahead of strict EU emissions regulations, while ensuring future commercial viability.
Streamlining its business through centralised production, common battery modules and shared platform architecture will not only lead to positive business outcomes and an increased return on investment, but it should also bring with it faster product rollout timeframes, and a greater diversity of product offerings.
Source: Mercedes-Benz
The Mercedes-Benz EQS.
Porsche aims to reduce CO2 in manufacturing process; asks component suppliers to green up
Porsche is asking its automotive component suppliers to switch to renewables, as the company is said to have set a goal of 100% carbon neutrality across its whole production chain within 9 years.
Porsche’s Taycan production line is already carbon neutral. Images: Porsche AG
Porsche is asking its automotive component suppliers to switch to renewables, as the company is said to have set a goal of 100% carbon neutrality across its whole production chain within 9 years.
The Zuffenhausen automaker has stated that Suppliers who are unwilling to switch to certified green energy will no longer be considered for contracts in the long term. Porsche’s supply chain is responsible for around 20 percent of the company’s total greenhouse gas emissions. This percentage is set to rise to around 40 by 2030 due to the increasing electrification of its model range.
Uwe-Karsten Städter, Member of the Executive Board for Procurement at Porsche AG said in a statement "By using only renewable energy sources, our suppliers are following our example in our efforts to reach CO2-neutrality. We plan to have even more intensive talks with our partners in order to drive forward improvements in our sustainability. It is only by working together that we will be able to combat ongoing climate change."
For its part, Porsche has been trying to reduce carbon emissions from its production sites. The automaker will be investing 1 billion euros in decarbonisation measures this decade, and its Zuffenhausen plant has been carbon neutral since 2019. Porsche’s just released Taycan Cross Turismo is the world’s first-ever carbon neutral vehicle according to the company.
Source: Porsche AG
Nexport to bring self-branded last mile electric van to Australia in October 2021
Australia's importer for BYD vehicles and electric buses Nexport has revealed that it plans to bring an all-electric commercial van to Australia, with customer test drives commencing in October 2021, and deliveries in 2022.
Nexport’s DLX electric van. Via Luke Todd on Linkedin
Australia's importer for BYD vehicles and electric buses Nexport has revealed that it plans to bring an all-electric commercial van to Australia, to be named the Nexport DLX. In a statement via Linkedin, Nexport managing director Luke Todd said that “Mass production in NSW will commence in early 2022. We will soon announce price and specifications....Nexport is creating jobs for Australians wishing to join the clean-tech manufacturing renaissance.”
Nexport DLX revealed on Linkedin
Earlier in the week, Todd also posted on Linkedin, stating “ARRIVED. Introducing the DLX electric logistics truck, the newest addition to the Nexport suite of zero-emission products. Customer test drives to commence in Australia by October 2021. Customer deliveries scheduled for Q1, 2022. No overhyped market build up needed. The DLX just arriEVd and will deliEVr.”
The use of “Arrived” references UK-based EV commercial vehicle startup Arrival, which currently has a similar electric van in development, with production to commence in the third quarter of 2022. Arrival has no plans to bring its vehicles to markets outside North America and Europe at this stage.
Nexport’s vehicles will eventually be manufactured in Australia
This is a very short but welcome timeline from Nexport; Australia’s transport emissions have grown steadily over the last few decades, and account for one-third of our greenhouse gas emissions according to the Climate Council.
Nexport already manufactures buses in Australia, utilising BYD powertrains and bus bodies from Gemilang and Volgren, so it’s possible that they are leveraging existing manufacturing capacity to bring the DLX to market so quickly. Another scenario could be that the company plans to “flat pack” vehicle bodies and drivetrain components, ready for final assembly on Australian shores.
Nexport has plans to eventually establish a passenger and commercial vehicle manufacturing facility in Australia, on a 51 hectare site 90 minutes south-west of Sydney. We have contacted Nexport for more information and will update this post accordingly.

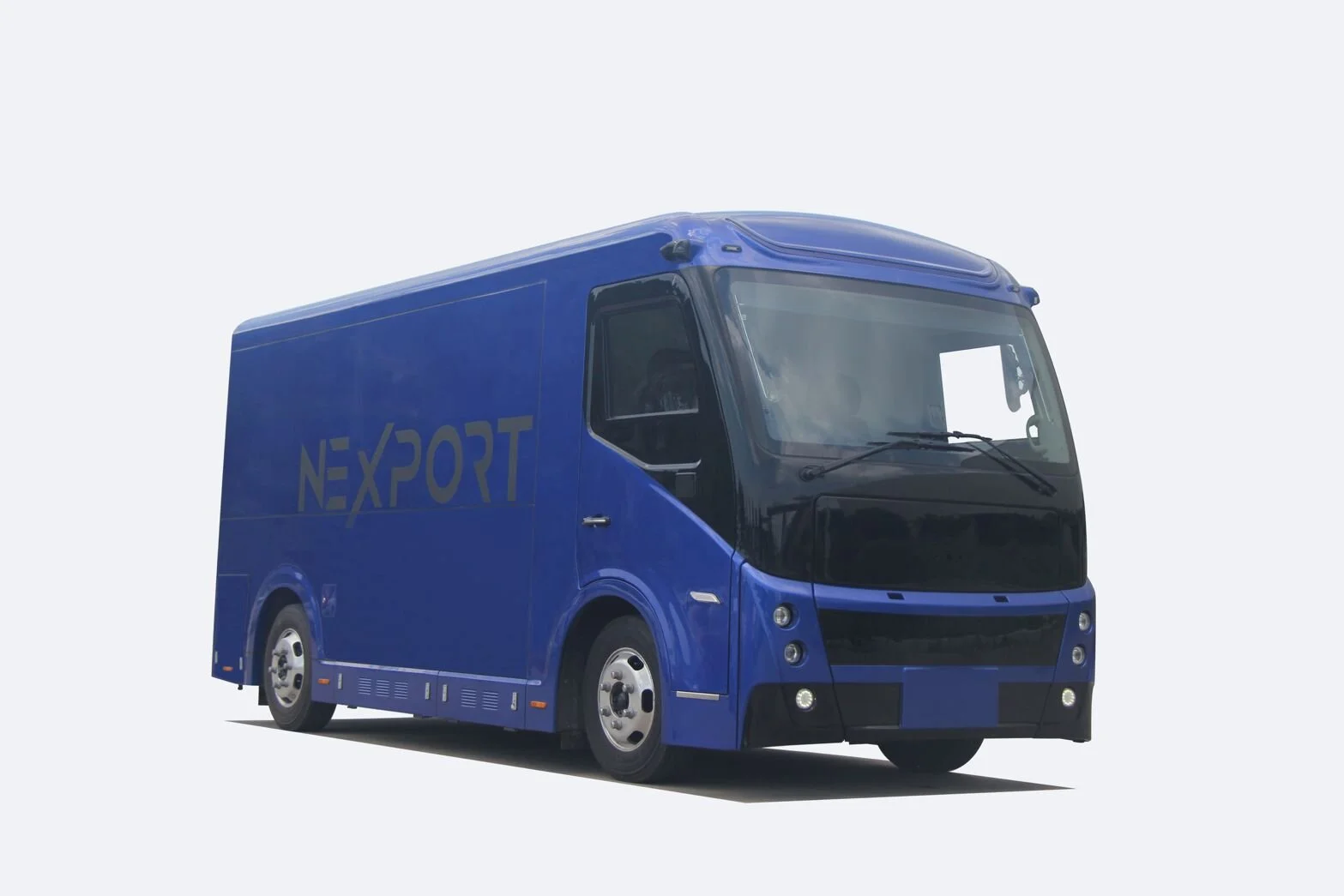



Source: LinkedIn
Porsche invests in Cellforce Group GmbH in the pursuit of high-performance battery technology
Porsche and joint venture partner Customcells today announced the launch of production for high-performance battery cells at the Weissach Development Centre. The announcement demonstrates Porsche’s continued technological innovation, and its commitment to e-mobility.
Porsche and joint venture partner Customcells today announced the launch of production for high-performance battery cells at the Weissach Development Centre. The announcement demonstrates Porsche’s continued technological innovation, and its commitment to e-mobility.
Oliver Blume, Chairman of the Executive Board at Porsche, Winfried Kretschmann, Minister President of Baden-Württemberg. Images: Porsche
“The battery cell is the combustion chamber of the future. As a new Porsche subsidiary, the Cellforce Group will be instrumental in driving forward the research, development, production, and sale of high-performance battery cells,” says Oliver Blume, Chairman of the Executive Board at Porsche. “This joint venture allows us to position ourselves at the forefront of global competition in developing the most powerful battery cell and make it the link between the unmistakable Porsche driving experience and sustainability. This is how we shape the future of the sports car.”
Porsche has been involved in the research of high-performance cells with silicon anodes for a while now; early research in this new battery technology has demonstrated it is possible to significantly boost the power density of cells compared to current batteries. New chemistry reduces the battery’s internal resistance, and it can offer the same energy content with a smaller footprint, and crucially, less weight. Silicon anodes effectively hold many more lithium ions, and they can move more freely than through graphite. An extra benefit is that lower-quality silicon can be used to no detriment, potentially making silicon anode Li-ion batteries cheaper than current graphite anode technology.
This graphic demonstrates how current batteries are charged and discharged. Image: Porsche
Porsche holds an 84 per cent majority stake in the new venture, which will be headquartered in the university town of Tübingen. The town is also a likely contender for a new battery cell factory, due to its proximity to the abovementioned development centre in Weissach and Porsche AG’s Stuttgart-Zuffenhausen headquarters.
The number of employees is expected to grow from the initial workforce of 13 provided jointly by both companies to up to 80 by 2025. The Federal Republic of Germany and the state of Baden-Württemberg are funding the project with around 60 million euros.
Michael Steiner, Boris Palmer, Torge Thönnessen, Winfried Kretschmann and Oliver Blume (f.l.t.r.)
“We founded Customcells with the aim of developing customer-specific battery cells for the most demanding of applications, and this is exactly what we can now realise together with Porsche. The goal for the planned production plant is to reach a minimum annual capacity of 100 MWh. This is equivalent to high-performance batteries for 1,000 vehicles,” explains Torge Thönnessen, CEO of Customcells. “We are not only contributing our expertise in cell technology and production into our partnership with Porsche, but also agility, innovative strength, and individual problem-solving skills,” adds Leopold König, who is also the new company’s CEO.
Source: Porsche
Former Canoo CEO to join Apple as Cupertino company works on Project Titan EV
The Verge is now reporting that Ulrich Kranz, co-founder and CEO of EV startup Canoo — and also formerly a BMW executive during the i3 and i8 development periods — will work on Apple’s electric vehicle program under former Tesla executive Doug Field.
Apple has had a large team working on its electric vehicle platform since 2014, which is codenamed “Project Titan”. After an initial focus on autonomous technology and systems, the company has reportedly pivoted back to vehicle development and has held talks with battery giants BYD and CATL. According to sources for Reuters, Apple is keen to develop a US battery factory with whoever signs on to the project.
The Verge is now reporting that Ulrich Kranz, co-founder and CEO of EV startup Canoo — and also formerly a BMW executive during the i3 and i8 development periods — will work on the Cupertino company’s electric vehicle program under former Tesla executive Doug Field.
Kranz even help talks with Apple during the development of Canoo’s EV platform, however talks between the two companies broke down as Apple was more interested in the acquisition of the startup rather than investing in the business.
The Verge has noted that Kranz was one of a number of top executives who have departed Canoo over the last twelve months, with the company’s first CEO Stefan Krause, and CFO and chief counsel also leaving the business.
Canoo went public on the NASDAQ in December 2020 via a SPAC deal, and is thought to have received close to $600 million USD from the deal. The company’s stock price launched at $22.82, and is currently trading at $9.76 at the time of writing.
Canoo is looking to fill a niche in the increasingly crowded EV market, by developing and building commercial electric vehicles for small businesses. Its Multipurpose Delivery Vehicle (MPDV) and Canoo Pickup are scheduled for launch to US-based customers by 2023.
Not much is known about Apple’s Project Titan, however it’s believed that the company’s focus on autonomous driving alongside a vehicle platform could lead the tech company to compete with Tesla, in the race to get a fleet of autonomous taxis onto the streets.
Canoo’s MPDV. Image: Canoo
Canoo’s Pickup.
Source: The Verge
Renault ElectriCity set to become largest electric vehicle production centre in Europe
Renault has announced the creation of a new electric vehicle production centre, grouping together three of its sites across the communes of Douai, Maubeuge and Ruitz in the Hauts-de-France region of Northern France.
Renault has announced the creation of a new electric vehicle production centre, grouping together three of its sites across the communes of Douai, Maubeuge and Ruitz in the Hauts-de-France region of Northern France.
The Renault ElectriCity plans to produce up to 400,000 vehicles per year, making it the largest EV production centre in Europe. Renault claims over 700 additional jobs will be created by 2025, including within a training centre and on-site university.
Renault Group and the representative trade unions have signed an agreement to bring nearly 5,000 employees within the single ElectriCity entity. Renault Group will also participate in innovation initiatives in partnership with start-ups to support future developments in the automotive world by participating in ‘Incubator’ type initiatives.
The Hauts-de-France region was chosen due to its technical and R&D know-how and experience in the electric car value chain. Renault Group will form partnerships with universities to set up training schemes to equip students with the skills necessary to work with next-generation EVs.
"I am very proud to have contributed to the creation of Renault ElectriCity, a symbol of Renault's know-how and technological innovation, and to participate to the enhancement of the economic and social attractiveness of Hauts-de-France in Europe. This agreement, signed with all the trade unions, is proof that the commitment of employees, constructive social dialogue and a strong local presence are key to setting up a robust and attractive industrial model," said Luciano Biondo, Director of Renault ElectriCity.
Key elements
Douai
The plant will produce its first electric vehicle, Mégane E-Vision, from 2021 on the Alliance's new modular CMF-EV platform
On the same platform, Douai will be assigned a new C-segment vehicle
A new electric platform dedicated to the industrialisation of B-segment vehicles will be installed
Maubeuge
A pioneer and leader in the electric van segment in Europe for 10 years with Kangoo Electric, the site manufactures New Kangoo, New Kangoo Van for Renault and its partners Mercedes and Nissan and will produce New Kangoo
E-Tech Electric in 2022
In addition, the plant will be assigned other variants of New Kangoo
Ruitz
The plant will host a new electrical components manufacturing activity
Hyundai Motor Group plans $7.4 billion investment in US manufacturing by 2025
Hyundai Motor Group (HMG), which includes Hyundai Motor Company and Kia Corporation, announced its plan to invest $7.4 billion in the U.S. by 2025 to produce future EVs and enhance its production facilities.
Hyundai’s new petrol-engined Tucson SUV on the production line in the Alabama factory. Image: Hyundai
Hyundai Motor Group (HMG), which includes Hyundai Motor Company and Kia Corporation, announced its plan to invest $7.4 billion in the U.S. by 2025 to produce future EVs and enhance its production facilities.
José Muñoz, Hyundai Motor Company’s Global Chief Operating Officer and President and CEO of Hyundai Motor North America said, “I am excited to make this announcement on behalf of the Hyundai Motor Group. This investment demonstrates our deep commitment to the U.S. market, our dealers and customers. Hyundai will lead the future of mobility in the United States and around the world. Our efforts are proof positive that Hyundai will continue to pursue excellence in our current and future product line-up.”
HMG plans to bring a range of American-made electric vehicles to U.S. consumers from 2022, starting with the Hyundai Ioniq 5 and Kia EV6.
HMG is also working with the U.S. government and other business partners to expand the U.S. hydrogen energy ecosystem. HMG signed an MOU with the U.S. Department of Energy in February 2020 to cooperate in hydrogen fuel cell technology innovation and global expansion. This included the installation of a hydrogen refueling station and providing NEXO SUVs.
HMG will also launch a subsidiary in Washington, D.C. to spearhead the Group’s Urban Air Mobility (UAM) businesses. The subsidiary will focus on creating an UAM technology ecosystem, and follows the group’s purchase of robotics company Boston Dynamics in 2020.
This vote of confidence in the U.S. by HMG comes after President Biden announced the acceleration of government spending to increase EV uptake, including $174 billion in incentives, tax credits, and rapid chargers.
Hyundai’s Montgomery Alabama factory. Image: Hyundai
Mercedes-Benz EQS sedan enters series production ahead of summer 2021 launch
The Mercedes-Benz EQS has entered series production at the company’s Factory 56 in Sindelfingen, Germany, alongside Mercedes-Benz S-Class and Mercedes-Maybach models.
Mercedes-Benz board members and executives celebrating the start of EQS series production. Image: Daimler
The Mercedes-Benz EQS has entered series production at the company’s Factory 56 in Sindelfingen, Germany, alongside Mercedes-Benz S-Class and Mercedes-Maybach models. The production facility is the result of over 730 million Euros invested, as Mercedes-Benz looks to rolling out its electrification strategy, and reducing its environmental footprint.
Factory 56 will be completely CO₂-neutral, thanks in part to a rooftop photovoltaic system and energy storage system based on reused vehicle batteries. Mercedes-Benz plans to use Factory 56 as an environmentally friendly manufacturing blueprint to transfer to its other vehicle plants worldwide.
Mercedes-Benz claims to have reached new levels of efficiency in the assembly process, due to high levels of digitisation and an MO360 digital ecosystem that focuses on providing the best possible support to its 1,500+ workers at Factory 56.
According to Michael Bauer, Site Manager and Head of Production of Mercedes-Benz Sindelfingen Plant, "With the EQS in our portfolio, we are once again proving the future viability of the Sindelfingen site: Here tradition is combined with a new understanding of innovation and sustainability. Thanks to our highly competent team, we have successfully completed the start of production of the EQS at the Mercedes-Benz Sindelfingen plant."
The EQS is set for a summer 2021 launch in Europe and North America, with other markets to follow late in 2021-22. Read more on the EQS in our launch preview.
Factory 56 at the Mercedes-Benz Sindelfingen plant. Image: Daimler.
Chinese automaker NIO plans NeoPark, an EV Industry Park in Hefei with $7.7 billion US initial investment
NIO’s founder, chairman and CEO William Li announced plans this week for a new smart electric vehicle industry park in conjunction with the Hefei municipal government at Xinquao, Hefei, Anhui province, about 5 hours west of Shanghai.
A concept rendering of NeoPark in Hefei, Anhui. Image: NIO
Hefei lies about 5 hours drive from Shanghai. Image: Google Maps
NIO’s founder, chairman and CEO William Li announced plans this week for a new smart electric vehicle industry park in conjunction with the Hefei municipal government at Xinquao, Hefei, Anhui province, about 5 hours west of Shanghai.
In a ceremony with Chinese government officials, NIO announced that it will be the first major manufacturer to be based within this world-class EV industry cluster, designed as a mega campus to house everything the EV manufacturing industry needs. The automaker has also committed 50 billion RMB ($7.7 billion US) to the initial stages of planning and construction.
NeoPark will be a hub for research and development, design, autonomy as well as parts and components manufacturing, and the concept allows for hundreds of key supporting enterprises to be able to function as an industry cluster within the park.
At 16,950 acres (over 11 square kilometers), the campus of NeoPark will contain manufacturing areas, research and development areas, living space, and an eco-park. It’s estimated that over 50,000 workers will be able to live/stay on campus at any one time, and Hefei plans to support the industry by providing policy support and funding, which, in turn, should attract more EV chain businesses and talent.
A NIO showroom within NeoPark rendered for the presentation.
NeoPark is launch before Chinese media.
Hefei will increase its support for the smart electric vehicle industry through funding, favourable policy and construction. NIO will be heavily involved in the long-term development planning of the park, and will introduce more EV chain businesses through establishing an R&D, corporate and manufacturing presence there.
NeoPark claims green credentials too, though the media event didn’t highlight any specifics at this stage.
NeoPark has the potential to realise an annual production capacity of 1 million vehicles and 100 GWh of battery storage according to NIO, and the campus gross yearly output could reach RMB 500 billion ($77.23 billion US).
Nio executives at the launch of NeoPark.
Xpeng P5 EV set for April 14 reveal; company posts all time quarterly sales record for 2021 [UPDATED]
Chinese electric vehicle manufacturer Xpeng (also known as XMotors.ai and Xiaopeng Motors) will reveal their P5 mid-size electric sedan online on April 14 at 2pm ET/8pm CET/4am 15/4 AEST prior to the media and public reveal at the Shanghai Auto Fair.
Xpeng’s upcoming P5 sedan
[Updated]: Chinese electric vehicle manufacturer Xpeng (also known as XMotors.ai and Xiaopeng Motors) will reveal their P5 mid-size electric sedan online on April 14 at 2pm ET/8pm CET/4am 15/4 AEST prior to the media and public reveal at the Shanghai Auto Fair. This follows the recent sighting of camouflaged prototypes undergoing final development testing on the streets of China, and the following teaser image from XPeng:
XPeng’s Chairman He Xiaopeng has hinted in previous discussions with Chinese media that the P5 will be the first production vehicle with Lidar technology — now confirmed in the above tweet — and that the P5 will be equivalent in size roughly to the Toyota Camry and Honda Accord (and obviously, Tesla’s Model 3)
The P5 carries the company’s contemporary styling cues, and appears to offer two driver displays in the interior. The vehicle architecture is shared with the company’s G3 crossover, and customer deliveries are expected to commence towards the end of 2021.
XPeng’s P5 undisguised. Credit: reddit.com/wyboongk
XPeng posts best ever monthly and quarterly sales results
Admittedly, XPeng’s 2020 sales didn’t hit expectations due to a number of factors—only 6 months of P7 sedan sales as well as the COVID-19 pandemic—but the company has posted strong numbers for this year, with 13,340 sales from January to March 2021, versus 1,419 for the previous period in 2020. The company sold 7,974 P7 sedans, and 5,366 G3 SUVs, and also surpassed a cumulative total of 50,000 vehicles.
According to XPeng, "The Company attributed the record quarterly deliveries to its growing brand recognition and product appeal, expanded product portfolio and its relentless efforts in broadening sales, marketing and supercharging service networks across China."
Xpeng is working hard to continue growing its sales as well as its brand in China, and faces stiff competition from BYD, NIO, upcoming Zhiji Auto and of course, Tesla. XPeng is growing its DC fast charging network across China, with over 935 sites across 139 cities available by the end of 2021. The company has also reached an agreement with NIO for customers of either brand to be able to share fast charging stations. In addition, Xpeng has brought in a lower-priced lithium iron phosphate (LFP) battery option from CATL, designed for city-based customers for whom a longer battery range is of limited value. Customers who opt for the LFP battery option can expect to save around RMB 20,000 ($3,000 US) per vehicle.
BYD achieves record new energy vehicle sales in China for Q1 2021, strong 2020 net profit
Chinese automaker BYD has had a strong sales start to 2021, with 53,380 passenger vehicle sales in the first quarter, comprising battery electric vehicles (BEVs) and plug-in hybrid electric vehicles (PHEVs). That represents a 148 percent increase over the same period last year.
BYD achieves 148 percent increase in NEV sales for Q1 2021
Chinese automaker BYD has had a strong sales start to 2021, with 53,380 passenger vehicle sales in the first quarter, comprising battery electric vehicles (BEVs) and plug-in hybrid electric vehicles (PHEVs). That represents a 148 percent increase over the same period last year, where 21,520 new energy vehicles were sold.
2020 sales were obviously heavily affected by the COVID-19 pandemic in China, but it’s important to see automakers in China returning to strong numbers, even in what is a traditionally quiet sales period after January’s pre-Chinese New Year sales rush.
March 2021 marks the seventh consecutive month of year-on-year growth for BYD’s new energy vehicle sales, and the company is continuing to innovate, with improvements to its in-house lithium iron phosphate (LFP) ‘Blade Battery’, including the claim of over 3,000 available charge cycles or 1.2 million kilometres from the new cells.
BYD’s revenue and profit soars in 2020
BYD has also posted annual revenue figures for 2020, and despite COVID-19, posted a revenue figure of 156.598 billion yuan ($23.87 billion USD). This represents an increase of 22.59 percent over 2019. Net profit attributable to shareholders also headed for the sky, with a 162.27 percent increase over 2019, to 4.234 billion yuan ($645.349 million USD).
All this despite the company’s 2020 output of new vehicles—including fossil fuel powered vehicles and commercial vehicles—declining 5.08% year over year:
BYD 2020 sales
Total new vehicle sales: 431,954 units (down 5.08%)
Total passenger vehicle sales: 394,608 units (down 3.62%)
Total new energy vehicle sales: 162,893 units (down 12.52%)
Total fossil fuel passenger vehicle sales: 231,715 units (up 3.81%)
Analysts have forecasted that BYD's net profit attributable to shareholders for the first quarter of 2021 is forecasted to reach 200 million to 300 million yuan ($30.482 million to $45.723 million USD), an increase of somewhere between 80 and 160 percent from the first quarter of 2020.
BYD is going from strength to strength, trouncing rivials NIO and Xpeng in sales volume (however both manufacturers also had strong first quarter results, despite lower volumes), and recently announcing a slew of new passenger vehicles for 2021 (which will exclusively use BYD’s in-house ‘blade battery’) and the expected unveiling of a new EV brand in the next few weeks.
The BYD Tang SUV interior. Image: BYD
Source: Gasgoo
Electric Chevy Silverado pickup gets green light, will be manufactured in Detroit
In a move set to anger coal-rolling pickup drivers yet guarantee the future viability of Chevrolet, the company has announced that a fully electric version of it’s popular Silverado pickup truck will be manufactured at it’s Factory Zero electric vehicle only manufacturing site in Detroit and Hamtramck.
In a move set to anger coal-rolling pickup drivers yet guarantee the future viability of Chevrolet, the company has announced that a fully electric version of it’s popular Silverado pickup truck will be manufactured at it’s Factory Zero electric vehicle only manufacturing site in Detroit and Hamtramck.
The fact that General Motors (GM) is going electric not only signifies GM’s commitment to electrification, but represents a significant future shift in the market. The Chevrolet Silverado is the second most popular new and used vehicle in the United States, selling close to 600,000 new units in 2020.
The Chevrolet Silverado electric will be a full-size pickup based on the company’s Ultium EV architecture, and according to GM will travel more than 400 miles (642 kilometres) on a full charge. General motors has committed billions not only to the new Factory Zero site, but also to electrifying its entire model line up, and its Ultium Cells joint venture with LG Chem LLC.
A release date for the Silverado electric is not yet known, but GM president Mark Reuss said at an event on Tuesday this week that the company will also make fleet-focused versions of the truck for commercial customers.
The current 2021 Chevrolet Silverado. Image: General Motors