EV Brief Podcast #44: Danny Thai, Zecar & Shaun Garrard, Industry Expert
In this episode, Jonathan sits down with Danny Thai of Zecar and Shaun Garrard, EV industry expert to discuss the Chinese EV market, battery technology, charging infrastructure rollout in Australia and more.
In this EV Brief Hangout, three EV-focused friends sit down at a table and discuss zero emissions transport on World EV Day.
Danny Thai is the founder of zecar.com, a one-stop-shop for electric car news, comparisons, data and clean energy.
https://www.linkedin.com/in/dannythai123/
Shaun Garrard has extensive experience across the automotive and electric vehicle sectors in the Asia Pacific region, including with Tesla Australia and WM Motor in Shanghai.
Timecodes:
00:00 - Introduction
01:25 - What's happening this week in EVs
02:50 - Shaun's background
06:20 - Do western countries see China as a serious automotive player?
08:35 - Wan Gan - the man behind China's EV dominance
13:30 - Talking NIO
18:07 - Battery swapping; will it work in Australia?
22:00 - The cost of charging infrastructure
26:40 - Tackling residential charging issues
29:20 - EV Uptake in Australia
30:15 - Are there benefits from not being first; will it pay off to watch other countries makes the switch to EVs from fossil fuel
30:50 - Carrot + stick - how to drive people into EVs, and what should Australia's national strategy be?
37:20 - Which future products are we looking forward to?
Incredible efficiency and range - the Mercedes-Benz VISION EQXX concept teases the future
Travelling over 1,000km on a single charge, the VISION EQXX debuts lightweight composite bionic chassis construction, energy efficient wheels and tyres, a lightweight battery with improved energy density and an outstanding drag coefficient figure of Cd0.17
The Mercedes-Benz VISION EQXX sets off on its record-breaking trip. Images: Mercedes-Benz
The Mercedes-Benz VISION EQXX is not a production car, nor a showy concept vehicle but rather an engineering test bed for future Mercedes-Benz Group technologies. This week, the EQXX travelled from Sindelfingen across the Swiss Alps and Northern Italy, to Cassis on the Côte d'Azur in France - a journey of more than 1,000 kilometres (620 miles). The long-distance drive was completed with the charging socket sealed and accompanied by an independent expert from certification body TÜV Süd.
Averaging a record 8.7 kWh/100km energy consumption figure, the EQXX’s battery still held a 15% state of charge (around 140km) upon arrival. So how was this achieved?
The answer is of course, not due to one single factor, rather an incredible soup of advanced design and engineering. The EQXX’s slightly odd, rounded form provides an aerodynamic drag coefficient of Cd 0.17, lower than the slippery EQS which has a score of 0.20. Mercedes-Benz says that air “flows elegantly like a water droplet towards the rear".
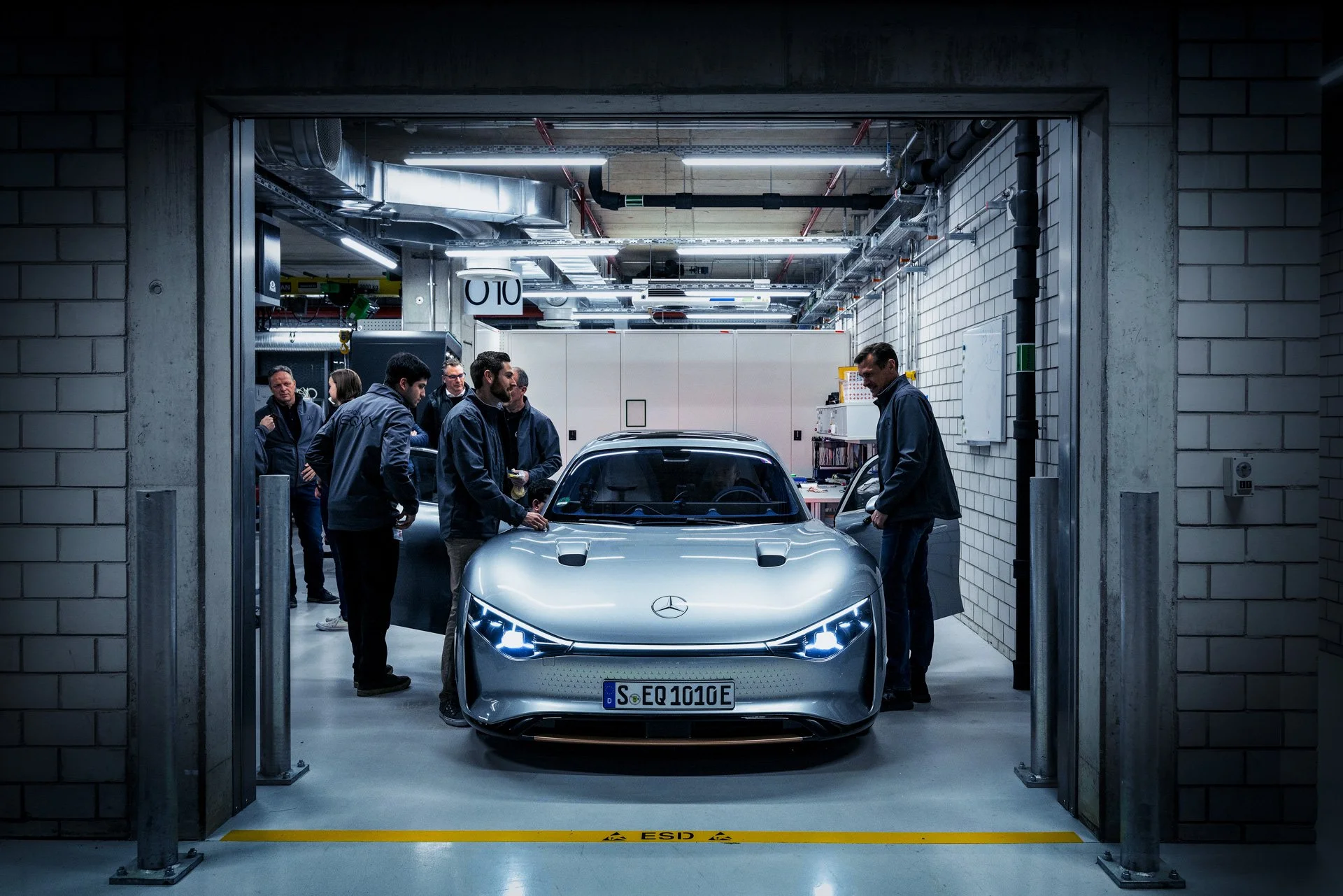

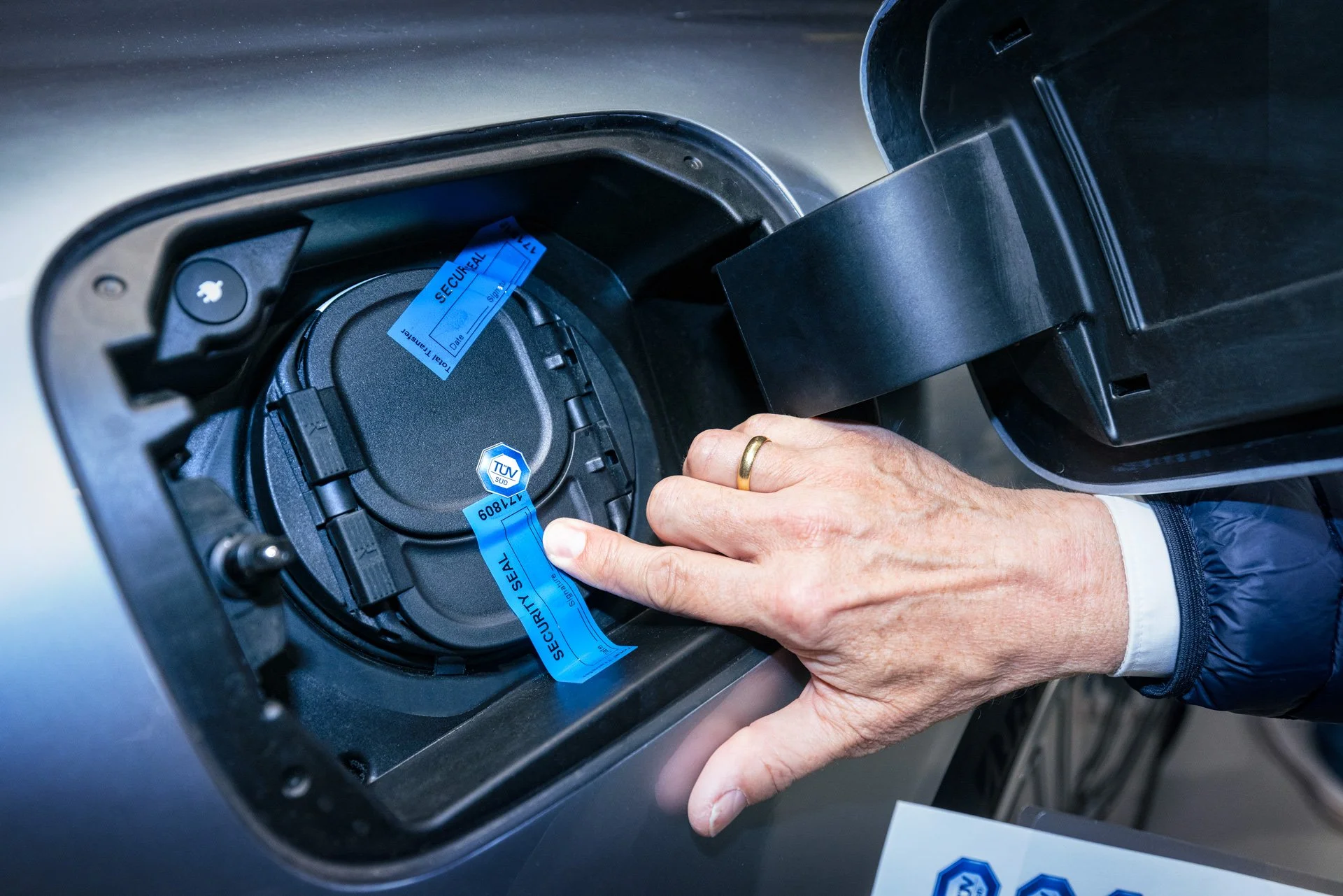

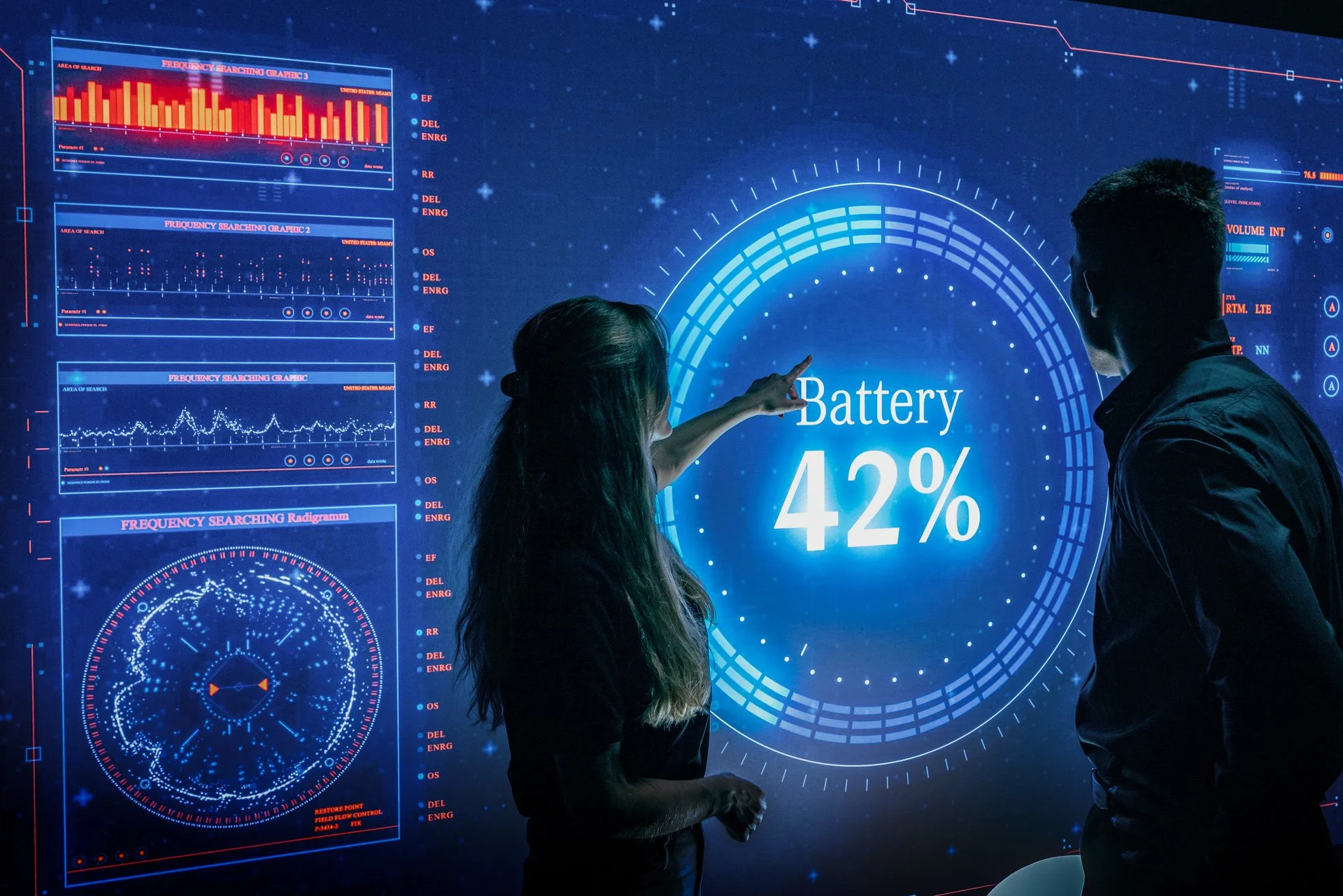





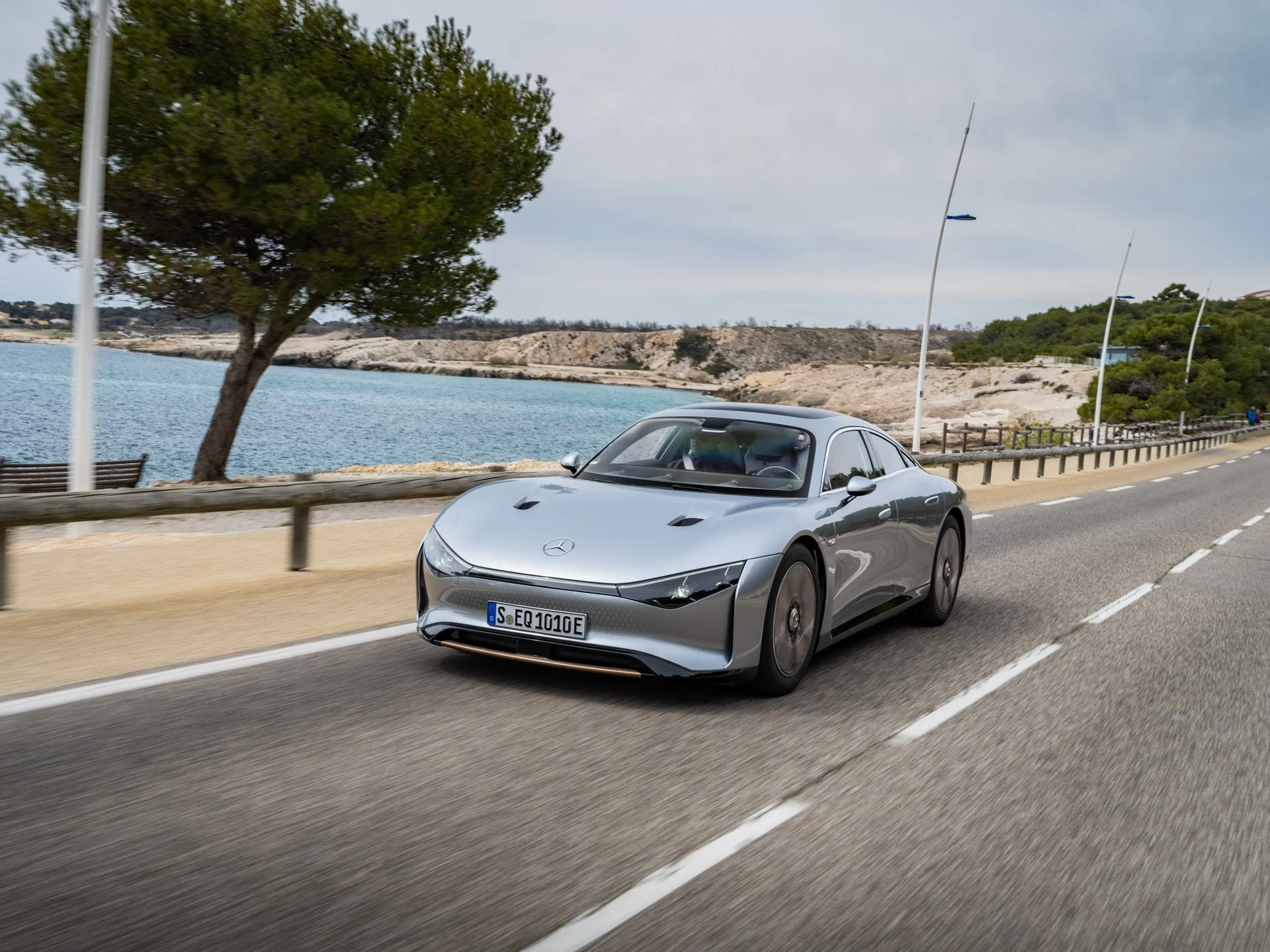
According to Ola Källenius, Chairman of the Board of Management of Mercedes-Benz Group AG, “The VISION EQXX is the most efficient Mercedes ever built. The technology programme behind it marks a milestone in the development of electric vehicles. It underpins our strategic aim to ‘Lead in Electric’,”
Low rolling resistance tyres were specially developed for the EQXX in conjunction with Bridgestone. At 185/65 R 20 97 T, the wide diameter and narrow width provide a 20 percent weight reduction, improved aerodynamic geometry, and in conjunction with lightweight magnesium wheels, greater driving range.
Bionic engineering is Mercedes’ fancy term for making stuff lighter. Tesla has pushed the automotive industry forward with its lightweight, single-piece castings, but Mercedes-Benz has gone further with its bionic-looking structural components. The skeletal aluminium chassis components have holes where structural rigidity is not necessary, providing a 20 percent weight reduction.
A 100 kWh battery — the same capacity as the Mercedes-Benz EQS — sits within the floor of the EQXX, however it weighs just 495kg, some 30 percent less than the EQS. With 50 percent less volume than its sedan sibling, the EQXX battery measures just 200 x 126 x 11 cm. The total weight of the vehicle is 1,755 kilograms.
While we won’t see the EQXX’s technology in production vehicles anytime soon, Mercedes-Benz has always been a leader in automotive engineering, safety and drivetrain development. The S-Class limousine debuted many features now taken for granted on the cheapest of econoboxes today, from the Anti-lock Braking System (ABS), airbags, and adaptive cruise control. We can be certain that innovations debuted within the EQXX will begin to filter through to Mercedes’ production battery electric vehicles this decade.
Source: Mercedes-Benz
German auto giants Mercedes-Benz and Volkswagen accelerate battery production plans
Daimler secures 33 percent stake in Automotive Cells Company alongside Stellantis and TotalEnergies, and JAC Volkswagen announces construction of additional battery factory in Hefei, China.
Following news this week that Ford has partnered with Redwood Materials to secure future battery component supply chains, we have an announcement from Daimler that Mercedes-Benz has secured a 33 percent stake in Automotive Cells Company (ACC), a battery cell manufacturer with a presence in France. The stake is estimated to be worth around $1.2 billion USD ($1.65 billion AUD).
Stellantis and French petroleum company TotalEnergies own 33 percent each. Automotive News Europe reports Mercedes-Benz CEO Ola Kaellenius has said “the purpose of the partnership is to develop cells and battery modules and “help ensure that Europe remains at the heart of the auto industry — even in an electric era.”
Mercedes-Benz will provide technology and production expertise to the ACC partnership, and aims to manufacture at least 120 Gigawatt hours of cell capacity by the end of the decade with its partners. The company is moving towards a modular, standardised battery “kit” that allows battery cells and modules from different manufacturers to easily fit with its range of components and interfaces.
High energy density, performance and charging power are key benchmarks for the project according to Daimler. ACC will primarily use renewable energy for its production facilities, and the batteries themselves will be over 95 percent recyclable.
ACC’s first new factory will be located in Northern France, and plans to be operational by 2023.
A rendering of JAC Volkswagen’s Hefei battery production facility. Image: Volkswagen
Volkswagen powers ahead in China
Meanwhile, Chinese joint venture Jianghuai Automobile Group/Volkswagen (JAC Volkswagen) will also have a new battery factory operational by 2023, located in Hefei city. Automotive News Europe states that the factory's initial capacity will be 150,000 to 180,000 battery systems a year.
This is the fourth battery factory in the works for the Wolfsburg automaker, with plants in Brunswick and Salzgitter Germany coming online in the next couple of years. A battery factory in Chattanooga, TN and at Volkswagen technology partner Northvolt’s Skellefteå plant should also be operational by 2023. Volkswagen plans to produce unified, modular cells like Mercedes-Benz for its scalable MEB platform architecture, and has flagged an annual capacity of up to 180,000 battery systems from its Hefei plant.
“With a significant increase of battery-electric vehicles in the future, we need to focus on keeping key components like battery systems in our own value chain, allowing us to leverage Group-wide synergies and innovations” says Stephan Wöllenstein, CEO of Volkswagen Group China. He goes on to say that “Volkswagen Anhui and VW Anhui Components Company, alongside our two strong Joint Ventures, are crucial to our electrification strategy and to achieving our goal of the Volkswagen Group China fleet reaching over 40% NEVs by 2030”.
Sources: Daimler, Automotive News Europe
Hyundai IONIQ 7 electric SUV due 2024, powered by SK Innovation Co batteries
A teaser image of the future of the IONIQ range. We’ve lightened the image to provide a better look. Image: Hyundai
We seem to be covering Hyundai’s IONIQ range non-stop these days (no bad thing). The IONIQ 5 is on-sale in Europe, Asia and New Zealand, and about to open for customer orders in Australia. Hyundai’s IONIQ 6 sedan has been delayed this week; pushed back to mid-2022 due to changes to the battery system and a redesign according to reports.
To round out the week, we have news from The Korean Economic Daily that SK Innovation Co. has been chosen to supply batteries to Hyundai for the 2024 IONIQ 7 full-size SUV. Based on the modular E-GMP platform, the IONIQ 7 is set to come in two and four wheel drive configurations, and from the official Hyundai images and the rendering below, melds interesting elements of traditional SUV design with a hint of futurism.
SK Innovation Co currently supplies battery systems for the IONIQ 5 and Kia EV6 models. Strong sales of the former have boosted SK Innovation Co’s profitability and battery supply, with 12,484 units sold in the Korean domestic market, and 18,966 sold abroad.
An IONIQ 7 rendering from TopElectricSUV.com
The IONIQ 6 will use batteries from Korean competitor LG Energy Solution Ltd; the battery maker has signed an memorandum of understanding with Hyundai and the Indonesian Government to partner in a new $1.1 billion USD battery plant in Indonesia. LG Energy Solution hopes to ramp production to an annual capacity of 10 GWh of cells by 2024, providing enough energy for 150,000 electric vehicle battery systems per year.
Hyundai is cleverly spreading its risk — both in terms of supply chains and development — by partnering with all the top battery makers in Korea. The IONIQ range is expected to miss out on solid-state battery technology according to industry insiders; an additional partnership exists between Samsung SDI Co and Hyundai to develop an all-solid-state battery, but that technology isn’t expected to reach commercial viability until 2027 at the earliest.
Hyundai’s IONIQ 7 is based on the modular E-GMP platform.
Ford partners with Redwood Materials to recycle EVs, and provide battery materials
The deal will see the automaker work with battery recycling firm Redwood to create an end of life solution for electric vehicles, reducing environmental footprint and future cost of manufacturing, while ensuring Ford has adequate supply to meet projected battery demand.
Ford’s EV architecture will soon use recycled battery components in a deal with Redwood materials. Image: Ford
Ford is partnering up with Redwood Materials with a plan to create a closed loop supply chain system for its future range of electric vehicles. Redwood Materials is the brainchild of former Tesla CTO JB Straubel, and the company wants to address the problems of growing e-waste by developing an end-of-life supply chain to provide materials to battery manufacturers and automakers.
According to a Redwood Materials media statement, “we [Redwood Materials] need to start planning now for the end-of-life of batteries as we ramp up to build millions of EVs that can’t be disposed of safely without a robust recycling solution. The exciting side of this problem is that the critical materials inside of a battery are essentially infinitely recyclable. Unlike gasoline, the materials are not consumed or lost in their lifetime of usage in the vehicle.”
Ford has already seen success with its Mustang Mach-E, and as the electrified F-150 Lightning enters pre-production, the automaker is sure to see battery cell and component demand soar over the short-to-medium term.
Battery modules used in Ford’s Mustang Mach-E, manufactured by SK Innovation. Image: SK Innovation
Redwood Materials currently partners with battery manufacturers such as Panasonic/Tesla in Nevada, and Envision in Tennessee. The company received a healthy $700 million capital injection in late July, through a successful fundraising round from the likes of Baillie Gifford, Goldman Sachs Asset Management, Amazon and more.
Redwood plans to soon supply anode and cathode materials back to the American supply chain, and the company states that the deal with ford will span a vehicle battery’s entire lifecycle. To further advance these business opportunities between the companies, Ford has invested $50 million in Redwood to help them expand their manufacturing footprint.
It’s positive to see Ford thinking ahead like this; while many automakers like Volkswagen and Stellantis are simply scrambling to build up battery capacity to meet growing demand, Ford’s long-term strategic partnership should provide the company with an opportunity to not only secure enough materials to meet production demand, but reduce costs of production, and the associated environmental footprint.
Mercedes-Benz announces electrification plan, EV and battery rollout, end of internal combustion vehicles
Mercedes-Benz has announced an end to its internal combustion-engined product offerings, moving towards a range of electric-only vehicles by 2030. Mercedes-Benz will cease the development and release of internal combustion vehicle architectures from 2025, launching three electric-only platforms in the same year.
Mercedes-Benz has announced an end to its internal combustion-engined product offerings, moving towards a range of electric-only vehicles by 2030. The caveat provided by the company is that zero-emissions vehicles will prevail “where market conditions allow”, presumably giving the automaker a guilt-free emissions pass in markets where charging infrastructure and EV uptake is yet to develop.
Mercedes-Benz will cease the development and release of internal combustion vehicle architectures from 2025, and will launch three electric-only platforms in the same year. According to the company, customers will be able to choose an all-electric alternative for every model in the Mercedes-Benz range, and that “Mercedes-Benz intends to manage this accelerated transformation while sticking to its profitability targets.”
Ola Källenius, CEO of Daimler AG and Mercedes-Benz AG said in a media statement that "The EV shift is picking up speed - especially in the luxury segment, where Mercedes-Benz belongs. The tipping point is getting closer and we will be ready as markets switch to electric-only by the end of this decade," "This step marks a profound reallocation of capital. By managing this faster transformation while safeguarding our profitability targets, we will ensure the enduring success of Mercedes-Benz. Thanks to our highly qualified and motivated workforce, I am convinced that we will be successful in this exciting new era."
Ola Källenius, CEO of Daimler AG and Mercedes-Benz AG with the Mercedes-Benz EQ range.
Mercedes-Benz’s Future Product Line-Up
Let’s look at the above image and get a sense of where the brand is heading this decade. We’re already familiar with the upcoming EQS luxo-barge next to Ola Källenius, and pictured to its right is the soon-to-be-revealed EQE sedan. Both vehicles are based on Mercedes-Benz’s Electric Vehicle Architecture (EVA) modular platform. Behind them, from left to right, we have the GLB crossover, and the currently on sale EQC and EQA crossovers. In the third row, a mysterious crossover —likely the EQS SUV— sits just ahead of the EQV.
Mercedes-Benz revealed its subbrands including AMG, Maybach and G-Class —made infamous in the 2010s as a symbol of gas-guzzling excess— will go electric. The EQS SUV will be the first vehicle in the lineup to receive the Maybach work-over, as teased in this image below.
The Mercedes-Benz EQS SUV Maybach. Image: Mercedes-Benz
All subbrands to go electric. Images: Mercedes-Benz.
Brand new electric platforms from 2025
Three electric-only architectures will be launched in 2025:
MB.EA will cover all medium to large size passenger cars, establishing a scalable modular system as the electric backbone for the future EV portfolio.
AMG.EA will be a dedicated performance electric vehicle platform addressing technology and performance oriented Mercedes-AMG customers.
VAN.EA ushers in a new era for purpose made electric vans and Light Commercial Vehicles, which will contribute to emission free transportation and cities in the future.
Manufacturing and battery cell demands
The upcoming mercedes-Benz EQB.
Mercedes-Benz plans to install battery cell capacity of more than 200 Gigawatt hours with partners, and sets its sights on eight Gigafactories to support this product rollout. The company will develop new partnerships for R&D and production of battery cells in Europe.
Following Tesla’s lead and in an attempt to reduce the bureaucracy and cost of development for legacy automakers, Mercedes-Benz is reorganizing its powertrain activities to put planning, development, purchasing and production under one roof. The company claims this will deepen the level of vertical integration in manufacturing and development and electric drive technology.
Mercedes-Benz’s next-generation batteries will debut in 2025 and will be highly standardized, and suitable for use across more than 90 percent of all Mercedes-Benz cars and vans according to the automaker. The company intends to focus battery cell and module manufacturing in Europe, keeping the supply chain close to home. It will work with technology partners across Europe such as SilaNano to further increase energy density in batteries through silicon- carbon composite anodes.
Mercedes-Benz is also developing solid-state technology, with an aim to create batteries with even higher energy density and safety. The company is already trialling Citaro buses with solid-state batteries.
EV Brief’s Take
This is all great news in our view. After a general reluctance to commit to electrification from Germany’s big automakers, Mercedes-Benz is officially going “all in”. Massive investment in capital works, battery gigafactories, and cell R&D, as well as ensuring reduced emissions and CO2 neutrality from the production process will allow the brand to get ahead of strict EU emissions regulations, while ensuring future commercial viability.
Streamlining its business through centralised production, common battery modules and shared platform architecture will not only lead to positive business outcomes and an increased return on investment, but it should also bring with it faster product rollout timeframes, and a greater diversity of product offerings.
Source: Mercedes-Benz
The Mercedes-Benz EQS.
Porsche invests in Cellforce Group GmbH in the pursuit of high-performance battery technology
Porsche and joint venture partner Customcells today announced the launch of production for high-performance battery cells at the Weissach Development Centre. The announcement demonstrates Porsche’s continued technological innovation, and its commitment to e-mobility.
Porsche and joint venture partner Customcells today announced the launch of production for high-performance battery cells at the Weissach Development Centre. The announcement demonstrates Porsche’s continued technological innovation, and its commitment to e-mobility.
Oliver Blume, Chairman of the Executive Board at Porsche, Winfried Kretschmann, Minister President of Baden-Württemberg. Images: Porsche
“The battery cell is the combustion chamber of the future. As a new Porsche subsidiary, the Cellforce Group will be instrumental in driving forward the research, development, production, and sale of high-performance battery cells,” says Oliver Blume, Chairman of the Executive Board at Porsche. “This joint venture allows us to position ourselves at the forefront of global competition in developing the most powerful battery cell and make it the link between the unmistakable Porsche driving experience and sustainability. This is how we shape the future of the sports car.”
Porsche has been involved in the research of high-performance cells with silicon anodes for a while now; early research in this new battery technology has demonstrated it is possible to significantly boost the power density of cells compared to current batteries. New chemistry reduces the battery’s internal resistance, and it can offer the same energy content with a smaller footprint, and crucially, less weight. Silicon anodes effectively hold many more lithium ions, and they can move more freely than through graphite. An extra benefit is that lower-quality silicon can be used to no detriment, potentially making silicon anode Li-ion batteries cheaper than current graphite anode technology.
This graphic demonstrates how current batteries are charged and discharged. Image: Porsche
Porsche holds an 84 per cent majority stake in the new venture, which will be headquartered in the university town of Tübingen. The town is also a likely contender for a new battery cell factory, due to its proximity to the abovementioned development centre in Weissach and Porsche AG’s Stuttgart-Zuffenhausen headquarters.
The number of employees is expected to grow from the initial workforce of 13 provided jointly by both companies to up to 80 by 2025. The Federal Republic of Germany and the state of Baden-Württemberg are funding the project with around 60 million euros.
Michael Steiner, Boris Palmer, Torge Thönnessen, Winfried Kretschmann and Oliver Blume (f.l.t.r.)
“We founded Customcells with the aim of developing customer-specific battery cells for the most demanding of applications, and this is exactly what we can now realise together with Porsche. The goal for the planned production plant is to reach a minimum annual capacity of 100 MWh. This is equivalent to high-performance batteries for 1,000 vehicles,” explains Torge Thönnessen, CEO of Customcells. “We are not only contributing our expertise in cell technology and production into our partnership with Porsche, but also agility, innovative strength, and individual problem-solving skills,” adds Leopold König, who is also the new company’s CEO.
Source: Porsche
Energy Renaissance announces start of construction for Australia's first lithium-ion battery factory
Australia will soon be producing lithium-ion batteries onshore, thanks to start-up Energy Renaissance. With funding raised exclusively from private investors, Energy Renaissance has committed to manufacturing batteries at a site in Tomago, NSW, only a few kilometres from the Port of Newcastle.
Australia will soon be producing lithium-ion batteries onshore, thanks to start-up Energy Renaissance. With funding raised exclusively from private investors, Energy Renaissance has committed to manufacturing batteries at a site in Tomago, NSW, only a few kilometres from the Port of Newcastle.
Energy Renaissance’s 4,500 sqm purpose-built facility will manufacture Australian made batteries that are, according to the company “safe, secure, affordable and optimised to perform in hot climates.” Energy Renaissance will be manufacturing energy storage systems for the transport industry including busses and light commercial vehicles, as well as batteries for grid-scale, mining industry and community storage uses.
Energy Renaissance will have an initial battery production capacity of 48MWh per year and the capacity to expand to 180MWh per year in 2022. Energy Renaissance’s long-term plans are to develop a 1GWh battery manufacturing facility, and potentially grow to 5.3GWh over the next decade.
Construction of the facility will commence in April 2021 with a small-scale production trial run of batteries to start by July 2021, ramping up to full-scale production in October 2021.
CIS Solutions recently undertook an independent economic impact analysis, and concluded that an Australian advanced manufacturing industry supplying and exporting battery-grade chemicals and materials would create over 100,000 construction and 80,000 operational jobs and add AUD$7.3 trillion in export revenue. (Note that we haven’t been able to find a link to this study online)
There has been a dramatic decline in appetite for Australian iron ore and coal both domestically and internationally, and the Australian Government has been rather slow in realising that lithium—a metal found in abundance in Australia—has the potential to not only generate serious export dollars as global demand for batteries rises over the next decade, but to also shore up skilled manufacturing jobs locally, assisting the transition and retraining of mining sector workers.
Energy Renaissance is perfectly placed to take advantage of this; it’s investment to process raw materials locally in a region already known for mining means that the company should have a captive employment market available, as well as access to global markets via the nearby port.
With the New South Wales committing to purchase over 8,000 electric buses, this should present a great opportunity for Energy Renaissance to find local customers.
The government’s Minister for Industry, Science and Technology Karen Andrews and the Prime Minister, Scott Morrison were also present at Energy Renaissance’s manufacturing facility launch, and were keen to jump in with their own announcement, releasing the Resources Technology and Critical Minerals Processing road map in the Commonwealth Government’s Modern Manufacturing Strategy.
The Strategy has the following goals:
2 years: Improved capability to bring products quickly to market, through improved market development activities and investment made in critical enablers.
5 years: Foster increased collaboration with relevant sectors and international supply chains, increase exports and grow private sector investment.
10 years: Australia seen as a regional hub for resources technology and critical minerals processing, with significant R&D advancements, retention in intellectual capital for SMEs and significant volume and value of exports.
We’ll keep you updated as Energy Renaissance’s facility comes together.
Read more about the government’s strategy here: https://www.industry.gov.au/data-and-publications/resources-technology-and-critical-minerals-processing-national-manufacturing-priority-road-map