SEA Electric to purchase 1,000 battery sets from Soundon New Energy Technology Co for electric trucks
Global automotive technology company SEA Electric has expanded its global reach through the purchase of 1,000 electric vehicle batteries from long-time technology partner Soundon New Energy Technology Co. The newly formed arrangement immediately follows SEA Electric’s recently announced US$42 million in equity financing news.
Global automotive technology company SEA Electric has expanded its global reach through the purchase of 1,000 electric vehicle batteries from long-time technology partner Soundon New Energy Technology Co. The newly formed arrangement immediately follows SEA Electric’s recently announced US$42 million in equity financing.
Soundon has been providing SEA Electric with batteries since 2012, and the two companies have worked together closely on the development of seven SEA-Drive battery solutions over the course of the nine year relationship. SEA Electric is leveraging the cost benefits of Soundon’s battery and power electronics technical expertise, and their production efficiencies. The deal also allows SEA Electric to realise a significant 36 percent reduction in kilowatt hour (kWh) unit cost, and fulfilment of the battery production is expected to be completed in Q2 2021.
Soundon New Energy Technology’s manufacturing centre in China. Image: SEA Ealectric
According to Tony Fairweather, SEA Electric president and founder, Soundon is not only a world-class leader in innovation and battery technology, but highly regarded for its product quality, on time delivery, and competitive pricing. “Our long-term relationship with Soundon has been a very successful commercial journey and we anticipate continuing to share our global successes along the way.” While the majority of the initial 1,000 battery units are slated for the United States, the balance will go to SEA Electric inventories in Australia, New Zealand and Southeast Asia, along with the company’s first entry into the European market.
SEA Electric’s SEA-Drive technology fits hundreds of OEM platforms according to the company, with this large order from Soundon shared cross three major power-system models:
An Isuzu truck with SEA-Drive technology. Image: SEA Electric
SEA-Drive 70 – contains 88 kilowatt hours (kWh)
SEA-Drive 100 – contains 101 kilowatt hours (kWh)
SEA-Drive 120 – contains 138 kilowatt hours (kWh)
Wu Peng, Vice President of Sales and Marketing for Soundon commented that “this is a significant milestone in our partnership with SEA Electric. Receiving this 1,000-unit order not only facilitates SEA Electric’s substantial global growth, it also positions Soundon as a leader in the export market for commercial electric vehicles. It’s a winning proposition for all.”
With global headquarters and key leadership in Los Angeles, SEA Electric currently has operations in five countries and more than one million miles of independent Original Equipment Manufacturer (OEM) testing and in-service operation in all markets.
SEA Electric is an Australian success story, and currently partners with commercial vehicle OEMs, dealers, operators and upfitters to deliver zero-emissions trucks around the world. The company is expected to deliver more than 1,000 electric commercial vehicles this year. The company forecast is to have more than 15,000 vehicles on the road by the end of 2023.
Soundon New Energy Technology’s manufacturing centre in China. Image: SEA Ealectric
An example of SEA Electric’s SEA-Drive unit for OEMs. Image: SEA Electric
Vietnam's VinFast discussing potential EV battery and components deal with Apple supplier Foxconn
Vietnam's largest conglomerate Vingroup confirmed on Friday that its automotive subsidiary VinFast was in early stage talks with the Foxconn Technology Group about working together and that any partnership formed would focus on developing batteries and electric car parts.
Foxconn’s EV platform at a company event in 2020. Image: Reuters/Yimou Lee
Vietnam's largest conglomerate Vingroup confirmed on Friday that its automotive subsidiary VinFast was in early stage talks with the Foxconn Technology Group about working together and that any partnership formed would focus on developing batteries and electric car parts.
"Vingroup has received proposals from Foxconn but nothing is concrete yet. The partnership, if any, will focus on developing the batteries and electric car parts," a spokesman for Vingroup said. "No decision on working together to produce EVs has been made yet."
The flagship EV VinFast VF33 concept.
According to Reuters, Foxconn has put forward a proposal to VinFast to acquire their EV production lines, However VinFast would prefer a partnership as it remains keen to keep and grow its EV business.
Foxconn naturally declined to comment, however chairman Liu Young-Way also stated that the company may consider producing electric vehicles at its Wisconsin, USA plant, or look to setting up production facilities in Mexico. Liu described Foxconn as the "new kid in town" for vehicle manufacturing, and said the company needs to quickly build up its capacity to earn trust from clients.
Foxconn has been the world’s largest contract manufacturer for OEM’s for a few years now, and has openly stated that it has ambitions to shake up the automotive industry, but offering startup and established players alike a shortcut to competing in the electric vehicles market.
There’s no reason to expect that this can’t happen; Foxconn has moved quickly to establish deals with companies like Fisker and Byton. Recently Foxconn successfully established a deal with Zhejiang Geely Holding Group to provide contract manufacturing.
The VinFast LUX SA2.0 designed by Pininfarina. Image: VinFast
The VinFast LUX SA2.0 Interior.
Vinfast is the automotive arm of Vingroup, Vietnam’s largest conglomerate consisting of 48 subsidiary companies across real estate development, retail services, education, network security, healthcare and of course automotive manufacturing. The group has a combined estimated 50,000 employees, and a turnover in 2019 of 100 trillion VND - approximately $4.3 billion USD. Vinfast recently set up a research and devlopment arm in Australia, based in Melbourne.
The company sold around 30,000 vehicles in 2020, and plans to increase that by 50% in 2021. VinFast’s electric vehicle offerings are expected to begin hitting the domestic Vietnamese market by December 2021.
Source: Automotive News
Porsche aims for faster charging, higher energy density batteries and own fast charging network
As part of the Volkswagen Group’s inaugural Battery Day presentation, Porsche revealed continuing research and development into high performance battery and charging technologies, including the replacement of graphite with silicone in battery cell anodes.
As part of the Volkswagen Group’s inaugural Battery Day presentation, Porsche revealed continuing research and development into high performance battery and charging technologies, including the replacement of graphite with silicone in battery cell anodes.
Battery Technology
"The battery cell is the combustion chamber of tomorrow," says Oliver Blume, Chairman of the Executive Board of Porsche AG. "Our electrified high-performance sports and racing cars place the highest demands on battery technology. To meet these demands, Porsche needs special high-performance cells. Silicon has big potential."
Porsche’s Performance Battery Plus and 800V architecture as fitted to the Taycan Turbo.
An EV battery is made up of a few core components: the anode, cathode, separator, electrolyte, and one positive and one negative current collectors. Lithium ions are stored across both the cathode and anode, and the electrolyte carries these positively charged ions from the cathode to the anode during charging, and from the anode to the cathode during discharge (driving).
Porsche is looking at new battery cell chemistries to allow efficient operation in extreme temperatures, and to improve reliability and longevity in DC rapid charging. Porsche states that new batteries will begin testing in limited-production road vehicles and within their customer motorsport program. Porsche has also outlined a desire to ensure that there is a “completely European production chain for high-performance batteries”, implying a geopolitical need to avoid any reliance on dominant South Korean and Chinese cell providers LG Chem and CATL.
Battery modules in the Performance Battery Plus.
Porsche’s Own Charging Network
Porsche also announced plans to roll out a DC fast-charging network across important European autobahns, highways and motorways. Clearly looking to imitate Tesla’s Supercharger network—at least on a small scale—which provides industry-leading convenience and ease of use for Tesla owners, Porsche’s charging stations will feature six to twelve charging points, from 350kW and up.
The DC chargers at Porsche’s Leipzig customer centre could be a model for the company’s future highway chargers.
According to Blume, "An important prerequisite for electromobility is fast and convenient charging. That is why we are currently working on the details of a concept for our own fast-charging stations. We will select attractive locations for these in order to offer our customers the most comfortable and fastest long-distance travel experience possible."
Exact locations are not known at this stage, and plans outside Europe seem unlikely, but Porsche plans self-service lounge facilities with smartphone app access for its customers. These Porsche charging stations should complement the Ionity network nicely, and you can bet that the charging sites will feature Porsche’s usual high-end techno-minimalist look and feel. As the brand expands its electric offerings beyond the Taycan to the Macan and potentially the Cayenne by 2025, this rollout should quell future customers’ concerns about range anxiety, at least in Europe.
Porsche Leipzig’s customer centre features 350 kW DC/22 kW AC charging.
Nissan reveals paint colour palette for upcoming Ariya electric SUV
Nissan has unveiled a palette of ten exterior colours for the Ariya SUV, a pleasing change from the likes of Volkswagen which only offers a greyscale palette plus red or blue on expensive variants of its ID.4. There are four monotone and six two-tone options, and Nissan claims the paint portfolio was crafted to elevate Ariya’s premium look and feel.
Nissan Ariya boasts two bespoke colours, reduced CO2 output during paint process
Two brand-new colours have been developed by Nissan, Akatsuki Copper and Aurora Green
Technological innovations in the paint production line reduces carbon dioxide output by 25%
Nissan has unveiled a palette of ten exterior colours for the Ariya SUV, a pleasing change from the likes of Volkswagen which only offers a greyscale palette plus red or blue on expensive variants of its ID.4.
There are four monotone and six two-tone options, and Nissan claims the paint portfolio was crafted to elevate Ariya’s premium look and feel. The colours are applied by a highly advanced, environmentally sustainable paint production technology that reduces carbon dioxide output by 25% according to the company – further reducing the environmental footprint of this zero emission vehicle.
New colours for a new era of electrification
The design team developed Akatsuki Copper and Aurora Green especially for the all-electric coupé crossover. “The ingenuity the Nissan Ariya represents inspired us to adopt an entirely new mindset for colour design,” said Lesley Busby, Colour Manager at Nissan Design Europe.
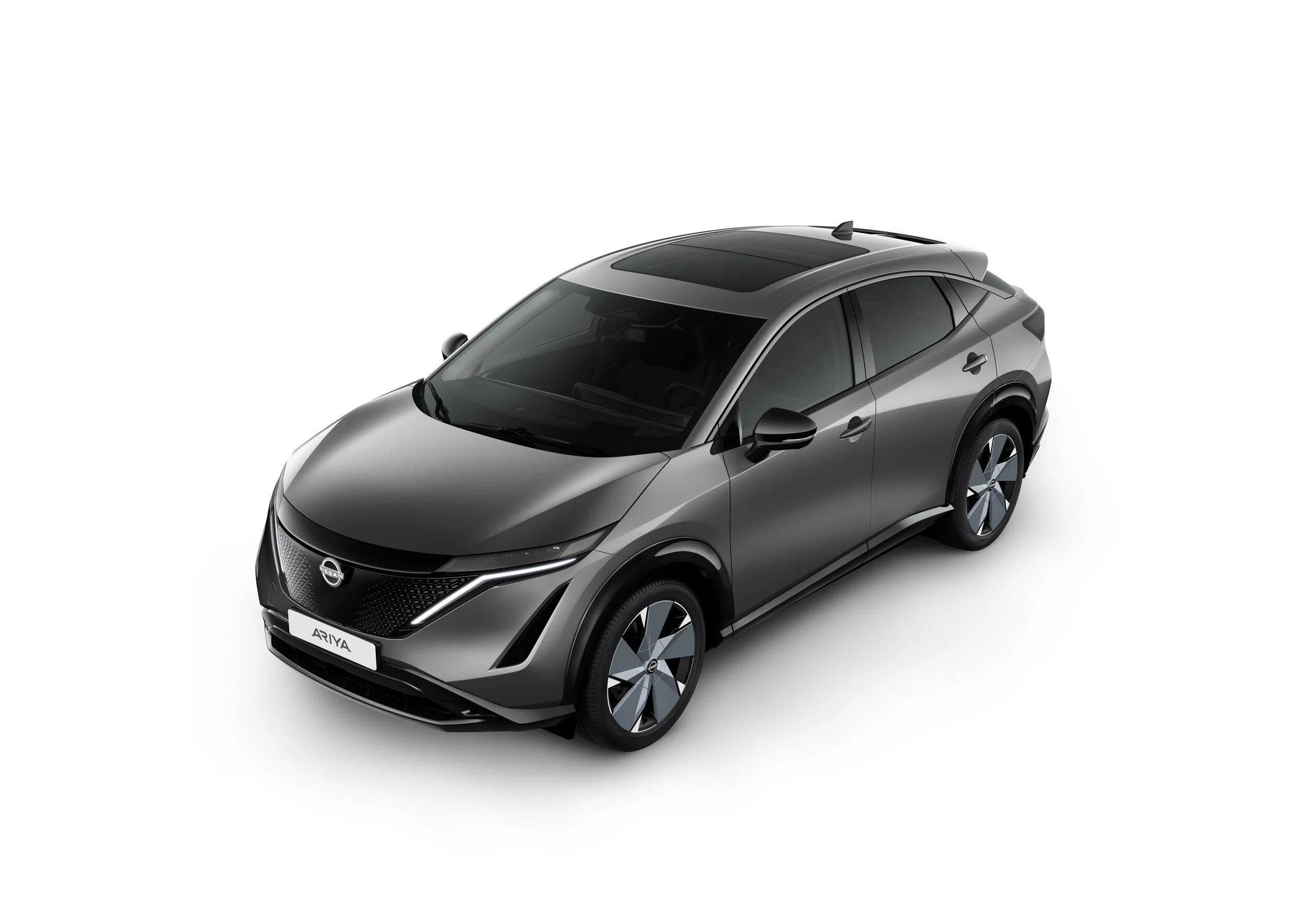


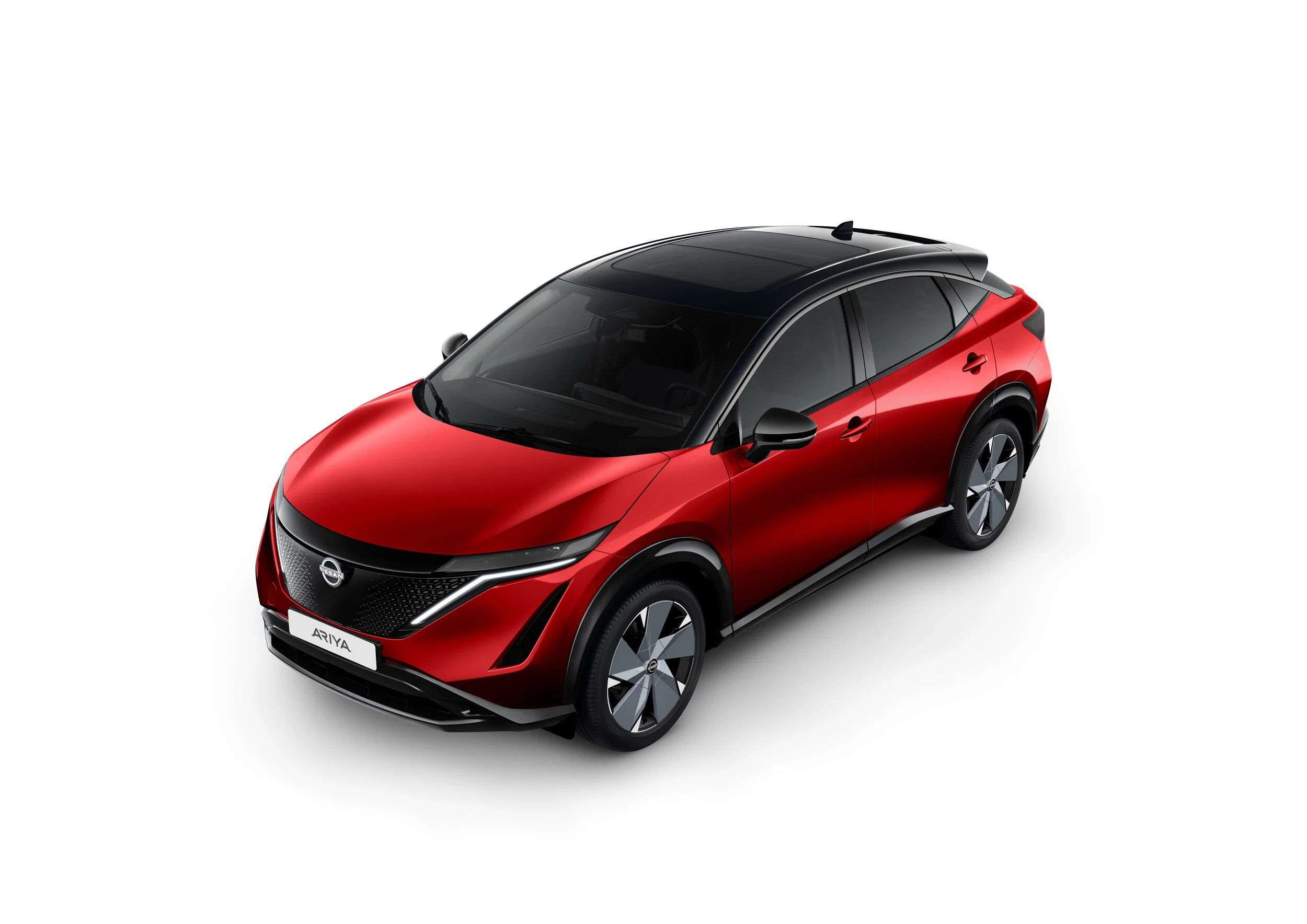

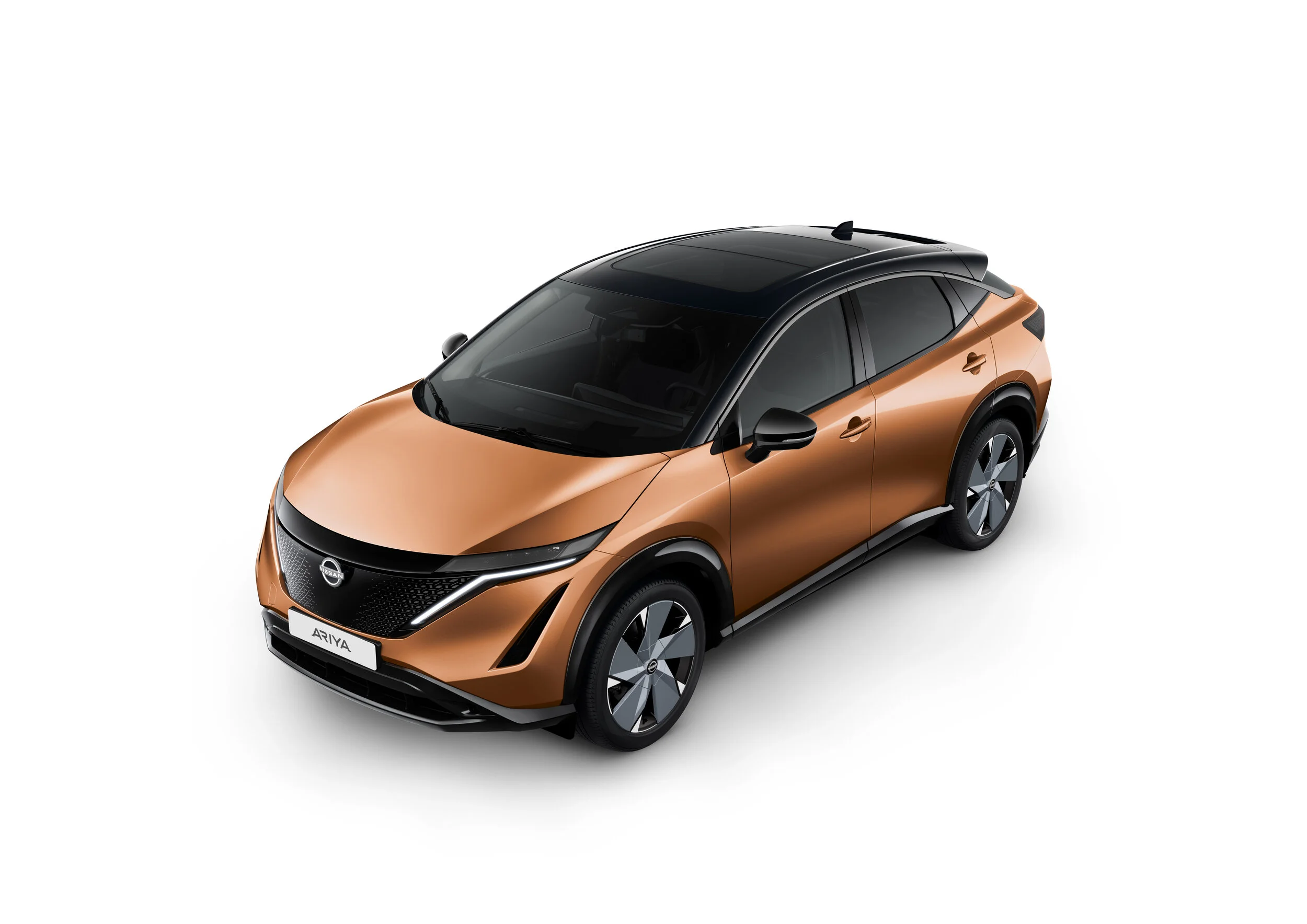
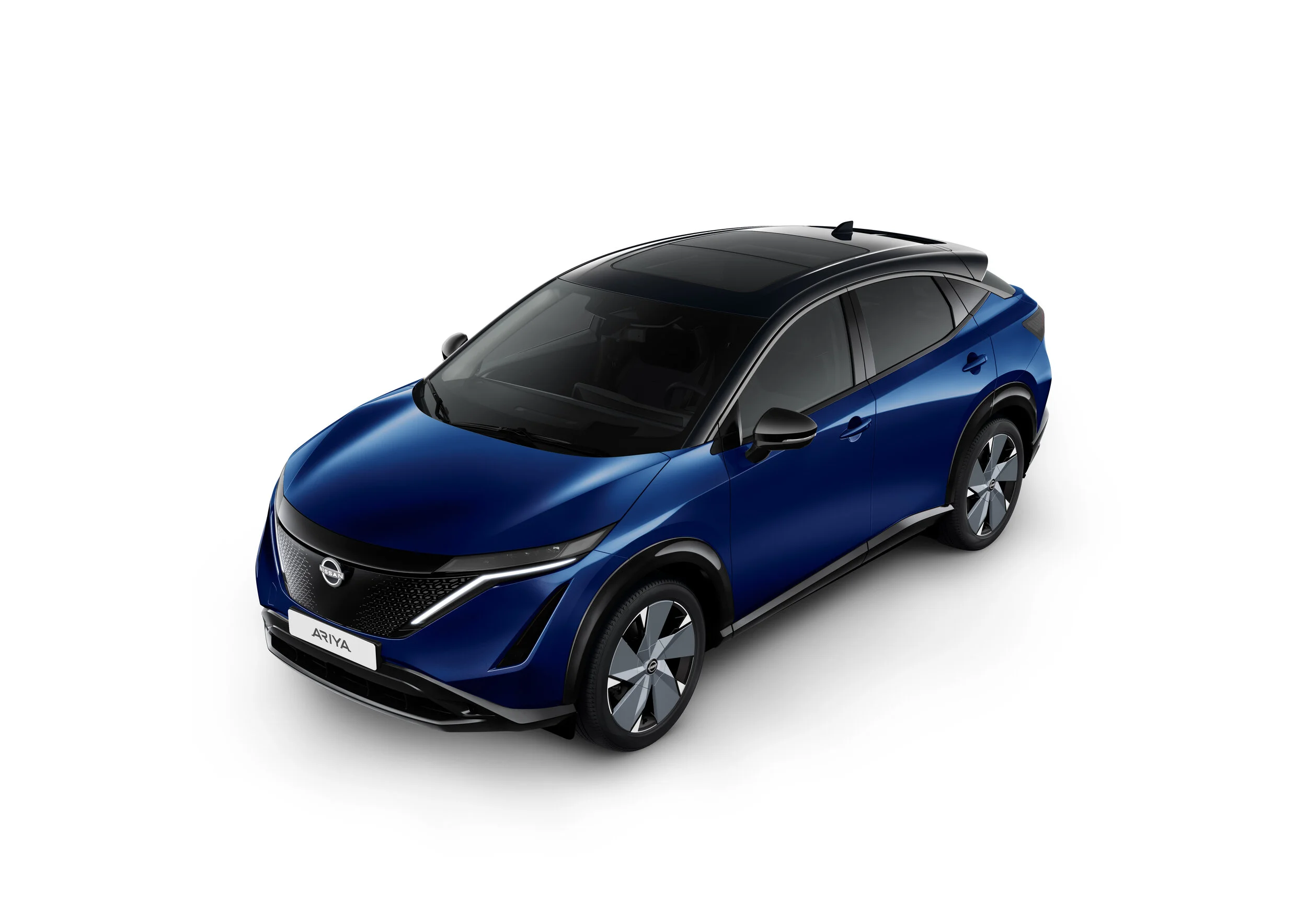


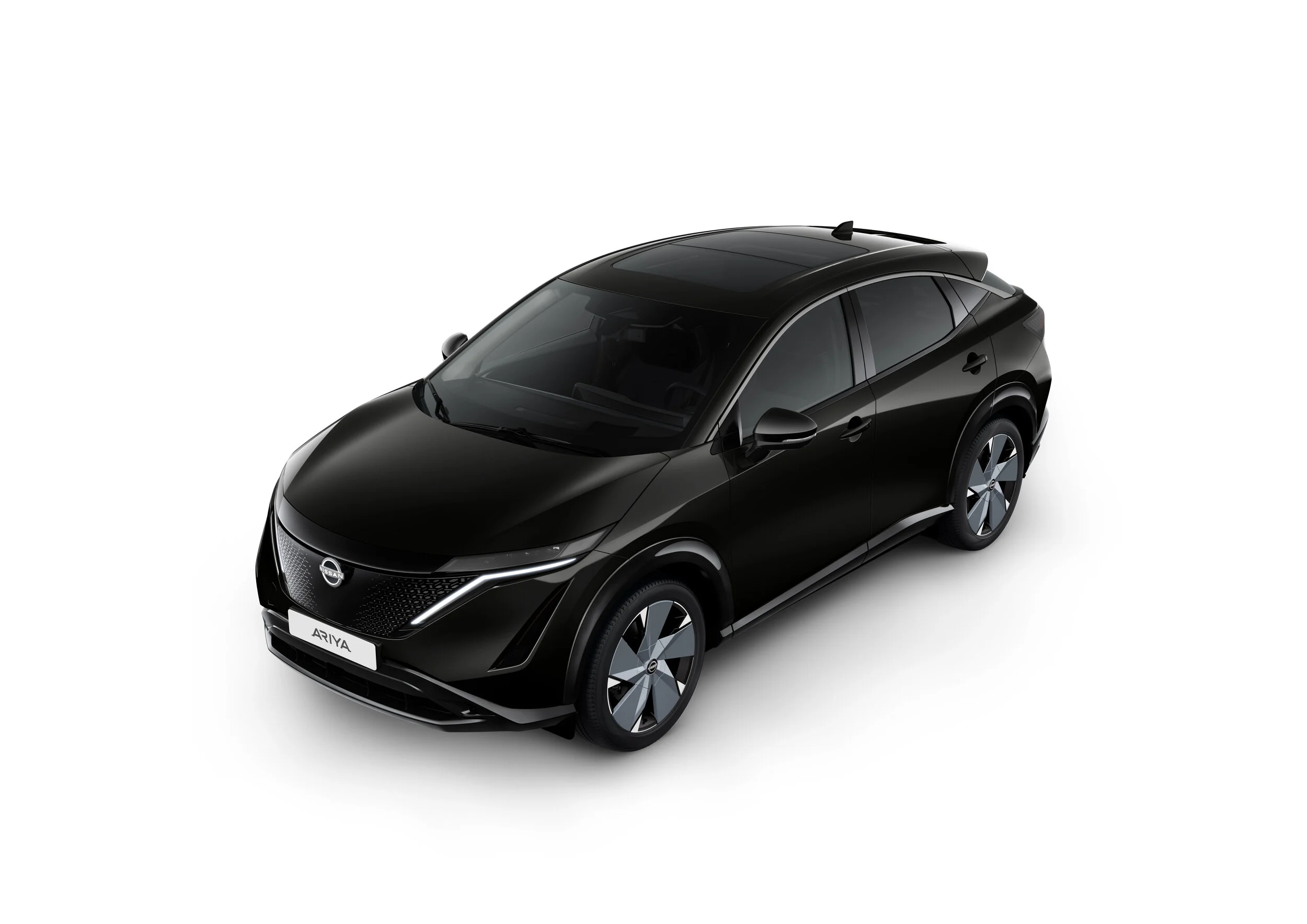
Nissan Ariya in Akatsuki Copper. Images: Nissan
“Ariya is the culmination of Nissan’s electric mobility expertise and a strong statement of intent for the future of EV design. We therefore worked hard to introduce a truly futuristic and technology-driven design language for the colours, analysing them in detail to create the perfect match for Ariya’s innovative personality,” Lesley Busby continued.
Inspired by the Japanese phrase for ‘dawn’, Akatsuki Copper’s striking appearance mimics the brilliance of a sunrise, reflecting the beginning of Nissan’s new brand identity. Its metallic sparkle is enhanced to evoke the conductivity of copper wires, honouring the model’s advanced EV technology.
Aurora Green takes its name from the beautiful ‘Northern Lights’ phenomenon, aurora borealis, commonly seen in the arctic. A sophisticated blend of different tones means the colour may appear green or purple depending on the angle that it is viewed, creating a sense of wonder and intrigue.
Technology innovation in colour
Nissan claims an all-new level of detail and depth to customer-favourite colours, created with state-of-the-art paint production techniques. Lesley Busby commented: “We know that black and white colours are some of the most popular options with vehicle owners in Europe and around the world. With Ariya, we have introduced a new level of richness and a premium veneer for these customer favourites. Combined with the quality and attention to detail seen throughout the colour palette, we’re excited for customers to experience Nissan’s new era of colour design for themselves.”
Sustainable production techniques
Technological innovation has also been employed to enhance the sustainability of the paint production line. Nissan has introduced a water-based paint which allows colours to be applied at a lower temperature, ensuring that each part of the vehicle can be painted together. This streamlines the entire application process, reducing carbon dioxide output by 25%.
The Ariya already has over 29,000 preorders worldwide according to Nissan, and is scheduled for a Japanese launch mid-2021 starting from 5 million yen ($66,700 AUD), and a European, Chinese and North American launch late in 2021.
While Nissan Australia has gone on the record as keen to import the Ariya, no Australian launch timing or pricing has been provided by the company. We’ll keep you updated if and when that changes.
Australian commercial EV manufacturer SEA Electric completes US$42 Million equity financing
This week, SEA Electric announced it has closed initial private placement equity financing for total gross proceeds of approximately US$42 million. The net proceeds from the investment will allow SEA Electric to solidify its position as a market leader in the electrification of commercial vehicles whilst funding its considerable backlog and facilitating more pilot programs with operators.
The SEA-Drive Power System. Images: SEA Electric
Founded in Australia in 2012, SEA Electric Holdings Pty Ltd. (SEA Electric) has become an international success story with its proprietary electric power-system technology (known as SEA-Drive®) now found across the world's urban delivery and distribution fleets.
With products in seven countries including USA, Canada, Australia, New Zealand, Thailand, Indonesia and South Africa, SEA Electric has more than one million miles of independently OEM-tested and in-service operation behind its technology.
This week, SEA Electric announced it has closed initial private placement equity financing for total gross proceeds of approximately US$42 million. The net proceeds from the investment will allow SEA Electric to solidify its position as a market leader in the electrification of commercial vehicles whilst funding its considerable backlog and facilitating more pilot programs with operators.
According to President and Founder Tony Fairweather, the financing allows SEA Electric to accelerate its global sales efforts and further utilize its proprietary Sea-Drive® 120b battery power system, while strengthening the delivery and distribution transportation segment for vehicles that operate in urban and metropolitan areas.
SEA Electric issued approximately 1.1 million Series A Preferred Shares at a price of US $40.1995 per share, convertible into common shares of SEA Electric at the option of subscribers and automatically convert to common shares under certain conditions, including SEA Electric completing a public transaction.
Fairweather stated, “We are very pleased to have completed a heavily oversubscribed equity financing and are excited to welcome aboard a global set of institutional investors as partners. The financing allows SEA Electric to grow our backlog as we explore options to seek a public listing in the United States this year.”
SEA Electric currently partners with commercial vehicle OEMs, dealers, operators and upfitters to deliver a new range of zero-emissions trucks and is on schedule to deliver more than 1,000 electric commercial vehicles this year. The company forecast is to have more than 15,000 vehicles on the road by the end of 2023.
“2021 will see a paradigm shift in the way developed markets facilitate uptake of commercial electric vehicles and the unstoppable momentum will build year-after-year” said Fairweather.
It is a notable achievement that in the face of lacklustre government support for clean technology in Australia, a company like SEA Electric has successfully conquered the international market in eight years. Companies like SEA Electric, Tritium and Evans Electric exemplify the technical and creative capital that exist in Australia that must be nurtured to support jobs, manufacturing and the transition to clean energy technologies.
Energy Renaissance announces start of construction for Australia's first lithium-ion battery factory
Australia will soon be producing lithium-ion batteries onshore, thanks to start-up Energy Renaissance. With funding raised exclusively from private investors, Energy Renaissance has committed to manufacturing batteries at a site in Tomago, NSW, only a few kilometres from the Port of Newcastle.
Australia will soon be producing lithium-ion batteries onshore, thanks to start-up Energy Renaissance. With funding raised exclusively from private investors, Energy Renaissance has committed to manufacturing batteries at a site in Tomago, NSW, only a few kilometres from the Port of Newcastle.
Energy Renaissance’s 4,500 sqm purpose-built facility will manufacture Australian made batteries that are, according to the company “safe, secure, affordable and optimised to perform in hot climates.” Energy Renaissance will be manufacturing energy storage systems for the transport industry including busses and light commercial vehicles, as well as batteries for grid-scale, mining industry and community storage uses.
Energy Renaissance will have an initial battery production capacity of 48MWh per year and the capacity to expand to 180MWh per year in 2022. Energy Renaissance’s long-term plans are to develop a 1GWh battery manufacturing facility, and potentially grow to 5.3GWh over the next decade.
Construction of the facility will commence in April 2021 with a small-scale production trial run of batteries to start by July 2021, ramping up to full-scale production in October 2021.
CIS Solutions recently undertook an independent economic impact analysis, and concluded that an Australian advanced manufacturing industry supplying and exporting battery-grade chemicals and materials would create over 100,000 construction and 80,000 operational jobs and add AUD$7.3 trillion in export revenue. (Note that we haven’t been able to find a link to this study online)
There has been a dramatic decline in appetite for Australian iron ore and coal both domestically and internationally, and the Australian Government has been rather slow in realising that lithium—a metal found in abundance in Australia—has the potential to not only generate serious export dollars as global demand for batteries rises over the next decade, but to also shore up skilled manufacturing jobs locally, assisting the transition and retraining of mining sector workers.
Energy Renaissance is perfectly placed to take advantage of this; it’s investment to process raw materials locally in a region already known for mining means that the company should have a captive employment market available, as well as access to global markets via the nearby port.
With the New South Wales committing to purchase over 8,000 electric buses, this should present a great opportunity for Energy Renaissance to find local customers.
The government’s Minister for Industry, Science and Technology Karen Andrews and the Prime Minister, Scott Morrison were also present at Energy Renaissance’s manufacturing facility launch, and were keen to jump in with their own announcement, releasing the Resources Technology and Critical Minerals Processing road map in the Commonwealth Government’s Modern Manufacturing Strategy.
The Strategy has the following goals:
2 years: Improved capability to bring products quickly to market, through improved market development activities and investment made in critical enablers.
5 years: Foster increased collaboration with relevant sectors and international supply chains, increase exports and grow private sector investment.
10 years: Australia seen as a regional hub for resources technology and critical minerals processing, with significant R&D advancements, retention in intellectual capital for SMEs and significant volume and value of exports.
We’ll keep you updated as Energy Renaissance’s facility comes together.
Read more about the government’s strategy here: https://www.industry.gov.au/data-and-publications/resources-technology-and-critical-minerals-processing-national-manufacturing-priority-road-map
Ultium Cells completes construction milestone at Ohio factory
Ultium Cells LLC, a joint venture between General Motors and LG Chem, aims to mass-produce Ultium battery cells at this new Ohio facility for General Motors’ next generation zero-emissions vehicles. GM and LG Chem are investing $2.3 billion in the facility to support EV manufacturing in the U.S., and in turn, local jobs, education, career training and infrastructure.
Ultium Cells factory under construction as GM nears 2022 launch date for next generation EV products
Ultium Cells LLC, a joint venture between General Motors and LG Chem, aims to mass-produce Ultium battery cells at a new Lordstown Ohio facility for General Motors’ next generation electric vehicles. General Motors and LG Chem are investing $2.3 billion in the facility to support EV manufacturing in the U.S., and in turn, local jobs, education, career training and infrastructure.
Working with LG Chem and General Motors, Ultium’s cells are of the large-format pouch design, and contain either vertically- or horizontally-stacked cells to integrate into GM’s upcoming modular EV platform – vertically for trucks, SUVs and crossovers, or horizontally for cars and performance vehicles.
Cadillac’s Lyriq is expected to debut GM’s new modular EV platform.
GM claims the batteries are able to be programmed digitally, as new chemistry is developed and becomes available, the battery management system could be upgraded digitally, similar to what Tesla already does with its over-the-air updates.
These high-capacity battery cells will also be switching to a Nickel Cobalt Manganese Aluminium chemistry, which reportedly uses 70% less cobalt than current technology.
The drive unit placement is also flexible, enabling front-, rear- and all-wheel drive variations. The motors were designed in-house at GM, and the modular platform is the first of its kind to support both front- and rear-wheel drive variants.
Ironworkers at Ultium Cells LLC’s battery cell manufacturing facility marked a construction milestone today with the final beam installation at what will soon be a 2.8-million-square-foot (260,000 square metre) operation in Lordstown, Ohio.
The team hoisted and installed the final beam as part of a traditional “topping out” ceremony, where leadership and trade partner employees had the opportunity to sign the beam and participate in a photograph.
Ultium Cells’ Ohio factory has topped out. Image: GM
Over 500,000 hours have been devoted to development of the facility, which is set to be completed in 2022. The framework of the building allows for an open floor plan, and the plant will equal the size of 30 football fields with an annual capacity of over 30 gigawatt hours of battery production, with room to expand.
“We are pleased construction at Ultium continues to progress safely and on schedule,” said Kee Eun, president of Ultium Cells LLC. “While we faced unprecedented challenges from the very beginning due to the COVID-19 pandemic, we have been able to execute successfully according to plan thanks to the collaborative efforts between General Motors and LG Chem, as well as the support and commitment from our contract partners and the local community.”
Ultium Cells is planning to create more than 1,100 new jobs in Northeast Ohio and is hiring to fill those positions currently.
Cadillac’s flagship Lyriq will likely be the first GM model to hit the market utilising Ultium Cells and GM’s new modular platform in the first quarter of 2022.
GM’s modular EV platform: Image: General Motors
Ford Europe to produce electric cars exclusively by 2030
Ford Europe has confirmed a commitment to sustainable profitability overnight, beginning a US$1 billion transformation of its Cologne manufacturing site to modernise its vehicle assembly facility, and create a home for the company’s planned e-mobility business.
Ford Europe to go all electric by 2030 with new models and new e-mobility factory in cologne
Ford plans for 100% of its passenger vehicle range in Europe to be zero-emissions capable by mid-2026, moving to all-electric by 2030
$1 billion will be invested in a new electric vehicle manufacturing centre in Cologne
The company’s first European-built, volume all-electric passenger vehicle for European customers will roll off the lines in Cologne starting in 2023
Ford will utilise Volkswagen’s modular electric-drive toolkit (MEB) to underpin the new vehicles
Ford Europe has confirmed a commitment to sustainable profitability overnight, beginning a US$1 billion transformation of its Cologne manufacturing site to modernise its vehicle assembly facility, and create a home for the company’s planned e-mobility business.
Ford states that 100 percent of their passenger vehicle range in Europe will be zero-emissions capable, all-electric or plug-in hybrid by 2026, and that the range will be completely all-electric by 2030.
The Mustang Mach-E, Ford’s all electric sports crossover. Images: Ford Motor Company
Interestingly, Ford will rely heavily on Volkswagens MEB platform architecture, with the German automaker tweeting about the deal, and claiming Ford will be using 600,000 MEB platforms and associated components by 2028:
Ford returned a profitable fourth quarter of 2020 in Europe, despite losses across the business globally. Ford recently announced US$22 billion would be allocated for e-mobility investment through 2025, across all its R&D and manufacturing facilities.
Ford’s announcement comes immediately after Jaguar Land Rover committed to electrifying their fleets over the next decade, with General Motors, Volkswagen and Volvo making similar commitments last year.
Ford’s E-Transit and Mustang Mach-E
JLR has big plans for 2025 with six EV Land Rovers, all EV Jaguar range
Jaguar Land Rover is racing headlong into an all-electric future, with plans revealed to scrap all combustion engine Jaguar models from the line up by 2025. In addition, the company plans to launch six all-electric Land Rover/Range Rover models by the same year.
Jaguar land rover commits to all-electric future; fully electrified Jaguar Range by 2025 and progressive roll out of land rover BEVs
Jaguar Land Rover is racing headlong into an all-electric future, with plans revealed to scrap all combustion engine Jaguar models from the line up by 2025. In addition, the company plans to launch six all-electric Land Rover/Range Rover models by the same year.
Jaguar represents the epitome of British tradition, and has often been accused of struggling to evolve with the times. The company suffered from a COVID-19 related sales decline in 2020, delivering 23.9% fewer units than 2019 . This new global strategy, referred to as “Reimagine” by Jaguar is a firm response to the EU block’s stringent CO2 and greenhouse gas reduction targets over the coming decade.
Jaguar’s I-Pace has been a sales success for the company
Under the leadership of Chief Executive Officer Thierry Bolloré, the Tata Group-owned Land Rover and Jaguar brands will rely on two separate electric architectures with two clear, unique personalities. The first all-electric Land Rover will arrive in 2024, with diesel engines likely to be phased out completely by 2026. Jaguar’s Model line up will be completely electrified by 2025. Although it’s not yet known which models will comprise this line up, Jaguar has confirmed the nearly complete electric XJ has been scrapped.
Jaguar Land Rover CEO Thierry Bolloré.
Jaguar’s I-Pace has been a relative success for the company, selling 7,807 units worldwide in Q4 2020. The I-Pace’s unconventional styling likely hints at the future of Jaguar’s line up: heavily skewed towards profitable SUVs, with a sport-oriented aesthetic and smart packaging.
Land Rover will use the forthcoming flex Modular Longitudinal Architecture (MLA). It will deliver electrified internal combustion engines and full electric variants as the company evolves its product line-up in the future. In addition, Land Rover will also use pure electric biased Electric Modular Architecture (EMA) which will also support advanced hybrid vehicles.
Land Rover’s Defender PHEV will eventually be joined by an all electric variant
Jaguar Land Rover will retain its plant and assembly facilities in the home UK market and around the world. As well as being the manufacturer of the MLA architecture, Solihull, West Midlands will also be the home to the future advanced Jaguar pure electric platform.
Jaguar Land Rover is aiming to achieve net zero carbon emissions across its supply chain, products and operations by 2039. The company is also carrying out research in fuel-cell powertrains, as many global economies look toward hydrogen. Jaguar claims fuel cell powered prototypes will be on UK roads within the next 12 months. Jaguar Land Rover plans to spend circa £2.5bn annually in electrification technologies and the development of connected services and technology.
Jaguar currently offers one all electric I-Pace model, plus hybrid versions of the F-Pace and E-Pace.
Volvo receives platinum medal in corporate sustainability rating from EcoVadis
Volvo Cars has received the highest rating for its sustainability performance from EcoVadis, a leading provider of corporate sustainability assessments, which has assessed over 75,000 companies in 160 countries.
EcoVadis awards Volvo highest corporate sustainability accreditation placing it in top one per cent of companies
Volvo Cars has received the highest rating for its sustainability performance from EcoVadis, a leading provider of corporate sustainability assessments, which has assessed over 75,000 companies in 160 countries.
According to EcoVadis, Volvo Cars’ sustainability performance deserves an Advanced ranking, based on the agency’s methodology. The resulting Platinum Medal rating places Volvo Cars in the top 1 percent among all 75,000 companies assessed by EcoVadis.
Volvo claims that this accreditation serves as further evidence that sustainability is as important as safety to Volvo Cars and has the highest priority throughout the company’s operations. Volvo Cars is already planning to manufacture all-electric vehicles exclusively in line with tightening emissions regulations from EU member countries.
“Sustainability is as important as safety to us at Volvo Cars,” said Anders Kärrberg, head of global sustainability at Volvo Cars. “We are taking action across the board to ensure we become a more sustainable business, including through reduction of our carbon footprint. It is encouraging that EcoVadis, through its rigid assessment, now confirms that we are on the right track.”
Volvo Cars has a comprehensive climate plan which addresses carbon emissions across all its operations and products, towards its ambition to become a climate-neutral company by 2040.
The plan goes beyond addressing tailpipe emissions through electrification; the company will also tackle carbon emissions in its manufacturing network and wider operations, its supply chain and through recycling and reuse of materials.
The XC40 Recharge is the first of many battery electric vehicles planned for Volvo’s product lineup. Image: Volvo Cars
As a first tangible step towards its 2040 vision, the company aims to reduce its lifecycle carbon footprint per car by 40 percent between 2018 and 2025.
EcoVadis looks at how companies implement sustainability across their supply chain. International companies in a variety of industries, and in particular large fleet buyers, use the ratings published by EcoVadis for their purchasing decisions to move away from unsustainable and unethical suppliers.
In its rating of Volvo Cars, EcoVadis highlighted several of the company’s ongoing sustainability activities and initiatives. It positively mentions its CO2 reduction actions across the supply chain, the verification of its sustainability strategy by the Science Based Targets Initiative (SBTI) and Volvo Cars’ work to improve energy efficiency and the efficient use of material and resources.
Elsewhere, EcoVadis also highlights Volvo Cars’ work to promote diversity and inclusion, its initiatives around protecting labor rights, the company’s extensive ethical business training program and its focus on sustainable procurement around the globe.
Lucid Motors reveals Arizona factory paint shop; targets 400,000 units per year across four models
On the back of news that Tesla Motors has begun construction on what may be the world’s most advanced automotive paint shop, Lucid Motors has released details on its paint shop under construction in its AMP-1 factory, located in Casa Grande, Arizona.
Lucid’s Arizona factory to produce high-end paint finishes, starting with 30,000 Lucid AIR Sedans per year
On the back of news that Tesla Motors has begun construction on what may be the world’s most advanced automotive paint shop, Lucid Motors has released details on its own paint shop currently under construction in its AMP-1 factory, located in Casa Grande, Arizona.
Lucid Motors’ competitor Tesla has been criticised in the past for many poor (and downright ghastly) paint jobs over the years. Recently however, Sandy Munro was thoroughly impressed with the exterior paint on a brand new 2021 Model—anecdotal evidence of course—which implies things may be improving in Tesla’s paint shop and its QA checks.
For many, Porsche has always been held up as among the best in the business when it comes to high-grade exterior finishes, and Lucid is clearly watching the big German manufacturers and Tesla closely to ensure its vehicles’ paint matches the company’s luxury image.
A Lucid Air after what appears to be the pretreatment and sealer phases of the painting process.
According to Mike Boike, Director of Manufacturing, “We're competing against the best in the world, and we know it.” he added. “So the processes and the materials that we use are nothing but the best in the world. We've got the latest and greatest paint process. We have the latest and greatest materials, and we have a high-powered team of engineers and manufacturing professionals.”
Lucid’s paint shop process involves the following steps:
Pretreatment and Electrocoat: As each Lucid Air comes out of the body shop, it gets rigorously cleaned. Then we apply both a thin film coating and electrodeposition coating, which protect the entire body structure from corrosion.
Sealer: Next we thoroughly seal the vehicle to prevent any type of air or water intrusion that could create road noise or water leakage into the car.
Paint: Once the unit is sealed and sanded, it’s then sent into the paint booth. Here, we’ve integrated the latest innovative process and materials technologies that result in a flawless, luxurious finish.
Finesse: Finally, post-bake, the car is brought to the finesse deck where a team inspects and polishes it to perfection before approving to ship to the customer.
Lucid’s automated painting process
Lucid plans to commence building the Air sedan in 2021, and is aiming for 30,000 vehicles in its first full year of production. According to the company, it’s more economical to build the paint shop based on the eventual full capacity of the plant, which is 400,000 units per year.
Lucid’s second model line, a luxury SUV codenamed “Project Gravity”
Lucid’s second vehicle will be a luxury SUV currently codenamed Project Gravity, which will arrive in 2023.
Source: Lucid Motors
Sandy Munro Evaluates the Engineering behind the latest 2021 Tesla Model 3
In his down-to-earth yet comprehensive way, Chief Executive Officer Sandy Munro of Munro and Associates has purchased a 2021 Tesla model 3, and proceeded to look under the skin to show us the engineering improvements from the company.
In his down-to-earth yet comprehensive way, Chief Executive Officer Sandy Munro of Munro and Associates has purchased a 2021 Tesla model 3, and proceeded to look under the skin to show us the engineering improvements from the company.
Munro looks at the front trunk or “frunk”, and demonstrates big improvements in design, moulding shape and in the plenum intake. He also takes a look at the company’s improvements in terms of cost savings on unnecessary clips and plastic pieces, and he seems impressed with Tesla’s Octovalve, now named “super manifold”, and overall, in terms of the engineering at least, Munro says that he can’t find any fault under the body panels, and that Tesla’s design and build of core components is excellent.
It’s not all roses and sunshine however, as even on this latest iteration of the Model 3, Sandy Munro finds inconsistency in panel gaps from one side of the vehicle to the other. For all the advanced engineering in the Model 3, Sandy remarks that consistency in production quality is something that Tesla should be able to easily achieve, so why are cars still having issues?
Rivian announces new funding windfall; company valued at $27.6 billion
Rivian has raised USD$2.65 billion as it readies itself for production of the all-electric R1T pickup truck this July.
Rivian closes January 2021 investment round with $2.65 billion
Rivian has raised USD$2.65 billion as it readies itself for production of the all-electric R1T pickup truck this July.
Spearheaded by funds and accounts advised by T. Rowe Price Associates Inc, investors included Fidelity Management and Research Company, Amazon’s Climate Pledge Fund, Coatue and D1 Capital Partners as well as “several other existing and new investors” according to Rivian.
Rivian has already raised close to $USD8 billion since early 2019, but as we all know, manufacturing a vehicle is not an inexpensive task. Rivian has spent almost $1 billion on the former Mitsubishi factory in Normal Illinois where it plans to commence manufacturing operations this year. The company plans to produce the R1T Pickup, R1S SUV as well as the Rivian/Amazon delivery van there.
Rivian CEO and founder RJ Scaringe said in a statement “The support and confidence of our investors enables us to remain focused on these launches while simultaneously scaling our business for our next stage of growth,”
According to Chicago Business, a person familiar with the workings of Rivian’s funding said that the company is presently worth around US$27.6 billion. Any suggestions that Rivian might be going public with an IPO sometime soon have been quashed by Scaringe, who stated in the video below that “the company is focused on the product and back-end operations for the next year”, indicating we’re unlikely to see an IPO in the shirt term.
Source: Rivian
Meet SAIC Motors' New Premium Electric Vehicle Brand Zhiji Auto
As electrification drives the convergence of traditional manufacturers and big Tech, SAIC Motors has announced a joint venture with Alibaba Group and Shanghai’s Zhangjiang Group to release electric vehicles under a new brand dubbed “IM”
Zhiji IM sedan launching in 2021
As electrification drives the convergence of traditional manufacturers and big Tech, SAIC Motors has announced a joint venture with Alibaba Group and Shanghai’s Zhangjiang Group to release electric vehicles under a new brand dubbed “IM”, which also signifies “Zhiji Motor” in Mandarin Chinese. “IM” stands for “Intelligence in Motion”, and will join the suite of brands in SAIC Motors’ stable including Roewe Motors, MG, Maxis and SAIC.
The company has yet to release detailed information about the future models under the “IM” brand, but has announced that it is working on a luxury sedan to rival NIO’s new ET7. The “IM” sedan measures 5,000mm long, 1,960mm wide and 1,485mm tall; similar to NIO’s upcoming sedan. Electrive reports that Liu Tao, the co-CEO of Zhiji Automobile, said in an interview with Chinese media that the IM brand was there to “kill” Tesla.
Sources have stated that the sedan will feature energy dense batteries from Contemporary Amperex Technology Co. Limited (CATL), autonomous driving capabilities from Nvidia’s drive technology, and based on the released images, roof-mounted Lidar.
There will be 93 kWh or 115 kWh options, which will be available for order in Q2 2021. In 2022, Zhiji Motor will launch a luxury SUV.
With murmurings around a partnership between Apple and Hyundai, this joint venture makes a lot of sense; SAIC will focus on manufacturing — something it obviously excels at as China’s largest automaker — and Alibaba will hold responsibility for AI technology and the data side of vehicles.
More information is expected as April’s Shanghai Auto Show nears;
Source: Gasgoo
Tesla Closes 2020 with a Record Q4 and 500,000 Vehicles Delivered
Tesla delivered 499,500 vehicles for the 2020 calendar year, and produced 509,737 vehicles. That’s almost 10x the production output from 2015. Many Wall Street analysts dismissed Tesla’s 500,000 unit goal for the year, as the onset of COVID-19 impacted the automaker’s production facilities around the globe…
Freemont Outbound Delivery Lot - Image: Tesla
Tesla delivered 499,500 vehicles for the 2020 calendar year, and produced 509,737 vehicles. That’s almost 10x the production output from 2015. Many Wall Street analysts dismissed Tesla’s 500,000 unit goal for the year, as the onset of COVID-19 impacted the automaker’s production facilities around the globe, and negatively affected sales across the broader passenger car market.
Image: Tesla
Five years ago, the company’s CEO Elon Musk emphasised a plan to reach a delivery target of 500,000 vehicles per year by 2020. At the time, this number seemed overly ambitious, as production difficulties, cashflow troubles and quality concerns seemed to be the most interesting stories to the media.
After a string of profitable quarters, successful launch of the Model Y and massive capital expansion, 2020 culminated in Tesla’s listing on the S&P 500 index, and a massive push to increase production by year end.
Tesla produced 179,757 vehicles and delivered 180,570 vehicles in Q4, up 42 per cent and 36 per cent respectively on Q4 2019 numbers. In Q3 2020, Tesla produced 145,036 vehicles and delivered 139,300 vehicles.
Elon Musk took to Twitter to mention the thousands of employees who contribute to Tesla’s continued success:
Investors and the majority of analysts have been very bullish on Tesla at the end of 2020, and the stock has surged past $705 US per share as at market close on December 31. Despite this, The New York Times, amongst other media outlets still falls into the trap of labelling Tesla as an “upstart automaker [that] will probably face stiffer competition in 2021.”
While its true Tesla has ongoing customer service and quality issues to address, and a huge amount of work ahead to continue to scale to meet future production and delivery targets, it’s dangerous to not see Tesla for what it now is; an energy company with the best automotive software on the market, and likely the best electric vehicles available today.
We can expect the full Q4 and calendar year 2020 earnings to be reported in late January or early February.
Tesla End of Year Wrap Up
The electric vehicle market is booming, despite COVID-19 putting the brakes on the auto industry generally. Of course Tesla has become a darling of investors, with the company seeing a 50% share price increase since the announcement in early November that the automaker was entering the S&P 500.
The electric vehicle market is booming, despite COVID-19 putting the brakes on the auto industry generally. Of course Tesla has become a darling of investors, with the company seeing a 50% share price increase since the announcement in early November that the automaker was entering the S&P 500. Not since Yahoo and the dot com boom in the late nineties have we seen such confidence in the future of a company.
Tesla isn’t one to slow down for the holiday season, and with a final production and deliveries push expected, Gigafactories across the world under construction, charging infrastructure and vehicle updates, we look at the news this week, and what we can expect to see in the new year.
Sales & Deliveries
North American and European sales of Model 3 and Y remain strong, and the company has apparently met (admittedly low) Model S and X targets for the year, and has halted production for these vehicles.
Tesla sales are strong in China, and this is the market that will help push Tesla to its 500,000 unit goal in 2020. Indeed, many analysts and commentators believe Tesla will surpass this target. With over 20,000 ‘made in China’ Model 3s sold in November, that demand looks set to continue through December, just as the Model 3 was recently awarded Number 1 electric vehicle in China by owners in a recent Net Promoter Score (NPS) index survey. Any concerns around battery availability have subsided, as Tesla’s Chinese production recently moved to lithium iron phosphate (LFP) batteries from supplier CATL.
In Q4 2019, Tesla delivered 112,000 vehicles. Tesla has been ramping production in Q3 and Q4, and Rob Maurer of Tesla Daily has projected just over 24,000 units of Model 3 in production from Giga Shanghai in December. His other projections include:
53,000 Model Y units produced in Q4;
58,000 Model 3 units produced in Q4;
19,000 Model S and X units produced in Q4;
530,000 total units produced in 2020
Tesla needs 181,000 deliveries worldwide to achieve the 500,000 unit annual target. Watch Tesla Daily’s Q4 prediction video below:
Factories
As was expected, construction of Giga Texas is powering forward, with the skeleton and roof of the facility already under construction, and the first phase of the project due for completion in 2021.
Over in China, Tesla completed the Model 3 and Model Y production lines in record time, and new single-piece body castings have been spotted at the factory, suggesting Tesla’s new ‘Gigapress’ casting machines are now online.
Tesla certainly isn’t resting though, and it appears the company is continuing to expand the production facility east of the current footprint:
Meanwhile, over in Germany, Giga Berlin is also charging full steam ahead, with ‘Gigapress’ casting machines arriving at the factory, and external walls being erected, despite a number of hold ups due to permits, environmental concerns and missed payments. Again, Tesla is expected to commence operations on time if not earlier, with production tests due for July 2021, some 13 months after construction on the site began.
FSD pricing and updates
Tesla’s autonomous Full Self Driving package is set to become a cash cow for the company, with the billions in R&D dollars spent set to be recouped over the next few years. Previously available as a stand-alone option before or after delivery for a cost of $10,000, Tesla announced 2021 will bring a subscription pricing model for owners who wish to pay for the option in instalments.
Tesla has also just released its holiday 2020 update, as part of Firmware 2020.48.25. There are some notable changes mentioned in the release notes including:
“The driving visualization has been refreshed and now offers a larger visualization to allow drivers to view more details of the road surroundings. The next turn will now appear above the visualization if the navigation turn list is covered by another app.”
“Schedule departure can now precondition your battery and cabin even when your car is unplugged. To account for different utility rate plans, you can now set the time when your off-peak rates end to save on charging costs. To access, tap SCHEDULE from the climate control or charging panel when parked.”
“Supercharger pins on your touchscreen will now display the number of available stalls at charging sites. Quickly search for nearby amenities by tapping an amenity icon on the Supercharger popup display.”
Teslarati has a full rundown of software changes listed here
Superchargers
Can electric vehicles from brands other than Tesla now charge at Tesla Superchargers? Not quite. Marques Brownlee asked Elon Musk on Twitter “Why don't more electric car makers take up Tesla on their offer to use the Supercharging network? Incompatible tech? Hidden fees? Pride? There's gotta be a good reason.” to which Elon Musk replied: “They are, although it’s kind (sic) low-key. Tesla Superchargers are being made accessible to other electric cars.”
Naturally, the internet went crazy, though you won’t see Porsche Taycan owners at a Supercharger any time soon. Tesla is focused on rolling out Superchargers for its customers, installing the high-speed Tesla-only chargers in more locations, and updating more Supercharger sites from 150kW version 2 models to 250kW version 3 models. Construction of Tesla's Supercharger factory in China appears to be ramping up too, and has a 10,000 unit per year production goal.
S&P 500 Inclusion
The big news this week is the inclusion of Tesla into the S&P 500 club; a move that many have signalled since Tesla achieved four straight profitable quarters in July this year. According to the Wall Street Journal, shares have surged some 70% since the announcement of the company’s addition in November.
Tesla’s listing on the stock market benchmark represents the biggest company ever to join the S&P 500, and its USD$650 billion market capitalisation figure means Tesla is the sixth largest publicly listed company in the United States.
1990 to 2020: Largest Companies Added to the S&P 500
Elon Musk appeared extremely grateful on Twitter, Tweeting on December 22 “Thanks to everyone who worked so hard to make Tesla successful. My heart goes out to you.”
Tesla is now the world’s most valuable automaker, with huge growth potential and some serious competitive advantages in the market place (more on that below).
The Street has just named Tesla as its ‘number one stock of the year’, with 12 of 16 panellists agreeing Tesla stood above Zoom Video, Moderna, Amazon and Netflix (numbers two to five respectively)
Image: The Street
What about Tesla Energy?
The growth of Tesla Energy is part of the reason many investors see so much future potential in the company; while solar and household battery growth has been slow over the last few years, Q3 and Q4 2020 were good quarters for the business, and Tesla energy looks to have generated around $1.85 billion in revenue for the 2020 calendar year.
According to The Motley Fool, During Q3 2020, Tesla shipped 759 megawatt-hours (MWh) worth of batteries, an 81% increase from Q2's 419MWh. That’s a higher rate of growth than Tesla’s automotive business, which saw shipments for Q3 at 139,593 units, a sequential increase of 54% over Q2's 90,650 units.
We can expect to see more grid-scale battery projects boosting the energy business in 2021; recently a number of large projects utilising Tesla Powerpack and Megapack technology have been completed, including Yorktown New York’s 490 MW Tesla battery, and an upgrade of an additional 50 MW added to the Hornsdale battery in South Australia. Construction commenced in October on the 182 MW (730MWh) Moss Landing battery in California, which consists of 256 Megapacks, and will be able to power every home in San Francisco for up to six hours according to Tesla.
Tesla Solar has been bubbling away for a few years now, and the company’s energy products have become on average 30% cheaper than the US average primarily due to their online business model. By reducing ‘soft costs’ or non-component costs of each system, customers are able to purchase customised packages that suit their homes, and can even pay off the installed system through a subscription program.
Many in the industry believe that Tesla Energy can generate revenue equal to that of the automotive side of the business, and that it’s just a question of scaling up production, and expanding subscription-based solar and battery systems outside the United States.
What else could possibly happen in 2020?
Well now that you mention it, according to Reuters, there’s a little something called ‘Project Titan’ that the Cupertino tech giant Apple is working on. It’s an electric vehicle that has been in the works since 2014, and part of the secret vehicle’s competitive advantage will apparently be a new battery design that could “radically” reduce the cost of batteries while maximising range.
Gene Munster from Loup Ventures doesn’t see Apple’s entry into personal mobility as a threat to Tesla’s market share; Munster stated that the firm believes traditional automakers are Apple’s target.
Loup Ventures predicts that electric vehicles will account for close to 30% of all auto sales by 2025, with one third of that market to be dominated by Tesla.
Elon Musk dropped quite the Tweet today, stating that during the company’s Model 3 design and engineering phase, he approached Apple to see if Tim Cook was interested in acquiring Tesla: “During the darkest days of the Model 3 program, I reached out to Tim Cook to discuss the possibility of Apple acquiring Tesla (for 1/10 of our current value). He refused to take the meeting.”
How different the automotive and energy landscape could have been…
What’s in store for 2021
So what will next year bring? Like many investors (myself included), Tesla experts see exceptional growth for the company, based on strong demand for electric vehicles generally, and increasing market share in key markets such as China. Wedbush analyst Daniel Ives believes China’s demand dynamic in the EV market will disproportionally benefit Tesla, and that the Chinese market could account for over 40% of Tesla’s sales within eighteen months.
Gali from Hyperchange demonstrates that Tesla has already figured out how to build electric vehicles profitably, with a gross margin figure of 23 percent. He sees a lot more growth potential on a profit per car basis, as the company focuses on software, and begins to recoup costs associated with the research and development of the Full Self Driving software. Gali is projecting a gross profit amount of $2.5 billion for Q4 2020, $2.7 billion in cashflow, and he expects capital expenditure to increase to $4-$6 billion per year from 2021 as Tesla pours more money into factories.
Model Y sales and deliveries are expected to get off the ground early in 2021, and with the Cybertruck Gigafactory due for completion mid-year, 2021 could be the year that Tesla brings the first mass-market electric pickup truck to consumers.
Tesla also unveiled its new 4680 battery cells in September, and the new tabless cells are expected to offer exceptional thermal and electrical efficiency. These cells are expected to be at the core of Cybertruck and Semi performance and efficiency, and while Tesla has these cells currently deployed in prototypes, the company lacks a facility to manufacture them at scale.
One of Tesla’s main goals is terrawatt-hour (TWh), or one trillion watt hour scale battery production, and the company has a manufacturing goal of 3TWh by the year 2030. Elon Musk has also used Twitter to suggest Tesla may be able to manufacture 20 million vehicles a year by this date:
Clean Technica has an excellent article on Tesla’s future that delves deeper into the above, however any future light commercial vehicles from the company are notably absent. With Rivian, Arrival and other manufacturers seeing this segment as a growth market for EVs, I wouldn’t be surprised to find Tesla leveraging their expertise to manufacture delivery vehicles.
2020 has been a difficult year for the automotive industry, but I am cautiously optimistic that Tesla’s battery and vehicle roadmap will play out in their favour, and that we will continue to see the company scale and grow at a rapid rate. Say what you like about Elon Musk; Tesla is now much bigger than one man, and the company has driven the global automotive market rapidly towards electrification and zero emissions transportation.
Mercedes-Benz Accelerates EV Rollout; 8 BEVs In Production by 2022
Mercedes-Benz has today announced announced its ambition to fully electrify the entire product portfolio by 2039 as part of a plan to achieve CO₂ neutrality, and this includes the rollout of eight all-electric Mercedes-EQ models from 2022 built on dedicated electric architecture. The first mass-market Battery Electric Vehicle (BEV) from Stuttgart, the Mercedes-Benz EQC has been available around the world since 2019, and is based on the pre-existing GLC SUV platform.
Images: Mercedes-Benz AU
Update: Mercedes-Benz has released an additional rendering, which you can find below. This vehicle looks to be pretty close to final production design, and will be Mercedes’ first D-segment vehicle without a traditional grille.
Mercedes-Benz has today announced announced its ambition to fully electrify the entire product portfolio by 2039 as part of a plan to achieve CO₂ neutrality, and this includes the rollout of eight all-electric Mercedes-EQ models from 2022 built on dedicated electric architecture. The first mass-market Battery Electric Vehicle (BEV) from Stuttgart, the Mercedes-Benz EQC has been available around the world since 2019, and is based on the pre-existing GLC SUV platform.
The Mercedes-Benz EQS, as shown above and below will be the first to commence production in early 2021, and is essentially the luxurious S-Class reimagined for a zero emissions future. From the camouflagued vehicle, we can see an imposing physical presence -something the S-Class has always been known for- and a low, wide nose, possibly with a faux grille a-la Jaguar i-Pace or an indentation around the badge. The bonnet (hood for you North Americans!) rises steeply into a huge windscreen, which appears to continue above the driver’s head, as is the trend nowadays.
The high bootline and almost fastback look is unusual for the S-Class segment, however the large tail lights with some presumably funky graphics and lightbar spanning the width of the rear should provide a visual family reference to the EQC, while defining the EQS’ unique character.
The side profile looks a little slab-sided under camouflague, with the C-pillar, doors and rear fender covering a large area relative to the glasshouse, however it looks like there may be some interesting surfacing hiding under that blue wrap. The Goodyears on the test car look to be hugging at least 21-inch or 22-inch wheels, as is the trend these days. That’s aesthetics over efficiency for you.
The EQS will be produced in Sindelfingen from early 2021, while the less expensive EQA and EQB models will be produced at the Rastatt and Kecskemét (Hungary) plants respectively. We can expect the world premiere of the EQA on January 20, 2021 according to Mercedes-Benz.
Fast forward to the second half of 2021, and Mercedes-Benz states that the EQE ‘business sedan’ will begin production at the Bremen plant, as well as in Beijing for the Chinese domestic market only. Continuing the the Germans’ fondness for manufacturing SUVs in the United States, the EQE and EQS SUV variants will be manufactured at the brand’s Tuscaloosa Alabama plant.
According to Mercedes, a total of eight Mercedes-EQ electric vehicles will be produced at seven locations on three continents by 2022.
Daimler’s Battery Plans
Battery development, manufacture and supply will obviously be a critical part of this increase in BEVs, and Mercedes-Benz plans to increase investment in the energy side of manufacturing, alongside battery specialists.
Mercedes-Benz and BAIC have jointly set up a battery production plant at the existing location in the Yizhuang Industrial Park in Beijing (China) for vehicles sold in the domestic market.
In addition to two battery plants in Kamenz (Germany) already producing battery systems for Mercedes-Benz, the company plans a future battery plant at the Sindelfingen site, increasing capacity already available from the nearby Untertürkheim plants in preparation for locally built electric models.
Furthermore, Mercedes-Benz is upgrading the Jawor (Poland) battery plant, currently manufacturing battery packs for plug-in hybrid variants of the C,E and S-Classes, to include battery systems for upcoming EQ models, as well as planning a battery plant in the vicinity of the Tuscaloosa Alabama factory.
You can read the full press release below, alongside an interview with Jörg Burzer, Member of the Board of Management of Mercedes-Benz AG, Production and Supply Chain.
Mercedes-Benz Sindelfingen plant (Germany): Launch of electric luxury sedan EQS in Factory 56 in first half of 2021
Mercedes-Benz Rastatt plant (Germany): Production of first all-electric compact SUV EQA started - also at Beijing plant (China) in 2021
Mercedes-Benz plant in Kecskemét (Hungary): Decision to locate second all-electric compact SUV EQB. Production launch in 2021 - also at Beijing plant (China)
Mercedes-Benz Bremen plant: Production launch of electric EQE business sedan in 2021 - at Beijing plant soon thereafter (China)
Mercedes-Benz Tuscaloosa plant (USA): SUV variants EQS und EQE begin in 2022
Mercedes-Benz battery production network: Production start of battery systems for EQS and EQE in Untertürkheim/Hedelfingen (Germany) imminent. Production of compact SUV battery systems in Kamenz (Germany), Jawor (Poland) and Beijing (China) plants. Tuscaloosa battery plant will produce batteries for SUV variants of EQS and EQE beginning 2022
15 December 2020, Stuttgart. Mercedes-Benz is targeting leadership in electric drives and vehicle software. The consistent electrification of the entire product portfolio is a key element of the strategic focus "Ambition 2039" and a prerequisite on the way to CO₂ neutrality. In 2022 the portfolio includes eight all-electric Mercedes-EQ models. The global Mercedes-Benz production network is ready for the company’s electric product offensive and is integrating its Mercedes-EQ models into series production in its existing plants.
Markus Schäfer, Member of the Board of Management of Daimler AG and Mercedes-Benz AG; responsible for Daimler Group Research and COO Mercedes-Benz Cars: “With its ‘Electric First’ strategy, Mercedes-Benz is consistently on the path to CO₂ neutrality and is investing heavily in transformation. Our vehicle portfolio becomes electric and thus also our global production network with vehicle and battery factories. We intend to lead in the field of e-mobility and focus in particular on battery technology. We are taking a comprehensive approach, ranging from research and development to production, and also including strategic cooperation.”
The EQS, the first electric luxury sedan from Mercedes-Benz, will start in the first half of 2021 in Factory 56 at the Sindelfingen site (Germany). With the production launch of the electric compact SUV EQA at the Rastatt plant (Germany) and the current decision to locate EQB production in the Hungarian plant in Kecskemét, the company is taking further important steps toward making its product portfolio CO₂ neutral. The course has also been set toward “Electric First” in the global powertrain production network as well. High-efficiency battery systems will also be manufactured and assembled within the production network.
Jörg Burzer, Member of the Board of Management of Mercedes-Benz AG, Production and Supply Chain: “The Mercedes-Benz production network is global, digital and flexible, and ready for the upcoming electric offensive – thanks, of course, to our highly qualified and motivated employees worldwide. We are now beginning a real Mercedes-EQ fireworks display. Six electric product launches by 2022 underscore the strength and competence of our Mercedes-Benz production sites worldwide. The production network will have a total of six Mercedes-EQ car locations. Local production of highly efficient battery systems plays a central role in the Mercedes-Benz strategy - coupled with a comprehensive sustainability concept that spans the entire life cycle of the battery all the way to recycling.”
Mercedes-Benz vehicle plants consistently implement electric offensive
In May 2019 production of the EQC (combined power consumption: 21.5 kWh/100 km; combined CO₂ emissions: 0 g/km) at the Mercedes-Benz plant in Bremen (Germany) was integrated into ongoing series production. Just a few months later the German-Chinese production joint venture, Beijing Benz Automotive Co. Ltd. (BBAC), launched EQC production for the local market in China. In 2020 production of the EQV premium electric MPV (combined power consumption: 26.4 kWh/100 km; combined CO₂ emissions: 0 g/km)1 started in Vitoria, northern Spain.
Compact car class customers can look forward to two fully electric compact SUVs in the EQA and EQB in 2021. EQA will celebrate its world premiere on January, 20 2021 as the first fully electric derivative of this compact car. The EQA production launch at the Mercedes-Benz Rastatt plant went smoothly. As with the EQC from Bremen and Beijing and the EQV from Vitoria, which are already on the market, the fully electric models at the Rastatt plant run on the same production line as compact vehicles with conventional and hybrid drives. That means all five vehicles produced in Rastatt are electrified: In addition to the fully electric EQA, the AClass, A-Class sedan, B-Class and the compact SUV GLA are also produced at the Mercedes-Benz plant in Rastatt - with classic combustion engines as well as plug-in hybrid drive. With that the Mercedes-Benz Rastatt plant is making an important contribution on the road to a CO₂ neutral vehicle fleet and to the Mercedes-Benz AG electric offensive. EQA production will also follow next year (2021) at BBAC in Beijing for the Chinese market.
EQB production will launch in 2021 at two locations in the global Mercedes-Benz Cars production network: in the Hungarian Mercedes-Benz plant in Kecskemét for the world market and in the German-Chinese joint venture BBAC in Beijing for the local market. Plant preparation, including employee training and renovation work, is already underway. The compact SUV EQB will be the first purely electrically powered production vehicle from Hungary and will complement the plug-in hybrid portfolio consisting of the CLA and CLA Shooting Brake. The A-Class will also be produced in Kecskemét with a plug-in hybrid drive, in addition to production in the German Mercedes-Benz plant in Rastatt.
Furthermore, in the first half of 2021 production of the EQS electric luxury sedan will begin in Factory 56 at the Mercedes-Benz plant in Sindelfingen (Germany). EQS is the independent, fully electric member in the new S-Class program and is the first to use the new electric architecture for luxury and upper-class electric vehicles at Mercedes-Benz. In Factory 56 the S-Class and, in the future, the Mercedes-Maybach S-Class, and the EQS will be produced in a fully flexible manner on the same line. Factory 56 embodies the future of production at Mercedes-Benz and sets new standards for automobile construction. In Factory 56 efficiency gains of around 25 percent are achieved compared to the previous S-Class assembly. This is made possible by optimizing the entire value chain and full digitalization with MO360, the digital Mercedes-Benz production ecosystem. For further information on this: https://media.daimler.com/marsMediaSite/ko/en/47014243
Furthermore, the Mercedes-Benz plant in Bremen will begin production of the EQE business sedan in the second half of 2021, followed shortly thereafter at the Beijing plant. The EQE thus complements the allelectric portfolio of the two plants. The Beijing plant will then produce a total of four Mercedes-EQ models for the local market.
The Mercedes-Benz plant in Tuscaloosa (USA) is also preparing for production of the EQE SUV and EQS SUV in 2022, which will be produced in the future on the same line with SUVs with conventional and plug-in hybrid drives.
In 2022 a total of eight Mercedes-EQ electric vehicles will be produced at seven locations on three continents. This is possible because the company made early investments worldwide in flexibility and technical equipment with future-oriented Industry 4.0 solutions. In the Mercedes-Benz AG plants, vehicles with different drive types can be produced in parallel thanks to highly flexible structures. With a view to the strategic goal of generating more than half of sales with so-called xEVs, i.e. plug-in hybrids and electric vehicles, from 2030 on and gradually increasing the purely electric share, the high degree of flexibility is a decisive advantage. It enables production to be adjusted at short notice depending on market demand.
smart rounds off the electric Mercedes-Benz Cars portfolio with three additional models. The smart EQ fortwo (combined power consumption: 16.5 kWh/100 km, combined CO₂ emissions: 0 g/km)1 and smart EQ fortwo Cabrio (combined power consumption: 16.8 kWh/100 km, CO₂ emissions combined: 0 g/km)1 are produced in Hambach, France, and the smart EQ forfour (combined power consumption: 17.3 kWh/100 km; combined CO₂ emissions: 0 g/km)1 in Novo Mesto, Slovenia. The next generation of smart electric vehicles will be produced by the joint venture smart Automobile Co., Ltd. in China. This is a joint venture of MercedesBenz AG and the Zhejiang Geely Group (Geely Holding).
Plug-in hybrid drive is important as a key technology and intermediate step toward a purely electric product portfolio. More than 20 plug-in hybrid model variants are already an integral part of the Mercedes-Benz product portfolio. The portfolio will be expanded to include more than 25 model variants by 2025. Their production therefore also plays an important role in the global production network. Plug-in hybrid vehicles are already rolling off Mercedes-Benz Cars assembly lines in almost all car plants.
Global battery production network: a key success factor in the Mercedes-Benz electric offensive
The batteries for the Mercedes-EQ electric vehicles are supplied by a global battery production network with plants on three continents. Local battery production is a key success factor for the Mercedes-Benz electric offensive.
Two plants in Kamenz (Germany), have been producing battery systems for hybrids, plug-in hybrids and electric vehicles since 2012. The second battery factory at the site began operations in 2018 and has been producing the EQC's battery systems since 2019. It was designed from the start as a CO₂ neutral plant and combines, among other things, solar energy, geothermal energy and a combined heat and power plant. The battery systems for the EQA have also recently rolled off the production line at the site. Since the start of production at Accumotive, more than a million batteries based on lithium-ion technology for electric, plug-in hybrid vehicles and 48-volt systems have been produced at the Kamenz site.
Mercedes-Benz and BAIC have jointly set up local battery production at the existing location in the Yizhuang Industrial Park in Beijing (China). This supplies the nearby vehicle plant, which has also added all-electric Mercedes-EQ models to its portfolio with the EQC. Production of battery systems for the EQC started there in 2019. With the start of production of the EQA, EQB and EQE, the plant will manufacture battery systems for a total of four Mercedes-Benz EQ models beginning in 2021.
This year the battery plant in Jawor (Poland) started producing plug-in hybrid batteries for the C, E and SClasses. In the coming year the location will expand its portfolio to include battery systems for the compact Mercedes-EQ models, the EQA and the EQB. Much like the battery plant in Kamenz, the plant was designed from the outset for CO₂ neutral production.
In the future at the Untertürkheim (Germany) site two plants will produce battery systems. Final preparations for the production of the battery systems for the EQS, which will roll off the production line in nearby Sindelfingen in the first half of 2021, are currently underway at the Hedelfingen plant. The battery system for the EQE will also be produced in Hedelfingen. Another battery plant is currently being built in the Brühl facility, which will manufacture battery systems for Mercedes-Benz plug-in hybrids starting 2022. The work on the building has already been completed. The battery plant in Brühl will be fitted with the corresponding equipment in the coming months.
Production of the EQS and EQE SUV models will start in 2022 at the Mercedes-Benz plant in Tuscaloosa (USA). A battery plant is currently being built in the immediate vicinity and will supply highly efficient battery systems for both models. Work on the building has already been completed. The ultra-modern systems will be installed in the coming months.
In addition, the Mercedes-Benz production strategy currently provides for another battery plant at the Sindelfingen site.
Together with local partner Thonburi Automotive Assembly Plant (TAAP), Mercedes-Benz Cars set up a battery production facility in Bangkok (Thailand) and began operations in 2019. Battery systems for the current C, E and S-Class plug-in hybrids are manufactured at the site. Preparations are also being made there to manufacture drive batteries for all-electric Mercedes-EQ brand vehicles.
Electric First und Ambition2039: CO₂ neutral mobility und production
Under “Electric First,” Mercedes-Benz is pursuing the consistent electrification of all model variants and vehicle types as a clear objective. The decisive factor here over the next few years is the gradual increase in the purely electric share of the vehicle portfolio. So-called xEVs, plug-in hybrids and fully electric vehicles, should account for more than half of sales by 2030 - and the trend is rising. Electrically powered vehicles from Mercedes-Benz are enjoying increasing popularity. The company delivered a total of 45,000 electric vehicles and plug-in hybrids (xEVs) worldwide in the third quarter of 2020.
With “Ambition2039,” Mercedes-Benz introduced its path to CO₂ neutrality over a year ago. Vehicle production plays a crucial role in this regard. As early as 2022 the company’s Mercedes-Benz car and van plants will produce CO₂ neutrally around the world. This includes more than 30 car and van plants, as well as battery plants.
Brief interview
“We’re producing the Mercedes-EQ models the Mercedes way: Completely digital and flexible, highly efficient and maximally sustainable.”
Questions for Jörg Burzer, Member of the Board of Management of Mercedes-Benz AG, Production and
Supply Chain
Mr. Burzer, are you equipped for the production of electric vehicles in your production network?
The Mercedes-EQ production network is ready for our electric offensive. We started this transformation several years ago and set up our plants with maximum flexibility. The Mercedes-EQ electric models are gradually being integrated into our existing vehicle plants worldwide. They come off the same lines as vehicles with combustion engines or plug-in hybrid drives. The same applies to all of our Mercedes-Benz car plants - a total of six on three continents. This concept is particularly advantageous because demand for electric and electrified vehicles is developing very differently by region and we can adjust our production planning accordingly on short notice. In this way we can manufacture exactly what our customers want.
What specifically does your production planning for the upcoming model offensive look like?
One thing is certain: the proportion of all-electric vehicles in our portfolio will increase sharply in the coming years. By 2030 more than fifty percent of our vehicles will roll off the assembly line as so-called xEVs. Plug-in hybrids and hybrids will therefore continue to play an important role in our production planning over the next few years. However, our target is clearly designed for 100 percent Mercedes-EQ and we are directing our capacity precisely in this direction. We are preparing our production, as well as our employees, step by step for this change. Our sustainability concept is also a central focus: from 2022 on we will produce CO₂ neutral in our Mercedes-Benz plants worldwide.
What, specifically, were the challenges?
Every vehicle launch during ongoing production comes with challenges. That, of course, also applies to electric vehicles. However, thanks to the know-how in our plants and cross-location system planning, we could quickly develop and implement flexible solutions. The consistent digitalization of our processes through our digital production ecosystem MO360 also made a significant contribution. An important factor here, of course, is attaining targeted qualifications for our colleagues in our plants, which we consistently promote.
How will powertrain production continue in the future?
For the global Mercedes-Benz powertrain production network, the shift toward e-mobility poses a special challenge. However, we are determined to continue aligning our drive division to this change and make it sustainable for the future. We have already built up extensive know-how in our powertrain plants in recent years. It starts with the expansion of our battery production network and includes, among other things, manufacturing and assembling parts of the electric drivetrain ourselves. Still, it’s also clear that the drivetrains of the future will differ significantly from those of today.
You will manufacture the batteries for the Mercedes-EQ models in house?
The local production of batteries is an essential success factor in our electric offensive. With a view to steadily increasing demand and, in accordance with our production planning, we are setting up our global battery production network to be flexible worldwide. Today we already produce batteries in Kamenz, Bangkok and Beijing. The ramp-up of our battery plants in Hedelfingen and Jawor is imminent and our colleagues in Brühl and Tuscaloosa are already preparing to start production in 2022. Our production network is very well positioned for the Mercedes-EQ model offensive.
Which new electric model are you personally most looking forward to?
Basically, I look forward to every new Mercedes-Benz. A very special milestone is certainly the upcoming EQS production launch. It will roll off the assembly line, together with the S-Class, in our new Factory 56 at the Mercedes-Benz plant in Sindelfingen. Here we’re setting the course for our entire production network: With the most modern production technologies Factory 56 is a blueprint for our global network. At the same time, it bolsters our claim - the Mercedes way - to the production of the Mercedes-EQ models: completely digital and flexible, highly efficient and maximally sustainable.
Ford's Mustang Mach-E: An In-Depth Look with the Designers
Cars are so good these days that we often fail to understand the planning, design and engineering that goes into our personal transport. This great video from Ford dives in-depth with the company’s designers, looking at the exterior design, Ford SYNC and connectivity, the interior design and performance and charging.
Cars are so good these days that we often fail to understand the planning, design and engineering that goes into our personal transport. This great video from Ford dives in-depth with the company’s designers, looking at the exterior design, Ford SYNC and connectivity, the interior design and performance and charging.
Also worth watch is Jay Leno’s introduction to the Mach-E and the 7-motor (!) 1400hp Mach-E below.
The Mach-E is expected to go on sale in the US in the first quarter of 2021; sadly Ford has no plans to bring the Mach-E to Australia.
Hyundai's New 'E-GMP' Platform to Underpin Future BEVs
Designed exclusively for electric vehicles, the E-GMP platform architecture marks an engineering step change from Hyundai. With the company’s current range of EVs based on platforms designed for internal combustion engines, The E-GMP platform provides increased development flexibility, powerful driving performance, increased driving range, strengthened safety features, and more interior space for occupants and luggage according to Hyundai.
Designed exclusively for electric vehicles, the E-GMP platform architecture marks an engineering step change from Hyundai. With the company’s current range of EVs based on platforms designed for internal combustion engines, The E-GMP platform provides increased development flexibility, powerful driving performance, increased driving range, strengthened safety features, and more interior space for occupants and luggage according to Hyundai.
During an online digital discovery event, Albert Biermann, President and Head of R&D Division for Hyundai Motor Group. stated “Today our front-wheel driven Hyundai and Kia BEVs are already among the most efficient ones in their segments. With our rear-wheel driven based E-GMP, we are extending our technological leadership into segments where customers demand excellent driving dynamics and outstanding efficiency.”
According to Hyundai, E-GMP reduces complexity through modularisation and standardisation, allowing rapid and flexible development of products which can be used across most vehicle segments, such as sedans, SUVs and CUVs.
Hyundai claims that future vehicles based on E-GMP architecture can provide range over 500km on a full charge (WLTP) and be charged up to 80% within 18 minutes through high-speed DC charging.
E-GMP will be based on an 800V system architecture, while also allowing 400V charging. The company claims a world first for this multi-charging system, which operates the motor and the inverter to boost 400V to 800V for stable charging compatibility.
Hyundai plans to showcase a flexible charging system through its Integrated Charging Control Unit (ICCU). This unit allows bidirectional charging, and enables a new vehicle-to-load (V2L) function up to 3.5kW, which can additionally discharge energy from the vehicle battery without additional components. Hyundai claims this enables any BEV based on the E-GMP to operate other electric machinery, charge another EV, or operate “a mid-sized air conditioner unit and a 55-inch television for up to 24 hours.”
You can read the full press release below:
2 December, 2020 – Hyundai Motor Group has unveiled its new Electric-Global Modular Platform (E-GMP), a dedicated Battery Electric Vehicle (BEV) platform. Revealed online today during an ‘E-GMP Digital Discovery’ event, the platform will serve as the core technology for Hyundai Motor Group’s next-generation BEV line-up.
The event was broadcasted through the Group’s official YouTube channel and Channel Hyundai, an online global content platform.
From 2021, the E-GMP will underpin a range of dedicated new BEVs, including Hyundai Motor Company’s IONIQ 5; Kia Motors Corporation’s first dedicated BEV to be revealed in 2021; and a series of other models.
Designed exclusively for BEVs, E-GMP provides various advantages compared to the Group’s existing platforms, which have each been engineered predominantly to accommodate internal combustion engines. Benefits include increased development flexibility, powerful driving performance, increased driving range, strengthened safety features, and more interior space for occupants and luggage.
“Today our front-wheel driven Hyundai and Kia BEVs are already among the most efficient ones in their segments,” said Albert Biermann, President and Head of R&D Division for Hyundai Motor Group.
“With our rear-wheel driven based E-GMP, we are extending our technological leadership into segments where customers demand excellent driving dynamics and outstanding efficiency.”
“E-GMP is the culmination of years of research and development and brings together our most cutting-edge technologies. Our BEV line-up will evolve and be strengthened by this innovative new platform,” said Fayez Abdul Rahman, Senior Vice President of Vehicle Architecture Development Center for Hyundai Motor Group.
Maximising development flexibility through modularisation and standardisation
E-GMP reduces complexity through modularisation and standardisation, allowing rapid and flexible development of products which can be used across most vehicle segments, such as sedans, SUVs and CUVs. Moreover, flexible development can satisfy various customer needs for vehicle performance. Among these, a high performance model will accelerate from 0 to 100kph in less than 3.5 seconds and achieve a maximum speed of 260km/h.
E-GMP will be highly effective in expanding the Group’s EV leadership position as it will enable the company to enlarge its EV line-up over a relatively short period through modularisation and standardisation.
Designed for Driving Performance, Safety and Maximised Space
E-GMP is engineered to offer improved cornering performance and driving stability at high speed. This is due to optimal weight distribution between front and rear, a design which enables a low centre of gravity thanks to its low-mounted battery pack, and the adoption of electric motors located in the space previously occupied by an engine.
The high-speed electric motor raises the driving performance of E-GMP vehicles. A five-link rear suspension system, which is typically used for mid and large sized vehicle segments, and the world’s first integrated drive axle (IDA), which combines wheel bearings with the drive shaft to transmit power to the wheels, enhance ride comfort and handling stability.
The platform secures battery safety through a battery support structure made of ultra-high strength steel. Hot-stamped steel components surround this structure for additional rigidity. Collision energy can be absorbed efficiently thanks to energy-absorbent sections of the body and chassis, effective energy load paths, and a central section of the battery pack tightly bound to the vehicle body.
Moreover, by strengthening the structure of the load support section, located in front of the dashboard, engineers have been able to minimise collision energy to the power electric system and battery. The A-pillar’s load distribution structure also prevents deformation of the passenger cell.
E-GMP maximises interior space through its long wheelbase, short front and rear overhangs and slim cockpit module. With the battery pack mounted beneath the floor, the E-GMP creates a flat floor for the cabin. This provides more legroom for passengers, while enabling various arrangements for the front and rear seats.
The battery pack itself - mounted between the front and rear wheel axles - will be the most power-dense system that Hyundai Motor Group has ever created. This is partly thanks to its enhanced cooling performance, a result of a new separate cooling block structure which helps make the battery pack more compact. With energy density enhanced by around 10% compared to existing EV battery technology, the battery packs are lighter, can be mounted lower in the body, and liberate more cabin space.
Efficient and Powerful Electrification System
The E-GMP’s compact new power electric (PE) system consists of a powerful motor, EV transmission and inverter. These three components are integrated into a single compact module. This ensures powerful performance by raising the motor’s maximum speed by up to 70% compared to existing motors. The high-speed motor is smaller than other motors while providing comparable performance, and it gives efficiencies in both space and weight.
Additionally, a standardised battery system can be tuned to offer performance appropriate for a specific vehicle segment, to maximise driving range, or to meet various customer needs.
The motor is controlled by the inverter power module, which adopts silicon carbide (SiC) semiconductors. This motor can enhance system efficiency by around 2-3 percent, which means the vehicle can be driven for approximately 5% longer on the same battery energy.
E-GMP relies on the rear wheel for propulsion. Customers will be able to choose between rear-wheel and all-wheel drive configurations; models with the latter can be equipped with an additional motor. The all-wheel drive system includes an EV transmission disconnector, which can control the connection between the additional motor and front wheels, and switch between two-wheel and all-wheel drive modes to enhance efficiency by offering the ideal level of power or performance for current driving conditions.
All vehicles developed with the E-GMP platform use a standardised single type of battery module. This module is composed of pouch-type standard cells and can be packed in different quantities as required for each vehicle.
Multi (800V and 400V) and Bi-Directional Charging System
Most existing EVs and the fast-charging infrastructure provide 50kW-150kW charging for EVs equipped with a 400V system; however, the development of 800V infrastructure, with up to 350kW charging, will gradually enable even more fast-charging.
In line with this trend, Hyundai Motor Group has invested in IONITY, Europe’s leading high-power charging network, as a strategic partner and shareholder. IONITY operates 308 high-power charging (HPC) stations - using a charging capacity of up to 350 kW - along highways in European countries. The company plans to increase this number to 400 HPC stations by 2022, including 51 currently under construction.
E-GMP offers 800V charging capability as standard and enables 400V charging, without the need for additional components or adapters. The multi-charging system is a world’s first patented technology which operates the motor and the inverter to boost 400V to 800V for stable charging compatibility.
A BEV based on E-GMP is capable of a maximum range of over 500km with a fully charged battery, according to the Worldwide Harmonised Light-duty vehicle Procedure (WLTP). Moreover, it can high-speed charge up to 80% in just 18 minutes and can add up to 100km of driving range in just five minutes.
Unlike previous BEVs, which only accept one-way charging, the E-GMP’s charging system is more flexible. The E-GMP’s newly developed Integrated Charging Control Unit (ICCU) represents an upgrade from existing On-Board Chargers (OBC), which typically only allow electricity to flow in a single direction from an external power source. The ICCU enables a new vehicle-to-load (V2L) function, which can additionally discharge energy from the vehicle battery without additional components. This enables BEV based on the E-GMP to operate other electric machinery (110 / 220V) anywhere. The system can even be used to charge another EV.
The new V2L function can supply up to 3.5kW of power and operate a mid-sized air conditioner unit and a 55-inch television for up to 24 hours.
E-GMP to underpin future EV sales growth worldwide
Hyundai Motor Group has put in considerable effort to prepare for the era of electrification. Kia Motors Corporation launched its first mass-produced BEV in 2011, the Ray EV, in Korea, with the Soul EV sold in global markets from 2014. The Group completed the introduction of a mass production system for all electrified vehicles in 2015, including those with HEV, PHEV, BEV, and FCEV.
The E-GMP will underpin Hyundai Motor Group’s plans to introduce a total of 23 BEV models including 11 dedicated BEV models, and sell more than 1 million BEVs worldwide by 2025. As part of its BEV vision, Hyundai Motor Company launched its dedicated ‘IONIQ’ BEV brand in August 2020, which includes three dedicated BEV models, the IONIQ 5, IONIQ 6 and IONIQ 7 by 2024. This currently covers various vehicle segments.
Kia is also undergoing a transformation for the era of electrification, based on its ‘Plan S’ mid-to-long term strategy. In September, Kia announced plans to increase the share of BEV sales volumes as a proportion of total sales to 20% by 2025. The company also recently published an early image of seven dedicated BEV models to be released sequentially by 2027.
GM Grows EV Investment to $27bn, Charges Ahead Toward Electric Future
On Thursday, GM announced an addition $7 billion will be invested in the company’s electrification and autonomy program, hopefully accelerating the US automaker to the forefront of battery, electric vehicle drivetrain and autonomous technology.
On Thursday, GM announced an addition $7 billion will be invested in the company’s electrification and autonomy program, hopefully accelerating the US automaker to the forefront of battery, electric vehicle drivetrain and autonomous technology.
"Climate change is real, and we want to be part of the solution by putting everyone in an electric vehicle," said GM Chief Executive Mary Barra.
"We are transitioning to an all-electric portfolio from a position of strength and we're focused on growth."
GM’s EV platform will underpin the majority of its brands’ architecture over the next decade.
GM Estimates 40% of it’s model range will be electrified by mid-decade, and the company is currently developing new Ultium-based battery packs with claimed efficiency gains, a 450mi range, and cost savings of 60% over current battery technology used by GM’s brands. Some battery highlights include:
Cell design that enables higher energy density and uses less non-active material, making more room for the part of the battery that produces energy.
Manufacturing efficiencies through GM’s Ultium Cells LLC joint venture with LG Chem.
Better integration between vehicles and their battery packs, enabling fewer cells and modules.
Less expensive cathodes, reduced active material, novel electrolytes and the first use of lithium metal anodes in a GM battery.
No official EPA testing has verified these range claims, and much of the industry is still cautious about GM’s ability to produce competitive cells.
The capital spend is welcome however, and represents an important shift in the company; for the first time, investment in electrification outweights investment in combustion engine technology.
Full press release below.
Source: GM
GM’s new Ultium Battery Cells. Image: GM
Thirty new global EV launches planned through 2025
More than $27 billion in planned EV and AV product spending to exceed GM’s gas and diesel investment
By mid-decade, GM’s Ultium battery packs projected to cost 60 percent less than today’s packs with twice the energy density
GM ups full-charge maximum range of Ultium-based EVs to 450 miles
DETROIT – General Motors Co. (NYSE: GM) Chairman and CEO Mary Barra revealed that the company will offer 30 all-electric models globally by mid-decade. Forty percent of the company’s U.S. entries will be battery electric vehicles by the end of 2025. Barra also announced an increase in GM’s financial commitment to EVs and AVs today to $27 billion through 2025 – up from the $20 billion planned before the onset of the COVID-19 pandemic.
“Climate change is real, and we want to be part of the solution by putting everyone in an electric vehicle,” said Barra. “We are transitioning to an all-electric portfolio from a position of strength and we’re focused on growth. We can accelerate our EV plans because we are rapidly building a competitive advantage in batteries, software, vehicle integration, manufacturing and customer experience.”
At the virtual Barclays Global Automotive Conference, Barra and Doug Parks, GM executive vice president of Global Product Development, Purchasing and Supply Chain, will share key elements of GM’s plan, including:
By 2025, GM will launch 30 EVs around the world, and more than two-thirds will be available in North America. Cadillac, GMC, Chevrolet and Buick will all be represented, with EVs at all price points for work, adventure, performance and family use.
Engineering advances have increased the previously stated GM-estimated maximum range of Ultium-based vehicles from 400. GM’s Ultium-based EVs, when produced, will be capable of driving ranges up to 450 miles on a full charge1.
GM’s versatile Ultium platform provides the building blocks for everything, from mass market to high performance vehicles – all from a single, common cell in most markets and a set of interchangeable propulsion components.
More than half of GM’s capital spending and product development team will be devoted to electric and electric-autonomous vehicle programs.
GM’s second-generation Ultium chemistry is projected to deliver twice the energy density at less than half the cost of today’s chemistry. GM is already prototype testing this next-generation technology, which is expected to be available mid-decade.
Ultium technology, supported by hundreds of granted patents and pending patent applications, is expected to bring EVs closer to price parity with gas-powered vehicles.
Both the GMC HUMMER EV and Cadillac LYRIQ programs were accelerated, along with other vehicles to be revealed at a later date.
GM is hiring 3,000 electrical system, infotainment software and controls engineers, plus developers for Java, Android, iOS and other platforms.
GM continues to explore third-party licensing for its Ultium EV architecture, batteries and propulsion systems, along with its Hydrotec fuel cell technology developed with Honda.
GM, in collaboration with its dealers, will leverage its sales and service capabilities and software-powered innovations to deliver an exceptional customer experience for EV loyalists and new EV customers alike.
GM innovates in EV propulsion despite COVID-19
Ultium already represents a milestone achievement in electrification, with battery pack costs nearly 40 percent lower than those in the Chevrolet Bolt EV. Despite the pandemic, GM’s work on EVs accelerated during 2020.
Now, just eight months after the technology was first revealed, GM is projecting that second-generation Ultium packs, expected mid-decade, will cost 60 percent less than the batteries in use today with twice the energy density expected.
These second-generation cells will get closer to cost parity with gas-powered engines due to:
Cell design that enables higher energy density and uses less non-active material, making more room for the part of the battery that produces energy.
Manufacturing efficiencies through GM’s Ultium Cells LLC joint venture with LG Chem.
Better integration between vehicles and their battery packs, enabling fewer cells and modules.
Less expensive cathodes, reduced active material, novel electrolytes and the first use of lithium metal anodes in a GM battery.
GM has completed hundreds of test cycles on the multi-layer prototypes of this next-generation Ultium cell chemistry. Production cells are expected by mid-decade.
The Ultium platform is flexible enough to accept new chemistry and even cell types, without redesigns to its architecture. Ultium batteries will be easy to service at the module level, which makes repair costs less expensive than having to replace the whole pack.
“GM’s EV development times are speeding up and costs are going down rapidly, so we expect our Ultium EV programs to be profitable from the first generation on,” said Parks. “It’s not just the cost and performance of our innovative EV components that will give us a competitive advantage in a fast-changing industry, but how we integrate them with other advanced systems like Super Cruise, our Vehicle Intelligence Platform electrical architecture and other technologies pioneered in our traditional portfolio.”
GM is doing most of the development work on these cells internally at its Chemical and Materials Systems Lab, located at the Global Technical Center in Warren, Michigan. This facility features a fabrication line with polymer mixing, slurries, a coating machine and a cell assembly room.
Next year, GM will break ground on an all-new Battery Innovation Lab and Manufacturing Technology Center to develop the next-generation Ultium battery chemistry.
GM speeds its EV rollout and pace of innovation
The modular and highly flexible qualities of the Ultium system, along with engineering advances in battery technology, the use of virtual development tools and lessons learned during the HUMMER EV development process, have enabled GM to bring EVs to market much faster than originally planned.
The 2022 GMC HUMMER EV’s development time of 26 months – down from about 50 months – is now the benchmark.
The development schedules for 12 vehicle programs have been moved up, including:
GMC HUMMER EV
Three other GMC Ultium variants, including an EV pickup
Four Chevrolet EVs, including a pickup and compact crossover
Four Cadillacs
In addition, Buick’s EV lineup will include two Ultium-based EVs.
After the GMC HUMMER EV, the next EV to launch will be the LYRIQ, Cadillac’s first all-electric vehicle, which will arrive in the first quarter of 2022, nine months ahead of schedule.
“Ultium is already changing the way customers – and investors – view our company,” Barra said. “We are resolved as a management team to move even faster to expedite the transition to EVs. The all-electric future we are building integrates all the things we do better than anybody else – so we can put everyone in an EV, generate profitable growth and create shareholder value.”