Porsche Mission R electric GT car revealed; hints at future Cayman, Boxster models
Porsche’s new Mission R concept was revealed at IAA Mobility, and hints at the brand’s future design direction for track and production vehicles.
The Mission R hints at future electric Porsche styling. Images: Porsche AG
The Porsche Mission R concept vehicle is a GT-class electric racecar that is sure to either elicit elation or loathing from Porsche fans. It's got the looks and it’s got the power (800 kW or 1,088 PS to be exact), but petrol heads will bemoan the electrification of track-focused Porsches, and the lack of roaring flat six engines.
The exterior design explores traditional Porsche design elements; namely the four-point LED headlights, pronounced front and rear guards, and wide, full-length brake light. We love the cutaway guards at the rear, and the simplicity of the curved glasshouse.
We expect this design study to not only morph into a production EV racing Porsche, but also the next-generation 718 Cayman range with a fully electric drive train. The size and proportions are right, and Porsche could be hinting at future models with the Mission R. Porsche states that the Porsche Mission R is slightly shorter than the current 718 Cayman series.
An electric motor with up to 320 kW (435 PS) powers the front axle of the Mission R, while a maximum of 480 kW (653 PS) is delivered to the rear. The Mission R features 900-volt technology and Porsche Turbo Charging, which the automaker claims can charge the battery from 5 to 80 percent in 15-minutes.
The all-wheel drive car delivers just under 1,100 PS in qualifying mode accelerates from zero to 100 km/h in less than 2.5 seconds. The top speed is over 300 km/h (186 mph).
Although performance is the primary focus, Porsche says the body of the Mission R is largely made of natural fibre reinforced plastic (NFRP), the basic material of which is made from flax fibres obtained from farming. This material is also used on the interior of the concept car.
The interior is a spectacular place to be, and is full of driver-focused advanced technology. An ergonomically placed display between the controls on the steering wheel shows relevant data during the race, and an additional screen above the steering column shows the images from the side mirror cameras and the central rear-view mirror camera. A touch display to the right of the seat can be used to call up the driver's biometric data, for instance. Numerous other cameras in the interior can be used to provide exciting sequences for a live stream transmission.
The Mission R is a breathtaking and flamboyant vision of Porsche’s electric future, and a perfect show-stopper at IAA Mobility Munich. In its press release, Porsche not-so-subtly reminded us that both the Mission E and Mission E Cross Turismo concept studies became production models with only a few changes in appearance and technology. Let’s hope the electric Cayman and Boxster models look as good as this.
Porsche invests in Cellforce Group GmbH in the pursuit of high-performance battery technology
Porsche and joint venture partner Customcells today announced the launch of production for high-performance battery cells at the Weissach Development Centre. The announcement demonstrates Porsche’s continued technological innovation, and its commitment to e-mobility.
Porsche and joint venture partner Customcells today announced the launch of production for high-performance battery cells at the Weissach Development Centre. The announcement demonstrates Porsche’s continued technological innovation, and its commitment to e-mobility.
Oliver Blume, Chairman of the Executive Board at Porsche, Winfried Kretschmann, Minister President of Baden-Württemberg. Images: Porsche
“The battery cell is the combustion chamber of the future. As a new Porsche subsidiary, the Cellforce Group will be instrumental in driving forward the research, development, production, and sale of high-performance battery cells,” says Oliver Blume, Chairman of the Executive Board at Porsche. “This joint venture allows us to position ourselves at the forefront of global competition in developing the most powerful battery cell and make it the link between the unmistakable Porsche driving experience and sustainability. This is how we shape the future of the sports car.”
Porsche has been involved in the research of high-performance cells with silicon anodes for a while now; early research in this new battery technology has demonstrated it is possible to significantly boost the power density of cells compared to current batteries. New chemistry reduces the battery’s internal resistance, and it can offer the same energy content with a smaller footprint, and crucially, less weight. Silicon anodes effectively hold many more lithium ions, and they can move more freely than through graphite. An extra benefit is that lower-quality silicon can be used to no detriment, potentially making silicon anode Li-ion batteries cheaper than current graphite anode technology.
This graphic demonstrates how current batteries are charged and discharged. Image: Porsche
Porsche holds an 84 per cent majority stake in the new venture, which will be headquartered in the university town of Tübingen. The town is also a likely contender for a new battery cell factory, due to its proximity to the abovementioned development centre in Weissach and Porsche AG’s Stuttgart-Zuffenhausen headquarters.
The number of employees is expected to grow from the initial workforce of 13 provided jointly by both companies to up to 80 by 2025. The Federal Republic of Germany and the state of Baden-Württemberg are funding the project with around 60 million euros.
Michael Steiner, Boris Palmer, Torge Thönnessen, Winfried Kretschmann and Oliver Blume (f.l.t.r.)
“We founded Customcells with the aim of developing customer-specific battery cells for the most demanding of applications, and this is exactly what we can now realise together with Porsche. The goal for the planned production plant is to reach a minimum annual capacity of 100 MWh. This is equivalent to high-performance batteries for 1,000 vehicles,” explains Torge Thönnessen, CEO of Customcells. “We are not only contributing our expertise in cell technology and production into our partnership with Porsche, but also agility, innovative strength, and individual problem-solving skills,” adds Leopold König, who is also the new company’s CEO.
Source: Porsche
Mercedes Benz EQS exterior revealed - meet Stuttgart's first EV luxury sedan
The Mercedes Benz EQS is an important vehicle for the Stuttgart automaker. 120 years after the trademark ‘Mercedes’ was registered by Daimler-Motoren-Gesellschaft in 1901, we now have an all-electric sedan that is designed to ensure not only that the company remains the king of luxury motoring, but also the relevance and profitability in a world of strict emissions legislation, and dwindling resources.
2021 Mercedes Benz EQS debuts ‘sensual purity’ design language, 770 km range from 107.8 kwh battery
Mercedes Benz EQS 450+
single permanent magnet synchronous motor, rear wheel drive
245 kW (333 PS) / 568 Nm (418 lb ft), WLTP combined energy consumption 20.4-15.7kWh/100 km, range not stated
90 kWh nickel, manganese cobalt (NMC) modular battery, pouch cell design with 400V architecture, 200 kW DC fast charging
Mercedes Benz EQS 580 4MATIC
front and rear permanent magnet synchronous motors, all wheel drive
385 kW (523 PS) / 855 Nm (630 lb ft), WLTP combined energy consumption 21.8-17.4 kWh/100 km, range up to 770 km (478 miles)
107.8 kWh NMC modular battery, hard case cell design with 400V architecture, 200 kW DC fast charging
The Mercedes Benz EQS is an important vehicle for the Stuttgart automaker. 120 years after the trademark ‘Mercedes’ was registered by Daimler-Motoren-Gesellschaft in 1901, we now have an all-electric sedan that is designed to ensure not only that the company remains the king of luxury motoring, but also the relevance and profitability in a world of strict emissions legislation, and dwindling resources.
We’ve already covered the technical details, interior and Hyperscreen quite recently, so let’s look at what Mercedes-Benz has revealed today.
Exterior Design
It’s nice to finally be able to put a face to the EQS name. Designing such a flagship vehicle must be rather difficult, and on the whole, Gorden Wagener and his team must be congratulated. The EQS is a balance of progressive style and refined, familiar luxury. It’s a vehicle that has to outline the brand’s future direction, while still appealing to the S-Class buyer.
There are some odd angles however; soft, sloping front and rear are a result of function over form no doubt. With a drag coefficient of 0.2 cd, Mercedes Benz claims the EQS is the slipperiest sedan in the world.
Mercedes Benz states that the design philosophy behind the EQS can be defined as ‘Sensual Purity’ and that this is realised through clear, uncomplicated surfaces, curves and surface-emphasising modelling. It’s certainly not a fussy design, but will it appeal to buyers looking for a certain level of aggression and sportiness? Perhaps we’ll have to wait for an AMG version to find out.
The short front end and cab-forward look is almost the antithesis of the long-hooded luxo-barge look we’ve come to expect from this segment over the last few decades. The front end is handsome, if considerably more restrained than the EQS concept car. The black ‘grille’ on the front of the EQS is available with a Mercedes star pattern, if customers choose the AMG Line Exterior or Electric Art Exterior.
Frameless, coupé-like doors and a high, arched beltline draw the eye down the body to the rear of the EQS. Flush doorhandles aid aerodynamics, and provide a clean side profile view. The glasshouse is accentuated with chrome, and a two tone paint scheme is available.
Broad, generous surfaces, reduced join in body panels create an almost seamless transition between glass and bodywork at the rear. The rear tail light assembly is a broad, futuristic swoop of red, accentuating the width and hinting of the power within the EQS. 19-22 inch wheels are available, and the three exterior package inclusions are listed below:
Our favourite view of the EQS sedan
In our eyes, the most attractive angle of the EQS is a slightly raised and offset front three quarter view. The body is made of aluminium to keep weight down, and the front hood (bonnet) is of a clamshell design. Frunk fans will be disappointed to learn there’s no front storage compartment, but there’s ample space in the passenger compartment and rear trunk, with 610 litres of cargo capacity.
At 5.2 metres long with a 3.2 metre wheelbase — 106mm longer than the W223 S-Class — the EQS is a big car. The EQS 450 weighs in at 2480 kg (5467 lb), while the EQS 580 is 2585 kg (5,698 lb).
Mercedes Benz is expected to release an AMG performance variant of the EQS in the future, as well as a cheaper version with a smaller battery capacity. Europe, the UK and North America should see the EQS launch in the second half of 2021, while it’s expected that Mercedes-Benz Australia will bring the EQS down under in December 2021/January 2022.
You can read more of our coverage on the technical aspects of the EQS here, and view more galleries below:
2021 Mercedes Benz EQS exterior gallery
2021 Mercedes Benz EQS interior gallery





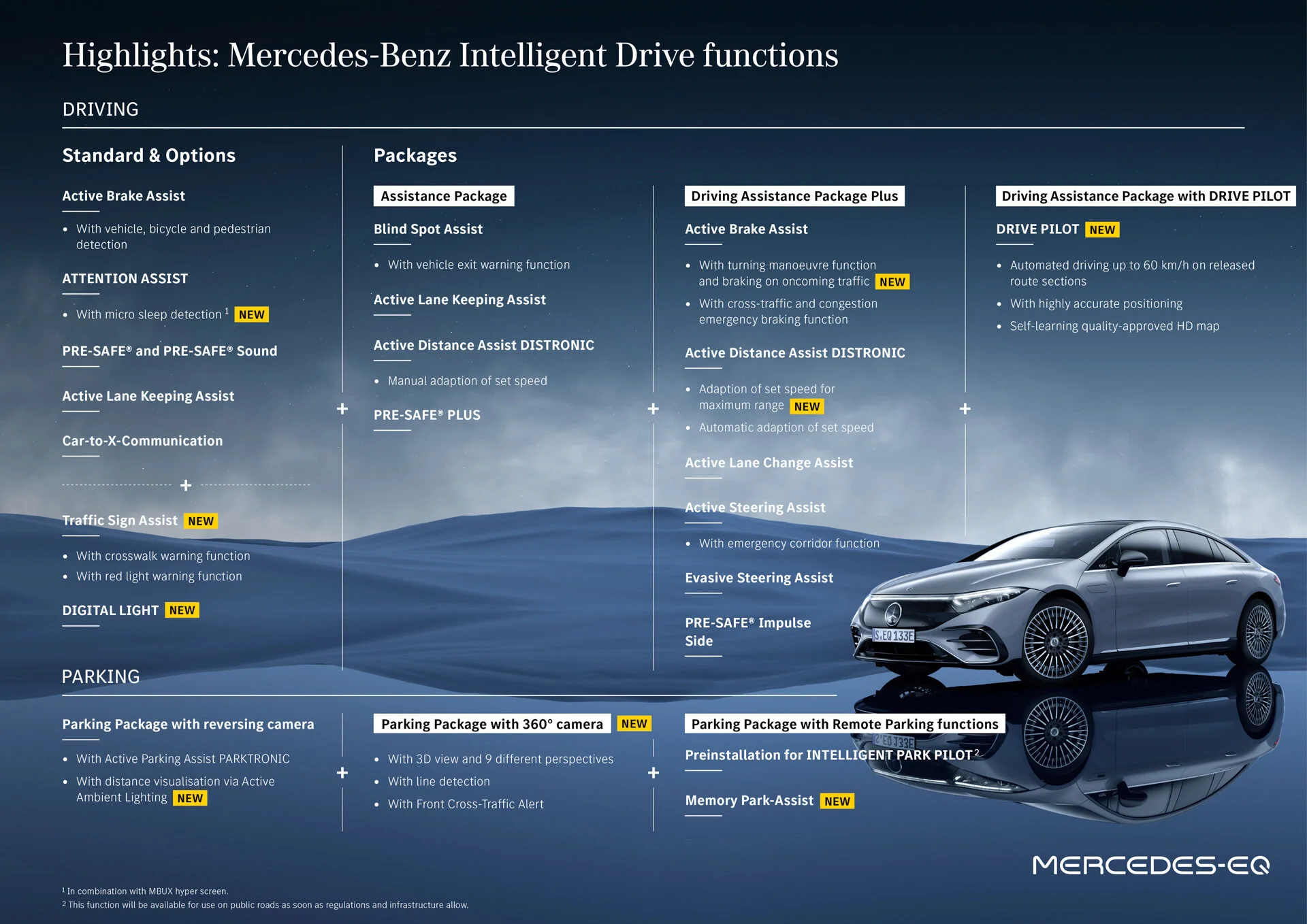
Mercedes-Benz Accelerates EV Rollout; 8 BEVs In Production by 2022
Mercedes-Benz has today announced announced its ambition to fully electrify the entire product portfolio by 2039 as part of a plan to achieve CO₂ neutrality, and this includes the rollout of eight all-electric Mercedes-EQ models from 2022 built on dedicated electric architecture. The first mass-market Battery Electric Vehicle (BEV) from Stuttgart, the Mercedes-Benz EQC has been available around the world since 2019, and is based on the pre-existing GLC SUV platform.
Images: Mercedes-Benz AU
Update: Mercedes-Benz has released an additional rendering, which you can find below. This vehicle looks to be pretty close to final production design, and will be Mercedes’ first D-segment vehicle without a traditional grille.
Mercedes-Benz has today announced announced its ambition to fully electrify the entire product portfolio by 2039 as part of a plan to achieve CO₂ neutrality, and this includes the rollout of eight all-electric Mercedes-EQ models from 2022 built on dedicated electric architecture. The first mass-market Battery Electric Vehicle (BEV) from Stuttgart, the Mercedes-Benz EQC has been available around the world since 2019, and is based on the pre-existing GLC SUV platform.
The Mercedes-Benz EQS, as shown above and below will be the first to commence production in early 2021, and is essentially the luxurious S-Class reimagined for a zero emissions future. From the camouflagued vehicle, we can see an imposing physical presence -something the S-Class has always been known for- and a low, wide nose, possibly with a faux grille a-la Jaguar i-Pace or an indentation around the badge. The bonnet (hood for you North Americans!) rises steeply into a huge windscreen, which appears to continue above the driver’s head, as is the trend nowadays.
The high bootline and almost fastback look is unusual for the S-Class segment, however the large tail lights with some presumably funky graphics and lightbar spanning the width of the rear should provide a visual family reference to the EQC, while defining the EQS’ unique character.
The side profile looks a little slab-sided under camouflague, with the C-pillar, doors and rear fender covering a large area relative to the glasshouse, however it looks like there may be some interesting surfacing hiding under that blue wrap. The Goodyears on the test car look to be hugging at least 21-inch or 22-inch wheels, as is the trend these days. That’s aesthetics over efficiency for you.
The EQS will be produced in Sindelfingen from early 2021, while the less expensive EQA and EQB models will be produced at the Rastatt and Kecskemét (Hungary) plants respectively. We can expect the world premiere of the EQA on January 20, 2021 according to Mercedes-Benz.
Fast forward to the second half of 2021, and Mercedes-Benz states that the EQE ‘business sedan’ will begin production at the Bremen plant, as well as in Beijing for the Chinese domestic market only. Continuing the the Germans’ fondness for manufacturing SUVs in the United States, the EQE and EQS SUV variants will be manufactured at the brand’s Tuscaloosa Alabama plant.
According to Mercedes, a total of eight Mercedes-EQ electric vehicles will be produced at seven locations on three continents by 2022.
Daimler’s Battery Plans
Battery development, manufacture and supply will obviously be a critical part of this increase in BEVs, and Mercedes-Benz plans to increase investment in the energy side of manufacturing, alongside battery specialists.
Mercedes-Benz and BAIC have jointly set up a battery production plant at the existing location in the Yizhuang Industrial Park in Beijing (China) for vehicles sold in the domestic market.
In addition to two battery plants in Kamenz (Germany) already producing battery systems for Mercedes-Benz, the company plans a future battery plant at the Sindelfingen site, increasing capacity already available from the nearby Untertürkheim plants in preparation for locally built electric models.
Furthermore, Mercedes-Benz is upgrading the Jawor (Poland) battery plant, currently manufacturing battery packs for plug-in hybrid variants of the C,E and S-Classes, to include battery systems for upcoming EQ models, as well as planning a battery plant in the vicinity of the Tuscaloosa Alabama factory.
You can read the full press release below, alongside an interview with Jörg Burzer, Member of the Board of Management of Mercedes-Benz AG, Production and Supply Chain.
Mercedes-Benz Sindelfingen plant (Germany): Launch of electric luxury sedan EQS in Factory 56 in first half of 2021
Mercedes-Benz Rastatt plant (Germany): Production of first all-electric compact SUV EQA started - also at Beijing plant (China) in 2021
Mercedes-Benz plant in Kecskemét (Hungary): Decision to locate second all-electric compact SUV EQB. Production launch in 2021 - also at Beijing plant (China)
Mercedes-Benz Bremen plant: Production launch of electric EQE business sedan in 2021 - at Beijing plant soon thereafter (China)
Mercedes-Benz Tuscaloosa plant (USA): SUV variants EQS und EQE begin in 2022
Mercedes-Benz battery production network: Production start of battery systems for EQS and EQE in Untertürkheim/Hedelfingen (Germany) imminent. Production of compact SUV battery systems in Kamenz (Germany), Jawor (Poland) and Beijing (China) plants. Tuscaloosa battery plant will produce batteries for SUV variants of EQS and EQE beginning 2022
15 December 2020, Stuttgart. Mercedes-Benz is targeting leadership in electric drives and vehicle software. The consistent electrification of the entire product portfolio is a key element of the strategic focus "Ambition 2039" and a prerequisite on the way to CO₂ neutrality. In 2022 the portfolio includes eight all-electric Mercedes-EQ models. The global Mercedes-Benz production network is ready for the company’s electric product offensive and is integrating its Mercedes-EQ models into series production in its existing plants.
Markus Schäfer, Member of the Board of Management of Daimler AG and Mercedes-Benz AG; responsible for Daimler Group Research and COO Mercedes-Benz Cars: “With its ‘Electric First’ strategy, Mercedes-Benz is consistently on the path to CO₂ neutrality and is investing heavily in transformation. Our vehicle portfolio becomes electric and thus also our global production network with vehicle and battery factories. We intend to lead in the field of e-mobility and focus in particular on battery technology. We are taking a comprehensive approach, ranging from research and development to production, and also including strategic cooperation.”
The EQS, the first electric luxury sedan from Mercedes-Benz, will start in the first half of 2021 in Factory 56 at the Sindelfingen site (Germany). With the production launch of the electric compact SUV EQA at the Rastatt plant (Germany) and the current decision to locate EQB production in the Hungarian plant in Kecskemét, the company is taking further important steps toward making its product portfolio CO₂ neutral. The course has also been set toward “Electric First” in the global powertrain production network as well. High-efficiency battery systems will also be manufactured and assembled within the production network.
Jörg Burzer, Member of the Board of Management of Mercedes-Benz AG, Production and Supply Chain: “The Mercedes-Benz production network is global, digital and flexible, and ready for the upcoming electric offensive – thanks, of course, to our highly qualified and motivated employees worldwide. We are now beginning a real Mercedes-EQ fireworks display. Six electric product launches by 2022 underscore the strength and competence of our Mercedes-Benz production sites worldwide. The production network will have a total of six Mercedes-EQ car locations. Local production of highly efficient battery systems plays a central role in the Mercedes-Benz strategy - coupled with a comprehensive sustainability concept that spans the entire life cycle of the battery all the way to recycling.”
Mercedes-Benz vehicle plants consistently implement electric offensive
In May 2019 production of the EQC (combined power consumption: 21.5 kWh/100 km; combined CO₂ emissions: 0 g/km) at the Mercedes-Benz plant in Bremen (Germany) was integrated into ongoing series production. Just a few months later the German-Chinese production joint venture, Beijing Benz Automotive Co. Ltd. (BBAC), launched EQC production for the local market in China. In 2020 production of the EQV premium electric MPV (combined power consumption: 26.4 kWh/100 km; combined CO₂ emissions: 0 g/km)1 started in Vitoria, northern Spain.
Compact car class customers can look forward to two fully electric compact SUVs in the EQA and EQB in 2021. EQA will celebrate its world premiere on January, 20 2021 as the first fully electric derivative of this compact car. The EQA production launch at the Mercedes-Benz Rastatt plant went smoothly. As with the EQC from Bremen and Beijing and the EQV from Vitoria, which are already on the market, the fully electric models at the Rastatt plant run on the same production line as compact vehicles with conventional and hybrid drives. That means all five vehicles produced in Rastatt are electrified: In addition to the fully electric EQA, the AClass, A-Class sedan, B-Class and the compact SUV GLA are also produced at the Mercedes-Benz plant in Rastatt - with classic combustion engines as well as plug-in hybrid drive. With that the Mercedes-Benz Rastatt plant is making an important contribution on the road to a CO₂ neutral vehicle fleet and to the Mercedes-Benz AG electric offensive. EQA production will also follow next year (2021) at BBAC in Beijing for the Chinese market.
EQB production will launch in 2021 at two locations in the global Mercedes-Benz Cars production network: in the Hungarian Mercedes-Benz plant in Kecskemét for the world market and in the German-Chinese joint venture BBAC in Beijing for the local market. Plant preparation, including employee training and renovation work, is already underway. The compact SUV EQB will be the first purely electrically powered production vehicle from Hungary and will complement the plug-in hybrid portfolio consisting of the CLA and CLA Shooting Brake. The A-Class will also be produced in Kecskemét with a plug-in hybrid drive, in addition to production in the German Mercedes-Benz plant in Rastatt.
Furthermore, in the first half of 2021 production of the EQS electric luxury sedan will begin in Factory 56 at the Mercedes-Benz plant in Sindelfingen (Germany). EQS is the independent, fully electric member in the new S-Class program and is the first to use the new electric architecture for luxury and upper-class electric vehicles at Mercedes-Benz. In Factory 56 the S-Class and, in the future, the Mercedes-Maybach S-Class, and the EQS will be produced in a fully flexible manner on the same line. Factory 56 embodies the future of production at Mercedes-Benz and sets new standards for automobile construction. In Factory 56 efficiency gains of around 25 percent are achieved compared to the previous S-Class assembly. This is made possible by optimizing the entire value chain and full digitalization with MO360, the digital Mercedes-Benz production ecosystem. For further information on this: https://media.daimler.com/marsMediaSite/ko/en/47014243
Furthermore, the Mercedes-Benz plant in Bremen will begin production of the EQE business sedan in the second half of 2021, followed shortly thereafter at the Beijing plant. The EQE thus complements the allelectric portfolio of the two plants. The Beijing plant will then produce a total of four Mercedes-EQ models for the local market.
The Mercedes-Benz plant in Tuscaloosa (USA) is also preparing for production of the EQE SUV and EQS SUV in 2022, which will be produced in the future on the same line with SUVs with conventional and plug-in hybrid drives.
In 2022 a total of eight Mercedes-EQ electric vehicles will be produced at seven locations on three continents. This is possible because the company made early investments worldwide in flexibility and technical equipment with future-oriented Industry 4.0 solutions. In the Mercedes-Benz AG plants, vehicles with different drive types can be produced in parallel thanks to highly flexible structures. With a view to the strategic goal of generating more than half of sales with so-called xEVs, i.e. plug-in hybrids and electric vehicles, from 2030 on and gradually increasing the purely electric share, the high degree of flexibility is a decisive advantage. It enables production to be adjusted at short notice depending on market demand.
smart rounds off the electric Mercedes-Benz Cars portfolio with three additional models. The smart EQ fortwo (combined power consumption: 16.5 kWh/100 km, combined CO₂ emissions: 0 g/km)1 and smart EQ fortwo Cabrio (combined power consumption: 16.8 kWh/100 km, CO₂ emissions combined: 0 g/km)1 are produced in Hambach, France, and the smart EQ forfour (combined power consumption: 17.3 kWh/100 km; combined CO₂ emissions: 0 g/km)1 in Novo Mesto, Slovenia. The next generation of smart electric vehicles will be produced by the joint venture smart Automobile Co., Ltd. in China. This is a joint venture of MercedesBenz AG and the Zhejiang Geely Group (Geely Holding).
Plug-in hybrid drive is important as a key technology and intermediate step toward a purely electric product portfolio. More than 20 plug-in hybrid model variants are already an integral part of the Mercedes-Benz product portfolio. The portfolio will be expanded to include more than 25 model variants by 2025. Their production therefore also plays an important role in the global production network. Plug-in hybrid vehicles are already rolling off Mercedes-Benz Cars assembly lines in almost all car plants.
Global battery production network: a key success factor in the Mercedes-Benz electric offensive
The batteries for the Mercedes-EQ electric vehicles are supplied by a global battery production network with plants on three continents. Local battery production is a key success factor for the Mercedes-Benz electric offensive.
Two plants in Kamenz (Germany), have been producing battery systems for hybrids, plug-in hybrids and electric vehicles since 2012. The second battery factory at the site began operations in 2018 and has been producing the EQC's battery systems since 2019. It was designed from the start as a CO₂ neutral plant and combines, among other things, solar energy, geothermal energy and a combined heat and power plant. The battery systems for the EQA have also recently rolled off the production line at the site. Since the start of production at Accumotive, more than a million batteries based on lithium-ion technology for electric, plug-in hybrid vehicles and 48-volt systems have been produced at the Kamenz site.
Mercedes-Benz and BAIC have jointly set up local battery production at the existing location in the Yizhuang Industrial Park in Beijing (China). This supplies the nearby vehicle plant, which has also added all-electric Mercedes-EQ models to its portfolio with the EQC. Production of battery systems for the EQC started there in 2019. With the start of production of the EQA, EQB and EQE, the plant will manufacture battery systems for a total of four Mercedes-Benz EQ models beginning in 2021.
This year the battery plant in Jawor (Poland) started producing plug-in hybrid batteries for the C, E and SClasses. In the coming year the location will expand its portfolio to include battery systems for the compact Mercedes-EQ models, the EQA and the EQB. Much like the battery plant in Kamenz, the plant was designed from the outset for CO₂ neutral production.
In the future at the Untertürkheim (Germany) site two plants will produce battery systems. Final preparations for the production of the battery systems for the EQS, which will roll off the production line in nearby Sindelfingen in the first half of 2021, are currently underway at the Hedelfingen plant. The battery system for the EQE will also be produced in Hedelfingen. Another battery plant is currently being built in the Brühl facility, which will manufacture battery systems for Mercedes-Benz plug-in hybrids starting 2022. The work on the building has already been completed. The battery plant in Brühl will be fitted with the corresponding equipment in the coming months.
Production of the EQS and EQE SUV models will start in 2022 at the Mercedes-Benz plant in Tuscaloosa (USA). A battery plant is currently being built in the immediate vicinity and will supply highly efficient battery systems for both models. Work on the building has already been completed. The ultra-modern systems will be installed in the coming months.
In addition, the Mercedes-Benz production strategy currently provides for another battery plant at the Sindelfingen site.
Together with local partner Thonburi Automotive Assembly Plant (TAAP), Mercedes-Benz Cars set up a battery production facility in Bangkok (Thailand) and began operations in 2019. Battery systems for the current C, E and S-Class plug-in hybrids are manufactured at the site. Preparations are also being made there to manufacture drive batteries for all-electric Mercedes-EQ brand vehicles.
Electric First und Ambition2039: CO₂ neutral mobility und production
Under “Electric First,” Mercedes-Benz is pursuing the consistent electrification of all model variants and vehicle types as a clear objective. The decisive factor here over the next few years is the gradual increase in the purely electric share of the vehicle portfolio. So-called xEVs, plug-in hybrids and fully electric vehicles, should account for more than half of sales by 2030 - and the trend is rising. Electrically powered vehicles from Mercedes-Benz are enjoying increasing popularity. The company delivered a total of 45,000 electric vehicles and plug-in hybrids (xEVs) worldwide in the third quarter of 2020.
With “Ambition2039,” Mercedes-Benz introduced its path to CO₂ neutrality over a year ago. Vehicle production plays a crucial role in this regard. As early as 2022 the company’s Mercedes-Benz car and van plants will produce CO₂ neutrally around the world. This includes more than 30 car and van plants, as well as battery plants.
Brief interview
“We’re producing the Mercedes-EQ models the Mercedes way: Completely digital and flexible, highly efficient and maximally sustainable.”
Questions for Jörg Burzer, Member of the Board of Management of Mercedes-Benz AG, Production and
Supply Chain
Mr. Burzer, are you equipped for the production of electric vehicles in your production network?
The Mercedes-EQ production network is ready for our electric offensive. We started this transformation several years ago and set up our plants with maximum flexibility. The Mercedes-EQ electric models are gradually being integrated into our existing vehicle plants worldwide. They come off the same lines as vehicles with combustion engines or plug-in hybrid drives. The same applies to all of our Mercedes-Benz car plants - a total of six on three continents. This concept is particularly advantageous because demand for electric and electrified vehicles is developing very differently by region and we can adjust our production planning accordingly on short notice. In this way we can manufacture exactly what our customers want.
What specifically does your production planning for the upcoming model offensive look like?
One thing is certain: the proportion of all-electric vehicles in our portfolio will increase sharply in the coming years. By 2030 more than fifty percent of our vehicles will roll off the assembly line as so-called xEVs. Plug-in hybrids and hybrids will therefore continue to play an important role in our production planning over the next few years. However, our target is clearly designed for 100 percent Mercedes-EQ and we are directing our capacity precisely in this direction. We are preparing our production, as well as our employees, step by step for this change. Our sustainability concept is also a central focus: from 2022 on we will produce CO₂ neutral in our Mercedes-Benz plants worldwide.
What, specifically, were the challenges?
Every vehicle launch during ongoing production comes with challenges. That, of course, also applies to electric vehicles. However, thanks to the know-how in our plants and cross-location system planning, we could quickly develop and implement flexible solutions. The consistent digitalization of our processes through our digital production ecosystem MO360 also made a significant contribution. An important factor here, of course, is attaining targeted qualifications for our colleagues in our plants, which we consistently promote.
How will powertrain production continue in the future?
For the global Mercedes-Benz powertrain production network, the shift toward e-mobility poses a special challenge. However, we are determined to continue aligning our drive division to this change and make it sustainable for the future. We have already built up extensive know-how in our powertrain plants in recent years. It starts with the expansion of our battery production network and includes, among other things, manufacturing and assembling parts of the electric drivetrain ourselves. Still, it’s also clear that the drivetrains of the future will differ significantly from those of today.
You will manufacture the batteries for the Mercedes-EQ models in house?
The local production of batteries is an essential success factor in our electric offensive. With a view to steadily increasing demand and, in accordance with our production planning, we are setting up our global battery production network to be flexible worldwide. Today we already produce batteries in Kamenz, Bangkok and Beijing. The ramp-up of our battery plants in Hedelfingen and Jawor is imminent and our colleagues in Brühl and Tuscaloosa are already preparing to start production in 2022. Our production network is very well positioned for the Mercedes-EQ model offensive.
Which new electric model are you personally most looking forward to?
Basically, I look forward to every new Mercedes-Benz. A very special milestone is certainly the upcoming EQS production launch. It will roll off the assembly line, together with the S-Class, in our new Factory 56 at the Mercedes-Benz plant in Sindelfingen. Here we’re setting the course for our entire production network: With the most modern production technologies Factory 56 is a blueprint for our global network. At the same time, it bolsters our claim - the Mercedes way - to the production of the Mercedes-EQ models: completely digital and flexible, highly efficient and maximally sustainable.